Manufacturing Challenges, Problems and Solutions
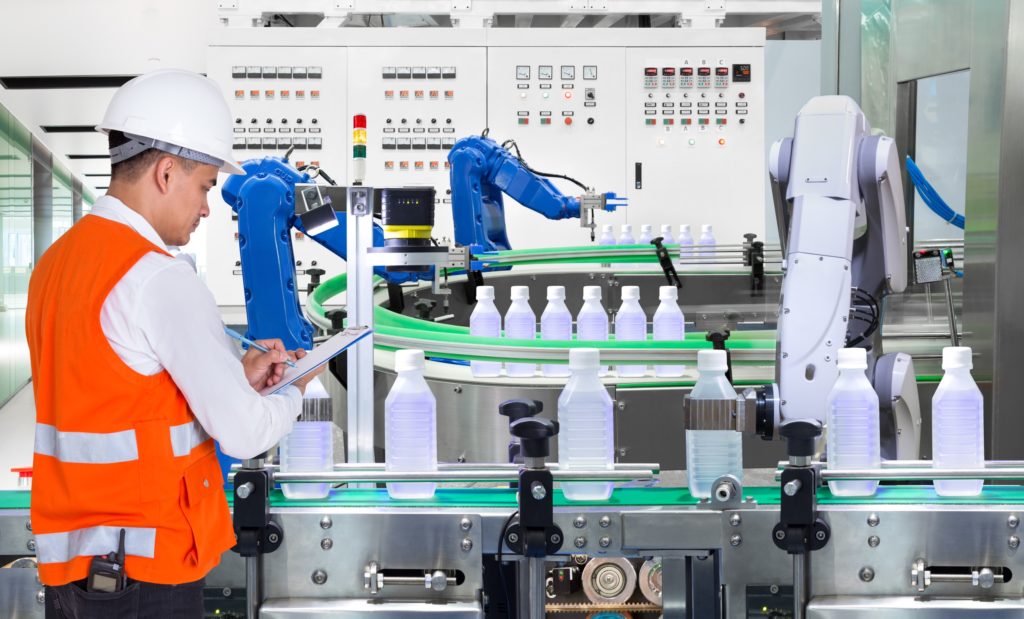
What are Common Manufacturing Problems?
When your job is to create and sell a quality manufacturing item, you’re going to have to deal with challenges. Challenges that spring up unexpectedly, often at the wrong moment and involve a great deal at stake for you and your company. It’s your job to consistently deliver a product that meets high-quality standards. Often you need to navigate a confusing supply chain, unrealistic expectations of your C-suite bosses, as well as time-to-market deadlines that demanding customers drive. And then there are seasonal demands.
Let’s not forget the reality that your product is following a process where all the important factors like design, cost and the amount of time you have to get the project done were set when the project first began. And again, maybe it’s a new product and you have no idea how long the above factors are going to take.
We want to look at some of the manufacturing industry challenges and problems almost all manufacturers face, as well as some potential solutions.
Supply Chain Issues
Increasingly manufacturers are counting on global suppliers for the raw materials they need or to build components needed to complete the manufacture of their products. But when you add additional parties to your supply chain, such as contractors or vendors or other parties, this greatly increases the chances of miscommunication and error. When you have production taking place in different locations across the country, or even around the globe, and different teams working on components of one product, you need to make sure your supply chain is working properly.
Scheduling for the completion of the project often lies in the hands of one person. While this allows that one person to have a 30,000-foot view of what’s taking place, the problem is that their team and teams that may be working around the country or the globe don’t really know where they are in the process. Manual updates aren’t the answer – such as everyone emailing everyone else to let them know what’s going on – because they don’t take into account the rate of change.
Meanwhile, priorities in the process shift and other unseen events occur that affect production or shipping. Without an effective means of communicating what’s taking place, there is practically no way for all the teams working on the project to see these changes reflected in the schedule and give them the opportunity to react in a timely manner.
Here are some potential solutions:
- Use a collaborative project management tool that allows everyone involved in the project to see what’s going on. This means all those involved can access the schedule at any time to see how the project is progressing and stay up-to-date on any important information.
- Within the next three years, about one-third of all manufacturing supply chains will be using analytics-driven cognitive capabilities. This could help reduce costs by 10 to 15 percent. Such a move will allow supply chains to use data generated by the Internet of Things (IoT) to give real-time insights into how they are working. Having access to this real-time data also help improve performance and operational efficiency.
People
You may have the best product in the world but if you don’t have the right people to help you produce it and sell it, you are just spinning your wheels. But as the workforce ages and takes valuable knowledge and skills into retirement, the question for manufacturers is how do we replace them? As many as 3.5 million manufacturing jobs could open up over the next 10 years.
It’s not that this is a new problem. Many manufacturers are already desperately trying to fill currently open positions. Having their skilled workforce retire will only make the problem worse. There is no doubt that automation will help but people will still be needed to manage the product through the production process.
