What Challenges Does Additive Manufacturing Face as it Comes to Market?
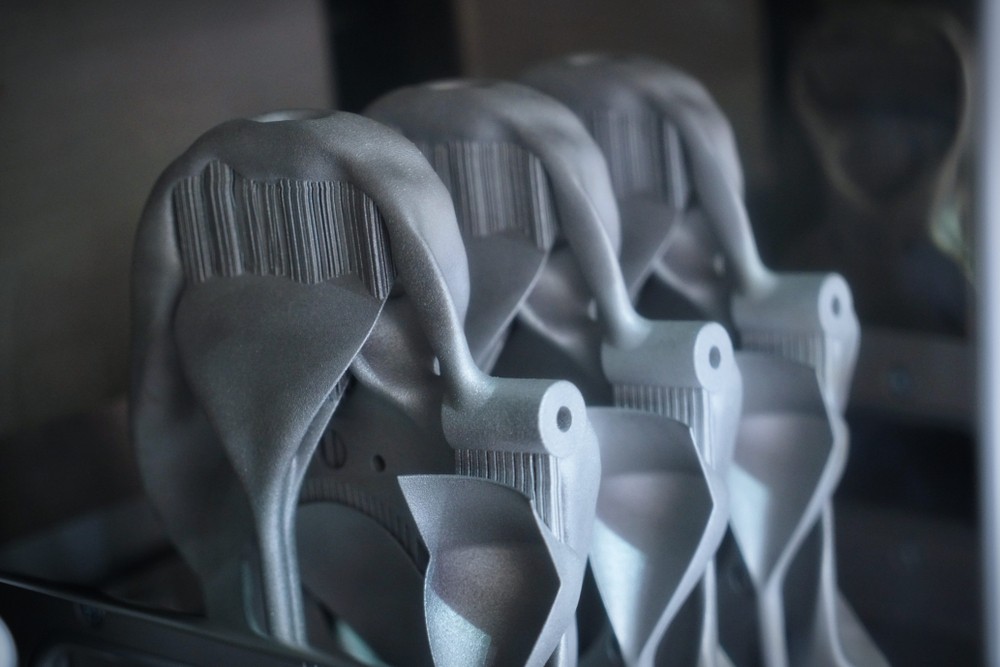
Few manufacturing trends have a more futuristic feel than additive manufacturing. Programming a machine to build parts to-specification, on-demand, all but taking the human element out of the equation, is something many manufacturers can’t wait to get their hands on. The benefits of additive manufacturing are simply too good to go ignored. Greater still, they’re broadly applicable across numerous sectors of manufacturing.
Why additive manufacturing for the future?
COVID-19 has shed light on the need for factory technologies that are resistant to disruption. Naturally, the conversation has come back to automation. Machines don’t need to social distance and they’re not at-risk for inheriting communicable illnesses. For additive manufacturing specifically, the benefits extrapolate far beyond.
Like all forms of automation, additive manufacturing has the potential to be cost efficient. It offers the prospect of both top- and bottom-line growth, in the form of costs saved (labor) and revenue generated (production). The automation factor also lends itself to leaner manufacturing — similar to how set-it-and-forget-it technology like CNC has already transformed machining. And, of course, there’s an element of efficiency, a la the repeatable standard of additive manufacturing.
All these benefits (and more) give producers across the spectrum of industry incentive to explore the prospect of additive manufacturing. But as they do, they’re running into several barriers that have stalled and continue to lag this technology’s emergence.
Challenges confronting additive manufacturing
For all its benefits, additive manufacturing has several staunch barriers that make it a difficult prospect — even during COVID-19, when the technology is seeing peak interest.
- Cost is perhaps the largest barrier for many factories right now. Not only the cost of the equipment, but the cost of maintenance and upkeep — not to mention the cost of feedstocks, which is currently astronomical. Metallic feedstocks are costly and difficult to source, making procurement an expensive endeavor.
- Scalability poses a serious problem for producers in many industries. While additive manufacturing may very well work for small or niche parts, the sheer size or volume of some components may detract from the benefits of additive manufacturing.
- Quality control is still an issue for many additive manufacturing setups. The process itself is still a highly volatile one, which leaves larger-than-desired margins of error for production. And although repeatability is a core benefit of the additive manufacturing process, it’s negated if there are random defects in the construction process. Producers need to solve issues of dimensional integrity, surface roughness, and unwanted tessellation.
Other problems can include machinability of some types of products or materials, as well as the expertise needed to make additive manufacturing work in facilities. It’s one thing to invest in the equipment and refine the process — it’s another to have staff available to program, troubleshoot, and adapt the equipment, as needed.
Additive manufacturing persists
Despite the current roadblocks, additive manufacturing remains an intriguing prospect for the future for a very simple reason: the concept is valuable. The benefits of this process are too many to pass up and the problems it faces aren’t so steep as to be overcome with innovation. It’s why additive manufacturing has gained so much steam during COVID-19 and will continue to after the pandemic passes.