What Is Material Requirements Planning and Why Does It Matter?
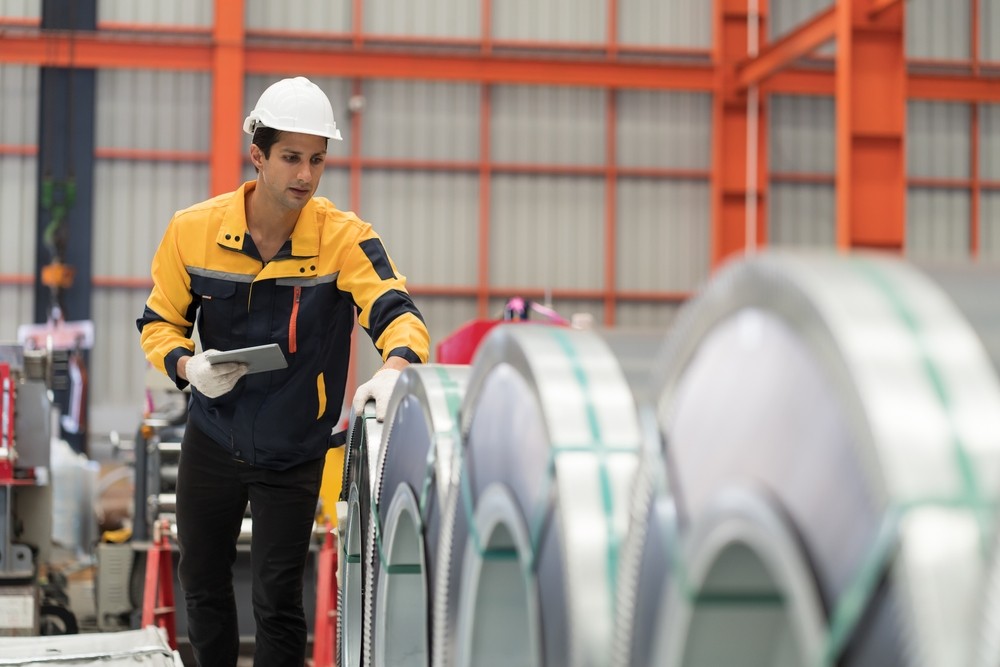
In simplified terms, manufacturing is the process of turning raw materials into finished goods. This process is controlled from end to end, beginning with the flow of raw materials entering the value stream. If you order too much, you’re left with a surplus. If you order too soon, you’ll tie up money in inventory. If you order the wrong item, production grinds to a halt.
In this process, many things can go wrong. It’s why every manufacturer must have a strong grasp of material requirements planning (MRP).
MRP defined
Manufacturing is all about achieving efficiency while maintaining customer satisfaction. Material requirements planning helps producers attain the perfect balance. This production and inventory management system enables manufacturers to plan and control ordering and production processes. It’s a framework for having the right materials in the right place at the right time to meet manufacturing demands.
Key components of MRP
MRP relies on a set of key components working together to drive accurate demand forecasts, inventory management, and timely production schedules. These interrelated considerations include:
- Bill of materials (BOM): A well-maintained and accurate BOM lays the groundwork for a reliable MRP system. It’s a comprehensive list of all raw materials, components, and subassemblies required to manufacture a finished product.
- Inventory management: An efficiently functioning inventory system ensures the right level of materials at all times to provide uninterrupted production and good customer service.
- Master production schedule (MPS): The MPS forms the backbone of supply chain planning, with data serving as a directive for production teams. It guides producers on what to produce and when.
How MRP works
How do today’s producers forecast demand and guarantee they have the optimal amount of raw materials and components on hand at all times? Here’s how manufacturers can manage their inventory and production:
- Forecasting demand: Producers must understand the market demands for products and the factors influencing demand. This means planning for seasonality, market volatility, and unexpected changes in customer behavior.
- Calculating net requirements: Net requirements refer to the amount of material needing to be ordered or produced for an upcoming production cycle. Calculating net requirements — along with planning around lead times — is crucial in ensuring an organization has sufficient raw materials to meet production needs.
- Generating purchase orders: After calculating net requirements, the MRP system generates purchase orders for raw materials and components and work orders for production activities.
- Executing work orders: Finally, the MRP system creates a production schedule to optimize the manufacturer’s production efficiency and reduce lead times.
Benefits of MRP
MRP gives manufacturers an advantage, allowing them to manage their production, inventory, and supply chain cohesively. It results in better inventory management, enhanced production efficiency, lower costs, and a solid reputation for delivering quality goods on time.
While today’s manufacturers can benefit from powerful and highly intuitive MRP software, those who understand MRP principles will be better able to pivot, adapt, and evolve faster than their competition.