Current workers also faced additional problems. Poor communication still remains a significant problem for many manufacturers. It’s a sure way to make a mistake. Production teams also need to be able to handle the changes that are often requested by clients in the middle of a production process. And safety is a constant concern. Worker’s Compensation not only costs the company money but if an important worker is injured because workplace safety has been ignored, it can affect the entire manufacturing process.
Micromanaging can also discourage and undermine a production team. It is disruptive and prevents workers from doing their best work.
How do you solve these problems?
- There are not as many trade school opportunities as there were 20 or 30 years ago. And so manufacturers are creating their own training programs to teach new and younger workers all the skills that they need regardless of what role they play in the production process.
- Manufacturers also need to become creative about how they attract new workers. They need to go to where the workers are. You’ll find relatively few if you advertise in newspapers. Develop smart ways to connect with these potential workers through social media or networking events. New workers are not just looking for a career. They’re looking for a culture where they feel they will flourish. Promoting the culture of your workplace is very important.
- Keep your team up-to-date on all the important workplace safety regulations. Never become complacent about this. The chances of workplace accidents taking place at the manufacturing site are higher than almost any other location. So constantly train your employees and inspect your workplace to make sure that it’s safe. That includes keeping all your equipment up-to-date as well.
- If you want to solve micromanagement, the smart thing to do is assign project management roles. This is a great way to encourage your team and help them use their own creativity. Take the time to pick the right person for the right job. If you have an employee who is particularly good at one part of the manufacturing process, assign them the responsibility to lead on that part of the project.
Product Development
Your customers are going to expect you to update your product line from time to time. But developing a new product comes with its own set of challenges. How do you know what your customers want? More importantly, how do you get all the stakeholders within your own company to work on the same page?
For example, an important senior member of your company wants to respond to a customer’s request for a quicker launch date of a new product. Often the senior manager will assure the customer that this is not a problem without first consulting with his production team to know whether that is true. The result is a team overwhelmed by a new, much shorter production cycle. This creates the possibility of more mistakes and a truly unhappy workforce.
If you don’t understand the needs of your customers, any new product will fail. If your customer really needs “A,” but your company produces “B,” that is a surefire way to lose that customer.
Here are some potential solutions:
- Make sure you have the most important stakeholders in your company involved in the manufacturing process of a new product from day one. Buy-in from the senior level of a company may be the most significant factor in a product’s ultimate success. This will help the team better deal with issues like change orders or shortened schedules because better communication and buy-in from senior management means they are more aware of any problems this may create.
- To make sure you are aware of your customer’s needs, follow these important steps:
- Identify your customers’ most important needs. Throughout the development process, research, experimentation and testing are important, based on feedback in conversations with customers.
- Smart project management. Be organized and define the process. Pay attention to things like customer satisfaction, what your profit may be on the product and how long it will take you to launch the product. Make sure you and your team completely understand the nature of the product and that all your goals are well defined and known by every member of the team.
- Separate the product from outcomes. It’s important to think not only about the product but also about how you’re going to sell it. You need to message test, do launch surveys, conduct product validation and assess the market. These are key to the marketing and the sales of the new product. Don’t just focus on the merits of the product — make sure you use the above processes to get lots of feedback from your customers. This will give you clues about how you can best sell your product.
Technology
Pressure grows almost every single day for manufacturers to incorporate more and more technology into their production processes. There are many reasons for this — a shrinking skilled workforce, a constant pressure to reduce costs and the need to remain competitive against other companies that are using technology in their processes. The need for companies to remain agile and have the technology necessary to respond to ever-changing global markets is paramount.
Manufacturing companies need to incorporate technologies that increase quality, improve efficiency, energize production processes and most of all reduce costs. And all of these new technologies must be incorporated while keeping in mind other important budgetary needs, like maintaining current equipment and software and protecting against the increasing threat of ransomware and hacks.
Companies need to be up-to-date, paying constant attention to items like automation, robotics, the Industrial Internet of Things (IIoT), cloud computing and so much more. And manufacturers face the constant problem that by the time their IT departments have researched and installed what they believed to be new technology, something even faster and more relevant to market conditions has emerged.
Stay a step ahead with these potential solutions:
- As a first step to incorporating new technologies into your company, work with a business consulting firm that specializes in manufacturing. It’s their job to know how to define “the cutting-edge” and if your company should be there. They can provide the necessary training on the technologies that they do recommend which will help you get the best return on your investment.
- When used correctly, IIoT can help generate new services that will provide new revenue. The key is the data and the data-related services generated by IIoT. This data will not only help show manufacturing companies where they can create new services but will also help them in the aftermarket to provide more timely repairs or updates when needed.
