What is Andon in Manufacturing?
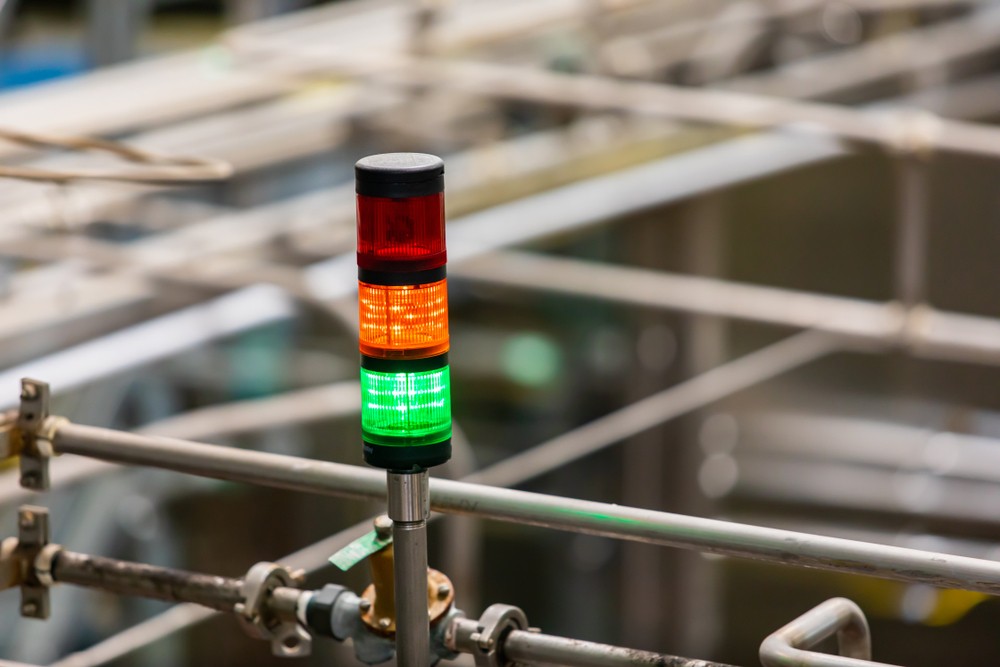
Often, the simplest innovations are the most powerful. The design of the fork hasn’t changed in centuries — spork notwithstanding — and there’s no need for Legos to evolve because they’re perfect as is. Such is the case for one of Lean manufacturing’s oldest and simplest innovations: Andon lights. There’s nothing quite so simple as a colored lighting arrangement to catch the attention of factory floor workers and immediately relay mission-critical information about the value stream.
An industrial game of red light, green light
In Lean manufacturing environments, an Andon lighting system is designed to quickly alert managers and operators of problems in real time so they can implement corrective measures instantly. Think of Andon lighting as akin to the “check engine” light in a car, only for a specific juncture in the value stream.
The beauty of Andon lighting systems is their use of a universal language: color. Much like a traditional stoplight, typical Andon lighting systems use red, green, and yellow to indicate the following conditions:
- Red: Production has stopped, requiring intervention from management.
- Yellow: There’s a problem on the production line needing investigation.
- Green: Conditions are normal, with operations continuing.
Andon lighting in the manufacturing space traces its roots back to the Jidoka methodology, implemented by Toyota. By empowering operators to spot problems and act to correct them — without seeking the approval of management first — this methodology boosts efficiency on the factory floor.
The powerful potential of an Andon system
While the Andon lighting system works with a very simple premise, it’s one with powerful potential. Lights are silent signifiers — driving awareness, which can improve actionability on the factory floor. Moreover, they’re indiscriminate, meaning anyone can see them and take informed action, even if they’re not the one directly addressing a yellow- or red-light issue.
Producers who integrate Andon successfully into their production processes create a more resilient value stream. By spotting and addressing issues as they occur, producers can:
- Prevent bottlenecks
- Reduce product defects
- Create more efficient, productive lines
Paramount to all of this, Andon lights help to bring presence and mindfulness to floor workers and production managers in real time.
From a Lean standpoint, there are several distinct benefits that come when manufacturers integrate Andon lighting into their production processes. Andon incentivizes workers to react to problems quickly and effectively, thereby improving product quality, enhancing worker safety, and reducing down time all at once. It’s a simple way to relay important information, streamlining communication to conserve time and labor.
Modern Andon: an old concept with new tech
Today’s digital Andon systems are a modern take on an old concept, involving complex boards that provide an at-a-glance view of production status while also enabling easy identification of problems. Andon is still driven by a color lighting system, but that system is now connected to everything from a factory manufacturing execution system (MES) to a digital twin of the value stream.
Digital Andon represents a new level of readiness potential. By making the small investment in the latest Andon technology, producers can create a Leaner value stream that yields a safer, more efficient factory and consistent, quality products that customers can depend on.