What’s Causing Production Bottlenecks?
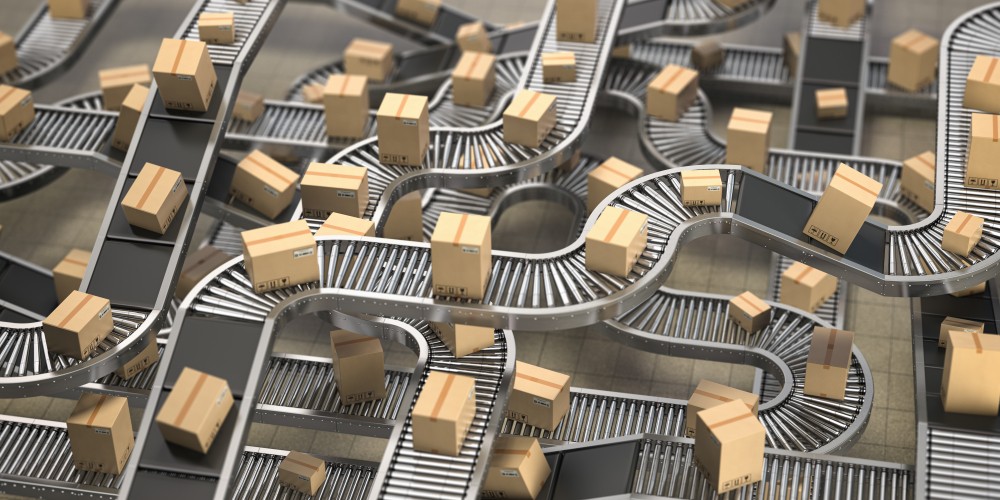
If they’re not swiftly identified and resolved, production bottlenecks cause big problems for manufacturers. Simple bottlenecks can lower your throughput numbers, put excess strain on equipment, and waste both time and money. Whatever the setback, most bottlenecks are avoidable if manufacturers are aware of their potential causes. So, what are the most common catalysts for production bottlenecks? And how do they contribute to downstream problems?
Equipment inefficiencies
Every piece of equipment on a production line must work at maximum efficiency. Inefficient and outdated equipment is often slower and can experience frequent breakdowns. These problems cause hiccups in the production cycle which can easily create bottlenecks.
The best way to ensure the quality and efficiency of factory equipment is to keep to a strict maintenance schedule. It’s also a good idea to replace equipment that requires constant repair. While there’s significant upfront cost to new asset investment, replacing outdated equipment saves manufacturers the combined costs of frequent repairs, significant downtime, and the production losses associated with a bottleneck — as much as $12 trillion annually by some estimates.
Breakdowns and downtime
Inefficient equipment is annoying, but broken equipment is undoubtedly worse. Dealing with broken equipment invariably results in downtime. And downtime creates production bottlenecks that cannot be resolved until the equipment is repaired. Repairs frequently take more time than expected — which leads to even more downtime. Costly repairs can deliver a significant blow to a company’s budget, and downtime leaves employees with nothing to do, creating numerous points of waste, each with its own intrinsic costs. A regular, preventive maintenance program is your best solution for preventing broken equipment and significant downtime.
Several issues may contribute to broken equipment, but overextension is a major cause. This usually occurs when a manufacturer overextends equipment capabilities to produce more items in a shorter time frame.
Process inefficiencies
Inefficient production planning can also lead to bottlenecks. When developing a production plan, pay special attention to pacing. Bad pacing naturally leads to bottlenecks. For example, if Machine A produces 30 assemblies per hour, and the next phase of the cycle, Machine B, only produces 20 assemblies per hour, there’s a potential bottleneck of 10 assemblies per hour as production moves through its cycle. Adjust for timing and flow to create a value stream void of bottleneck risk.
Bad forecasting
Bottlenecks aren’t always caused by faulty machines. Sometimes, human error is to blame for production disruptions. Bad forecasting can easily cause bottlenecks to appear at important junctures of the production line. Overestimating demand, for instance, leads to stockpiles of finished goods that occupy too much storage space. This also leads to inflated costs, stocking issues, and other throughput problems that put unnecessary stress on manufacturers.
What can manufacturers do to fix these issues?
Regardless of the reason(s) for a production bottleneck, one question remains: How do you fix it? Every bottleneck is unique in that it requires its own specific solution. Manufacturers should approach bottlenecks from an analytical standpoint with a fish bone diagram and bottleneck diagnostic tools. Solving the root problem alleviates the bottleneck, so it doesn’t continue to interfere with efficiency on the production line.