What is a Criticality Analysis?
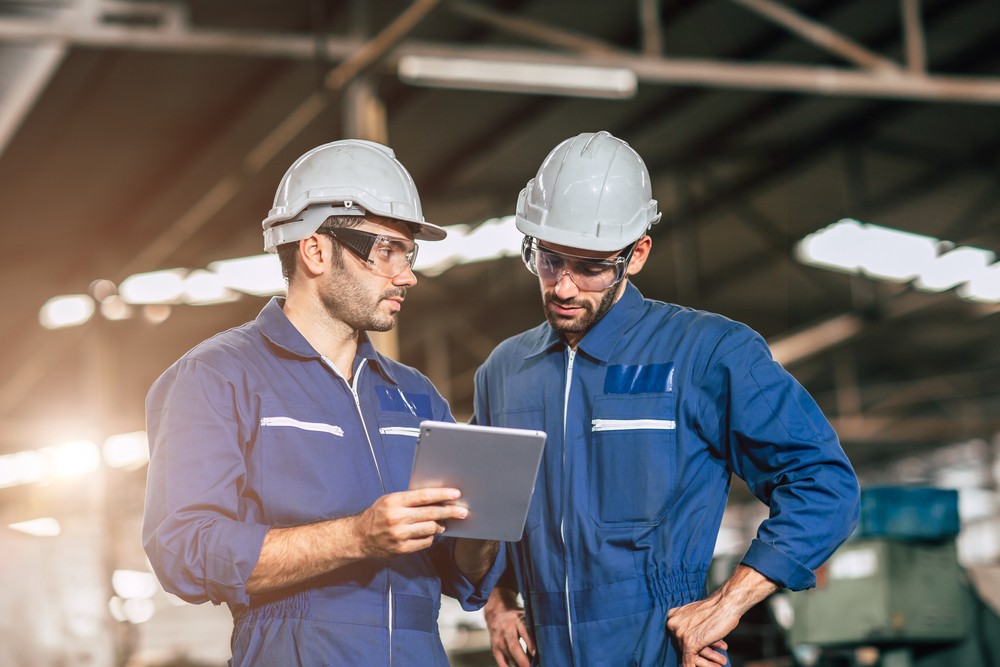
What you don’t know can hurt you. A small defect in a piece of machinery can become a safety hazard in moments — in the same way an equipment failure can bring your entire value stream to a halt.
Whether the harm manifests in personal injury, environmental impact, reputational damage, or loss of revenue, it’s inevitably a problem. The question is, could it have been avoided? If you take the time to perform a criticality analysis, the answer might be yes.
Understanding a criticality analysis
In the manufacturing sector, a criticality analysis is an assessment of risk weighed against the health of an asset — in particular, machinery and equipment. Maintenance professionals assign criticality ratings to assets, encompassing the many different ways each asset could fail and the effects it could have on individual processes and systems, as well as the entire operation.
Criticality analyses play a crucial role in a total productive maintenance (TPM) plan — a condition-based program to monitor high-value, high-priority equipment. By weighing risk with the features that make each machine critical, a criticality analysis gives producers an in-depth look at how an asset’s potential risk could impact operations across the factory floor.
Calculating risk and risk factors
What’s involved in performing a criticality analysis? Start by making a list of key assets and calculating the cost of repairs and downtime. For example, your factory could rely on thousands of motors in constant motion to produce a high-quality product. While the health of the motors is important, even more critical is the boiler that powers them. So compile a list of key assets and rank their criticality with this formula:
Equipment Criticality = Failure frequency (per year) x Cost consequence (repairs and downtime) = Risk (in dollars per year)
The criticality model involves multiple areas of an organization. As such, each analysis should be a company-wide effort, covering all departments — including engineering, maintenance, operations, procurement, safety, and others. By involving all teams, you’ll get a complete picture of an asset’s risk and optimal ways to assign it.
Applying criticality to improve operational excellence
A thorough criticality analysis helps producers manage assets and processes across the factory floor. Maintenance managers can apply criticality to focus attention on the assets that matter most so less time is spent on tasks that don’t mitigate costly risks.
While criticality analyses often highlight the need for preventive maintenance, they can also reveal the need to overhaul or modify equipment and processes to reduce risk. Either way, time and resources are better spent in the areas where they’re needed most, providing a host of benefits from reducing expenditures and downtime to improving worker safety.