Preventing Oscillation and Overtravel in Servo-Controlled Axes
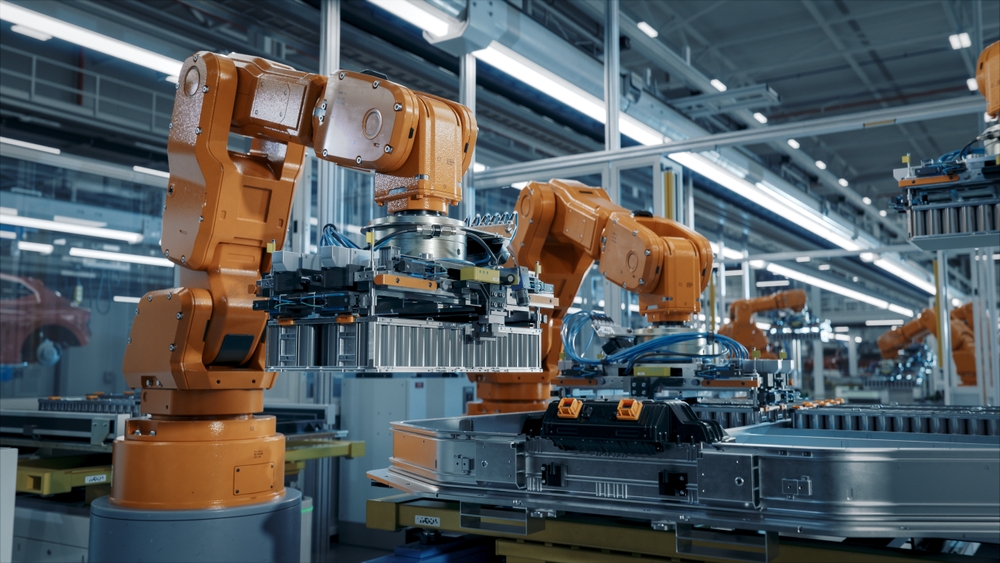
A CNC machine starts producing parts with inconsistent surface finishes. A packaging line begins overshooting its target positions. An assembly robot develops an unexpected tremor during precise movements. These problems often get blamed on “bad tuning,” but oscillation and overtravel in servo-controlled axes usually stem from deeper issues. True prevention requires understanding the mechanical and electrical factors that create instability — not just adjusting gain settings until symptoms disappear.
Why tuning alone fails to fix servo problems
Most maintenance teams reach for the tuning software when servo axes start misbehaving. They adjust gain settings, tweak response parameters, and sometimes manage to mask the symptoms temporarily. But aggressive tuning often creates new problems under different operating conditions. A servo that stops oscillating with light loads may become unstable when handling heavier parts.
The real issue is that tuning can’t fix mechanical problems. When couplings wear out, bearings develop play, or mounting systems lose rigidity, no amount of parameter adjustment will restore proper performance. These mechanical changes alter how loads transfer through the system, creating conditions that even perfectly tuned servos can’t handle.
This is why the same machine that ran flawlessly for months suddenly develops positioning problems after a tooling change or temperature shift. The mechanical reality has changed, but the control system is still trying to operate with outdated assumptions about system behavior.
How mechanical and electrical problems feed each other
Servo instability develops when mechanical issues interact with electrical control systems in unpredictable ways. A worn coupling doesn’t just create backlash — it introduces cyclic loads that confuse feedback systems. The servo tries to compensate for these mechanical inconsistencies, often creating oscillation around target positions.
Similarly, foundation flexibility allows unwanted movement that shows up as positioning errors. The encoder reports one position while the actual tool location differs due to structural deflection. The controller responds to this false information by making corrections that actually make the problem worse.
Load changes compound these issues. Adding weight to a machine or changing fixtures alters the inertia characteristics that the servo system expects. What appears to be an electrical control problem often traces back to mechanical factors that have shifted since the original tuning was performed.
Temperature variations add another layer of complexity. Bearing friction changes with temperature, affecting how smoothly axes move. Thermal expansion alters mechanical clearances. These changes happen gradually, making them easy to miss until servo performance degrades noticeably.
Building stability through systematic prevention
Preventing servo problems requires addressing mechanical and electrical factors as an integrated system. Start with the mechanical foundation:
- Make sure couplings are properly aligned and in good condition.
- Verify that mounting systems provide adequate rigidity.
- Check that lubrication systems maintain consistent friction characteristics.
Next, focus on feedback system integrity. Encoders and position sensors must provide accurate, noise-free signals. Electrical interference, loose connections, or damaged cables create false position information that triggers unwanted control responses. Regular feedback system testing catches these problems before they affect production.
Finally, match tuning parameters to actual operating conditions rather than ideal test scenarios. Use filtering and damping strategies to isolate the servo system from mechanical variations. Implement smooth motion profiles that minimize dynamic stresses. Remember: The goal is stable performance across the full range of operating conditions, not just optimal response under perfect circumstances
Stable servos start with systematic prevention
Preventing oscillation and overtravel means addressing root causes rather than chasing symptoms. Operations that focus only on tuning parameters will find themselves constantly fighting the same problems. Those that take a systematic approach to servo stability will benefit from consistent performance, reduced maintenance demands, and the ability to push equipment to higher speeds and accuracies.