Why is AI the Future of Reliability-Centered Maintenance?
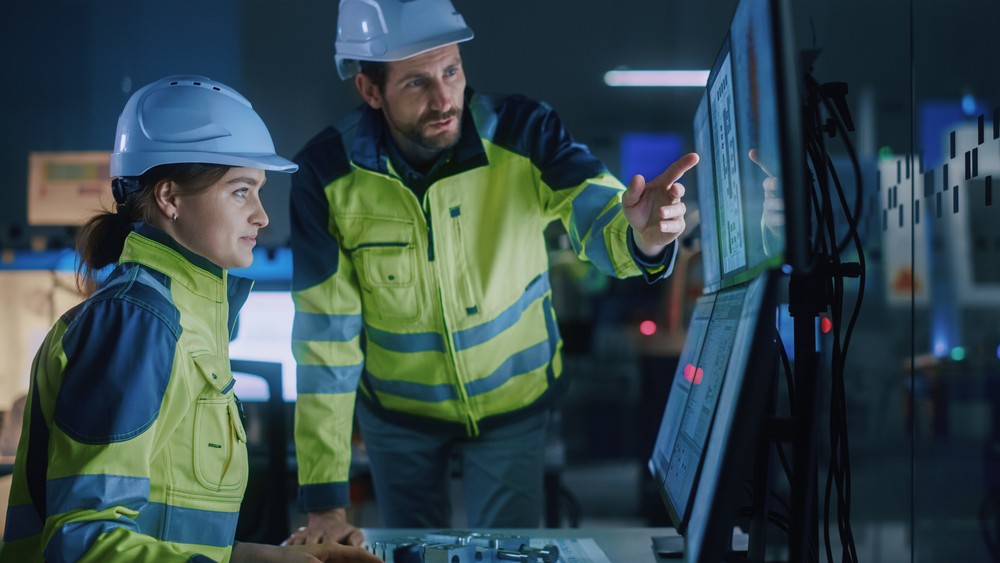
Artificial intelligence (AI) has long been a key driver of amazing innovations in manufacturing. It’s already on the forefront of quality assurance, workflow management, supply chain optimization, and more. Now, AI is taking on maintenance.
Reliability-centered maintenance (RCM) approaches benefit from AI and its ability to proactively predict events. Instead of waiting to administer maintenance at routine intervals, or repair a machine that breaks down, AI empowers RCM when it is needed, to preempt problems big and small.
What is RCM?
RCM ensures that all systems run at optimal efficiency and accuracy. It borrows from preventive and predictive maintenance modalities to guarantee each piece of equipment individualized attention aimed at keeping it functional. When implemented properly, RCM programs save money, improve safety, and enhance machine performance and reliability.
Practices for RCM vary, but most involve identifying system functions, isolating failures, and correcting them. It is essential to understand the potential consequences of these failures and why they occur in the first place. Identifying failures allows manufacturers to implement preventive measures and tweak maintenance strategies and schedules.
The major benefits of RCM
A good RCM program provides companies with the information they need to prevent machinery failures and shutdowns. Manufacturers benefit from increased reliability in numerous ways:
- Cost efficiency. Identifying failures and changes reduces future repair costs.
- Improved performance. Well-maintained equipment performs to a higher standard.
- Enhanced safety. Maintained equipment is safer for employees.
- Equipment longevity. Equipment with superior maintenance standards runs longer.
- Production predictability. Data allows manufacturers to predict production output.
Because RCM puts reliability at the forefront of maintenance, manufacturers retool their processes to ensure equipment receives dynamic attention. Instead of following a static maintenance schedule, equipment benefits from service and upkeep when and how it needs it.
What’s the role of AI in RCM?
While beneficial to manufacturers, an RCM philosophy is difficult to undertake successfully. Not only does it require systems to measure machine performance, RCM also demands individualized attention for each piece of equipment. This is where AI comes in.
AI programs accurately identify the condition of factory equipment, allowing manufacturers to determine its status and run those conditions against criteria for maintenance. AI can also interface with digital twins — and other records of equipment maintenance and service — to qualify conditions and contextualize them within an RCM approach.
And AI does not stop at the machine level. Some types of AI can even predict changes in the market and adjust supply chains accordingly, which helps companies optimize spending. For example, if original equipment manufacturer (OEM) inventory levels are low, AI might have the foresight to order parts and create work requests before inventory is depleted and maintenance is overdue.
AI, RCM and the growing IIoT
AI, RCM, and the Industrial Internet of Things (IIoT) all work in unison to improve the state of manufacturing. When manufacturers have a robust IIoT with the right sensors and beacons for equipment, there is plenty of data for an AI to process. Using this data, AI can drive better foresight in maintenance and service planning, which supports a robust RCM approach and all the benefits that come with it.