- If your company has not moved to the cloud, it’s time to do so now. In the 2017 State of Manufacturing Technology Report, almost 90 percent of manufacturing companies say they are using cloud-based programs to improve their productivity. The report shows that these companies feel that they have received significant benefits from moving to the cloud — 70 percent say that using cloud computing has improved their ability to meet their customer’s demands and 45 percent say it is a key contributor for making introductions about new products to the market.
- Virtual reality (VR) and augmented reality (AR) are ideal for testing a variety of manufacturing scenarios before a product is ready to move into full production. AR can help manufacturers identify potential issues that could interfere with or stop production. These emerging new technologies have other uses as well, including worker training, tracking inventory and providing a deep dive into optimal operational procedures and standards. They can also be used to provide information on how to make important repairs in remote locations that are difficult for regular technicians to reach.
- As we mentioned above, if manufacturing companies are going to develop and attract the next generation of skilled workers, they need to go where those individuals are. That means learning to use social media to both generate new hires and, perhaps more importantly, positively promote the culture of your company to a new generation.
Cybersecurity
You have likely heard or read the stories about illegal hacks and the theft of customer data that have been conducted against companies over the past couple of years. And the reality is that these break-ins have probably been underestimated, as many companies are afraid to announce that they have been hacked because of the effect it will have on their customers.
Hackers are not only interested in stealing data, but they also want to hold it hostage. Verizon reported in 2017 than the previous year ransomware attacks have increased by more than 50 percent. For example, if a hacker gains access to the software that controls automation or your robots, it can shut everything down until all of its demands for ransom are met. And as manufacturing companies increasingly rely on new technologies such as the Internet of Things, they can expect hackers to launch increasingly sophisticated attacks on their networks.
How do you keep your systems secure?
- Regularly update all computer security software. It is sad but true that too many companies only update the security features of their computer software now and then or when it comes to mind. This is like leaving an open door in your house for a burglar. Make a routine to check for updates to your computer security software every week or two. Don’t leave your front door unlocked.
- Educate your employees about the warning signs that they are being hacked. More than one company has been hacked because of an employee who clicked either on a phishing email or an email that contained a funny video. Your employees are your first line of defense. Make sure they are prepared. Teach them to look for the signs of a phishing email — unusual URLs, strange attachments, poor spelling or grammar, requests to update information or a note telling them that they won a contest.
Changing Regulations
These are interesting times when it comes to changing government regulations and tariffs. Dealing with the ever-changing world of government regulations always feels a bit like riding a wave. It’s powerful, but it’s uncontrollable. And you never know exactly which direction it will head.
The other issue, of course, is who knows how long any regulation will last? What one administration does another administration can undo. Every new administration brings with it a new set of priorities that impact regulations set for the manufacturing industry.
Here are some possible solutions for reacting to these changes successfully:
- One of the keys to any successful business is knowing how to mitigate risk and avoid uncertainty. Costs ebb and flow with changing regulations and tariffs. Manufacturers need to keep up-to-date and stay informed. This will help them stay nimble in the face of unforeseen changes and be in a better position to react to the changes they already know about.
- Create a team whose job it is to focus on changing regulations and who will then communicate how these regulations affect your company to important stakeholders and suggest the best ways of dealing with them.
- As we noted above, changes in regulations and tariffs come and go. One of the best answers to survive in this environment is to remain focused on your core competencies. Keep focused on what you do well and what you’ve always done well. This will provide you with a competitive advantage regardless of government regulations. Don’t wait for regulations to come along and provide you with an advantage. That is a fools’ errand.
Balancing Maintenance
Do not become so obsessed with the more creative aspects of the manufacturing process that you fail to notice that your equipment is stressed or in need of repair. If an important piece of your manufacturing equipment breaks down or fails at a key moment in the production process, it won’t matter how many good ideas went into your product’s creation.
How do you make sure your equipment stays functional?
- Regular preventative maintenance is essential in a manufacturing facility. It’s not just a matter of keeping the lights on and it’s much more than just another expense line for the C-suite to worry about. It’s important for worker safety. It’s key to making sure that your product makes it to market on time. It’s important to make sure that any new product meets customer expectations.
- Regular preventative maintenance helps reduce costs and save time. Don’t make it a back-burner issue.
- Regular maintenance of existing equipment will help you better understand how to integrate new technologies into your overall manufacturing processes.
Global Electronic Services Can Handle All Your Equipment Maintenance Needs
Global Electronic Services offers continuous, reliable, professional, preventative maintenance and repair services for manufacturing facilities and all of their equipment.
Working with Global Electronic Services means you can continue your operations and help limit losses due to damage. You can also select the most important repairs to be done off-line or off-peak hours whenever it works best for your company. We also offer monthly, quarterly and yearly programs so you can find one that works best for your manufacturing business.
You can subscribe to our blog, request a quote or directly order repairs. Our highly professional and trained technicians will help you solve any problem and get your manufacturing processes functioning smoothly again.