What Is Mechanical Shock?
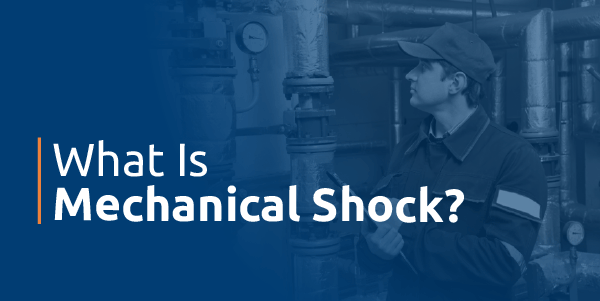
In the world of mechanics, precision is key. Before products and designs can go out into the world, engineers need to understand every possible facet of their work. How strong is it? How fast, flexible and durable is it? How well does it stand up against different types of adverse conditions? Once these products are released into the world, all of these things will become readily apparent, but it’s the designers’ and engineers’ job to arrive at solid conclusions before that time.
Quick Links
What Is Mechanical Shock?
What Are the Effects of Shock?
How Can You Measure Mechanical Shock?
Why Is It Important to Measure Mechanical Shock?
How to Control Mechanical Shock<
Learn More on Our Blog
Unfortunately, this can be difficult to do in warehouse and factory conditions. After all, these are purposefully safe and controlled environments. How can designers use them to predict how mechanical designs will behave under stressful circumstances? The answer is to create tests which mimic potential conditions the design might face, to evaluate how well the design performs against them.
One such test is one that we call mechanical shock testing. This test is critical to the safety of many different types of mechanical designs. Without tests like these, many designs would not be safe to release into the world. Today, we’re going to talk about what shock testing is, why manufacturers use it and how it works.
What Is Mechanical Shock?
Mechanical shock is best understood as a sudden and severe jolt to a mechanical system, and one that usually causes significant disruption across the entire system. In other words, if we interpret the word “shock” in the colloquial sense, and substitute the person being shocked for a mechanical system, the comparison would be accurate. A shock in this sense is a surprise that comes out of nowhere, giving the body and brain a jolt and usually disrupts whatever it was you were doing. Your heart probably races for a few minutes, you might physically jump, and you might even gasp. Likely, it will take a moment or two before your body returns to its resting state.
The same is true of a mechanical system. The key characteristics to remember what it comes to defining shock are suddenness and severity. A jolt to the system that is not sudden would not be considered a shock, but rather a slow build of pressure. As a result, the system will react differently. Think of the difference between being subjected to a jump scare versus a slow-building argument. Both are upsetting, but our reactions in each situation are different.
Likewise, a disruption that is not severe would also not be considered a shock. To once again use our metaphor of shock in a person, think of the difference between a paper cut and a gaping wound. One is more severe than the other, and as a result, both our personal reaction and the resulting damage to the body will be vastly different.
Through comparisons like these, we can gain a better understanding of what shock is — a jolt to the system that’s both sudden and severe, and often throws the entire mechanism into at least momentary chaos. It can come from any source — such as a collision of two objects at high speed, the discharging of a weapon, the dropping of an item from a tall height or a moving object slamming into a stationary one. All of these examples create exactly the type of impact that we would call shock.
Because manufacturing environments are usually extremely controlled, mechanical shock is unlikely to occur in its truest and most natural form. Accidental shock is unlikely, and if it does happen, it’s most likely the result of things not going according to plan. Shock can be planned for, however, in controlled testing environments that are designed to measure how well a mechanical design responds to shock. These tests then help engineers to tailor their designs in ways that will help the items in question absorb the shock more effectively.
What Are the Effects of Shock?
Because a mechanical shock is unexpected and intense, it should come as no surprise that it can be quite devastating to the system. Ideally, engineers will plan for potential shocks and have built a system that’s designed to resist these likely eventual impacts. Even despite these measures, however, shocks don’t always act the way we might imagine they will, and things may still be damaged.
If a shock is unplanned for, and if no measures have been put in place to guard against it, however, the effects will likely be far more devastating than a scenario where the engineers have prepared for them. Just a few of the potential effects of mechanical shock include:
- Blunt force fracture damage due to two or more items impacting one another, or one outside force impacting a standing item.
- Bending due to impact on a ductile item.
- Mechanical failure, which is a probable outcome of recurring low-level shocks.
- Eventual instability, which will likely be the result of recurring small amounts of damage that build over time to create larger amounts of damage.
- Shortened service life due to blunt trauma and mechanical instability.
- Decreased reliability, especially in cases of repeated shocks with the reliability decreasing further after each incident.
- Invalidated results from precise scientific instruments, if any were located within the impacted system.
- Detonations of any explosive elements that may have been located within the system when it was shocked.
- Weakened or separated connections within different pieces of the system.
Of course, it can be difficult to picture all of these separate consequences as hypothetical ideas. Let’s look at a concrete example instead. Imagine the mechanical system in question is a car. In this case, the shock is a car crash. It meets all the criteria of a shock — sudden and severe — and is, therefore, the perfect example.
