What Can Barcodes Do for Machine Maintenance?
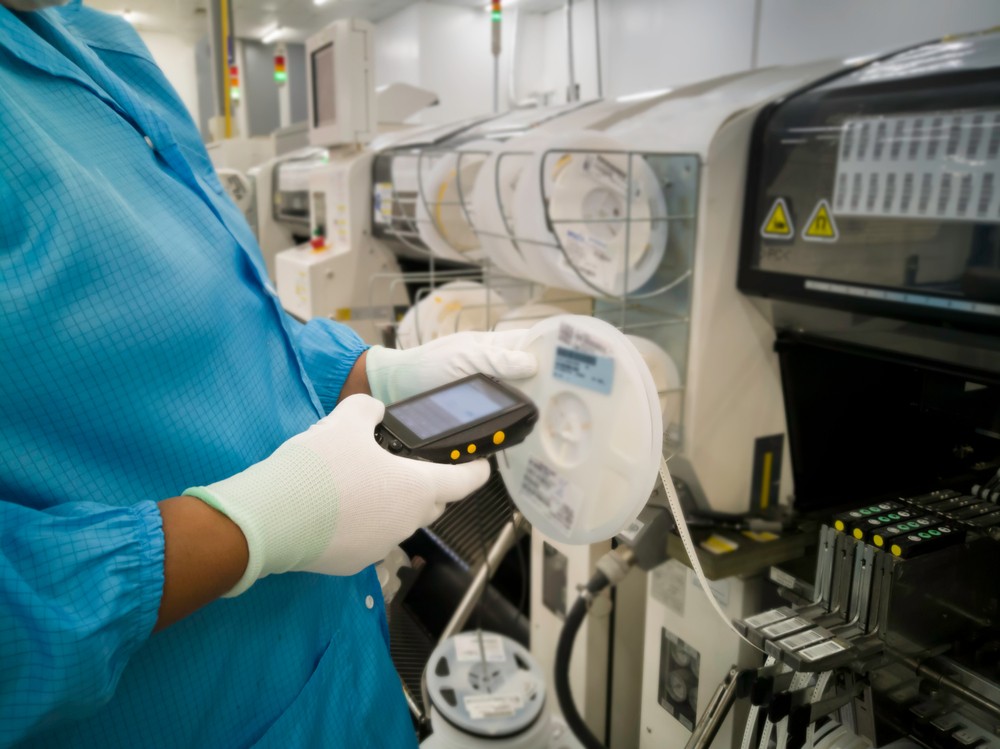
We tend to think of barcodes in their more traditional sense — as physical representations of transactions. You receive a part into inventory by scanning its barcode, then scan a similar barcode to remove it. Everything else happens behind the scenes, making barcodes a great tool for inventory management. But that’s not all they’re good for; barcodes play an important part in proactive factory maintenance programs, delivering vital, accessible information to technicians who need a snapshot of service data on-demand.
Scan for information
The simplest use of barcodes for machine maintenance is in their classical sense: cataloging information. In practice, this is as simple as a maintenance technician scanning a machine barcode to catalog the date, time, and user identification in a digital catalog. The service record is automatically added to a central database, recalled via enterprise asset management (EAM) software.
Another example of this is in data capture. For example, a technician might scan the machine barcode to initiate a maintenance log. The barcode prompts a service log, filled out on a tablet or smartphone. When finished, the service log is submitted to the database and easily recalled the next time someone scans the barcode. Machines may even have multiple codes — scan to maintain vs. scan to view log, for example.
Barcodes and the power of the IIoT
Barcodes aren’t limited to recording and relaying static data. They’re also valuable in displaying dynamic data, thanks to the Industrial Internet of Things (IIoT). Today’s barcodes are programmed to deliver pertinent information to maintenance technicians on-demand.
The execution of dynamic data via barcode can be complex, but highly valuable. The barcode or QR code is connected to the digital twin for that machine. When prompted, it opens the factory’s monitoring software to a preset dashboard displaying the records and real-time information for that machine.
- How many RPMs (revolutions per minute) is the motor currently spinning at vs. ideal tolerances?
- Is there maintenance due for this equipment?
- Are there any known issues from the last maintenance log?
A static barcode can offer dynamic insight into equipment when paired with a robust IIoT backbone.
Barcodes as a repository for truth
Given the right infrastructure, machine barcodes can become an instant resource for truth. For example:
- When was the last maintenance service?
- What did the last technician note about this machine?
- What components are currently in inventory that are necessary for maintenance?
With enough data sources linked into the barcode profile, maintenance technicians can answer virtually any question they may have for a particular machine, at the point of question.
Imagine walking past a machine and noticing a strange vibration or noise. You take out your smartphone and scan the barcode. It tells you that the last service technician noted a slight vibration caused by a soft foot. You also see that there’s a note to recheck this problem at a later date, and that the parts to repair it are already on order. You log a new note about the worsening problem, expedite the service order, and escalate the repair work order.
This is a simple example of how powerful a barcode can be — especially when backed by a robust data management system and multiple information inputs. It’s a great way to make maintenance more accessible, especially in a proactive capacity.