Try to picture a vehicle after a severe crash. There will almost certainly be physical damage such as bending, denting and smashing. But there will also likely be mechanical failure, as the car fails to start again. Instruments such as the speedometer won’t work anymore. And even if the vehicle did start up again immediately after the crash, we would all understand that it would have a decreased service life and be extremely unreliable.
All of these are potential and even probable effects of mechanical shock. While a car makes an excellent example to study, the effects will likely remain the same no matter what the mechanical system in question is and what the shock has been.
It’s easy to see why it’s important to put measures in place to protect against shock. To do this, however, manufacturers need to understand how shock works, as well as how well their system guards against it. This is where testing and mechanical shock calculation both come into play.
How Can You Measure Mechanical Shock?
As engineers are designing a system, it’s critical for them to know whether or not that design could be impacted by shock. If so, how much shock will it take to cause damage? What levels of damage will ripple throughout the design? All of these are meaningful considerations, and all of these are part of the process known as shock testing.
During shock testing procedures, engineers and designers test their designs against shocks that might occur in the real world and gauge the resulting reactions. In early design phases, these tests might be purely hypothetical and generated in a computer program. As the design progresses, however, they must eventually complete these tests in real life to evaluate the way their full-size designs react against accidents and events that could actually occur in the real world.
This involves a variety of different tests, which differ depending on what the mechanical system in question is and which type of shock the designers are testing for. These tests can simulate many different types of real-world events, such as:
- Product-handling events: Imagine a fragile package that’s being transported, only to be dropped out of the air. The packaging material manufacturers will want to simulate this type of event to ensure their materials will survive it.
- Transportation-related events: Think back to our analogy of the car. Plenty of shock-inducing events can occur along roadways, and engineers use tests to simulate these events and gauge reactions to them.
To complete these tests, engineers and technicians use specially designed equipment that simulates the correct amount of force from the event that is being mimicked. The equipment then records the way the system reacts and translates this into usable data. This data records in black and white exactly how the shock affected the system.
Like any type of testing, just once isn’t enough. The technicians will repeat these tests multiple times to gather a large enough sample size to ensure that their data is accurate across the board and not the result of one abnormal test.
From here, the engineers will use these results to make necessary changes to the design that will ideally render it better able to withstand shock. They then repeat the tests, make more adjustments and continue the process until the design is sufficiently prepared to face the shocks that it may encounter as it performs out in the real world.
Why Is It Important to Measure Mechanical Shock?
Measuring mechanical shock is important because it lets us all have confidence that the items we use every day will continue to perform well even if there are slight road-bumps along the way. For example, every time we get in a vehicle, we recognize that there’s a possibility we might have an accident — from something as simple as running over a curb to something as severe as a head-on collision. And while there are some situations no car can come away from, we recognize that our cars are carefully designed to protect us and keep going, even if you get stuck in a pothole or hit someone else’s bumper. We understand that the designers have done their due diligence, and as a result, we can feel safer and more secure.
Imagine if shock tests didn’t exist and if products were simply shipped out into the world on the hope and assumption that they were safe. Instinctively, most of us will realize the grave insecurity of such a situation. This is why shock testing is important. It keeps us safe. It keeps our belongings safe. And it helps us feel a little more confident in the products we use and that surround us every day.
How to Control Mechanical Shock
Testing for shock and measuring its effects is one thing. It’s easy enough for engineers to look at the results of a test and see that they need to ramp up their shock-absorption measures. However, it’s quite another to do so and craft a finished product that’s capable of withstanding significant stress levels.
Just a few of the different measures that engineers might choose to take to improve a design’s reaction to shock include:
- Modifying the design to add toughness. This is perhaps the simplest solution and involves altering the design the least. Rather than changing the way the design is composed, engineers will upgrade the materials or add additional protective layers around it. Think of this as adding extra armor to help the item withstand stress more effectively.
- Using shock absorbers or cushions to lessen the impact. This solution involves more re-designing and thus is a little more complex. Rather than just adding extra armor, this solution seeks to add cushioning elements throughout the item, such as shock mounts and absorbers so that when the impact does hit, it’s well-distributed throughout the design. This allows the shocks to be absorbed in the safest ways possible.
- Reducing the shock at the source. This solution involves creating a design where the impact of the shock is cut off as much as possible at the source. In other words, the shock makes its initial impact but is not allowed to transfer this shock to the rest of the item.
- Planning for failures. Not every product is worth spending the time and money to protect against shocks. Certainly in something as critical as a vehicle, these precautions are necessary. But in many cheap products that will never determine life or death, the best solution is to accept the risk and move on. In most cases, these products will be so cheap that replacing them is more cost-effective than developing more sturdy designs in the first place.
Each of these solutions is a large umbrella category and within each one are hundreds of different design solutions unique to every type of product. Most solutions, however, will fall into at least one of these primary categories.
Learn More on Our Blog
Do you have any experience with the world of mechanical shock testing and calculations? If so, be sure to comment and tell us your thoughts. And for more fascinating information and updates about the manufacturing industry, be sure to subscribe to our blog here at Global Electronic Services, where we’re committed to keeping you on top of the latest news and developments across the industry. And once you’ve subscribed for future updates, don’t forget to scroll back and read our older posts as well.