What a Functional Load Path Reveals About Your Equipment Health
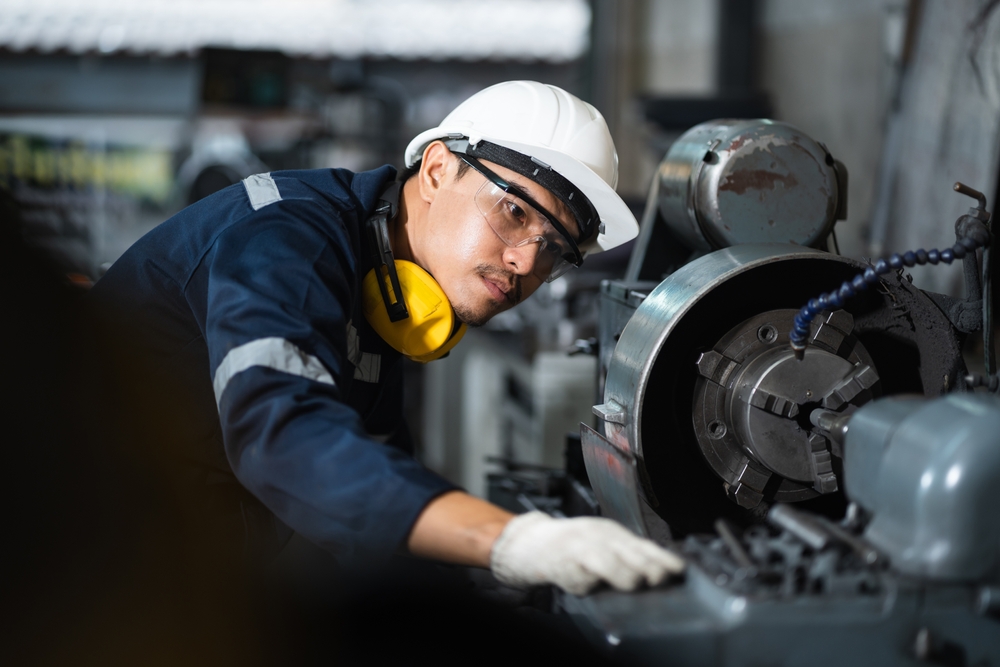
Every piece of rotating equipment has a functional load path โ the route that forces travel through bearings, shafts, couplings, and foundations during operation. This path reveals how well components work together and where problems develop long before they cause failures. Most maintenance teams focus on individual components, but the load path shows how the entire system behaves under real operating conditions. Learning to read these patterns can tip the balance of equipment servicing from reactive repairs to predictive maintenance.
Reading the load path story
A functional load path maps how forces flow through your equipment during normal operation. In a properly functioning system, loads distribute evenly across bearings, transfer smoothly through couplings, and dissipate predictably into foundations. The equipment operates within design parameters with consistent vibration signatures and uniform wear patterns.
Real-world conditions rarely match design assumptions, though. Thermal expansion, foundation settling, and normal wear create load path deviations that show up as changed vibration patterns, uneven temperatures, and accelerated component wear. These deviations tell you exactly where your equipment strays from optimal operation.
Identifying load path changes requires baseline measurements. Vibration analyzers, thermal imaging, and alignment tools can capture how forces currently flow through your system during operation. Comparing these measurements over time can reveal trends that predict component failures weeks or even months in advance.
Warning signs hidden in load paths
Load path analysis reveals equipment problems through specific, measurable indicators that traditional maintenance approaches often miss:
- Uneven bearing wear: When load paths shift, some bearings carry more weight than others. Temperature differences between bearing housings, unusual vibration patterns, and premature bearing failures all indicate load path problems.
- Coupling stress concentrations: Misaligned couplings create stress points that show up as unusual wear patterns, elevated temperatures, and changed vibration signatures. These stress concentrations accelerate fatigue failures and create secondary problems throughout the drivetrain.
- Foundation movement: Subtle foundation changes alter load paths in ways that affect the entire system. Thermal growth, settling, or structural changes create new stress patterns that show up as changed vibration characteristics and accelerated wear rates.
- Gradual degradation signals: Load path changes usually develop slowly, making them easy to miss without trending data. A gradual increase in vibration amplitude, slowly rising bearing temperatures, or changing alignment measurements all indicate evolving load path problems.
Using load path analysis for maintenance decisions
Load path analysis has the power to turn vague, generalized equipment concerns into specific, measurable problems. For example, instead of wondering why a pump “doesnโt sound right,” you get precise data showing a 15% increase in radial vibration at the outboard bearing. This quantifiable insight points directly to a coupling misalignment that requires an alignment correction rather than a costly bearing replacement.
The data drives targeted solutions.
When thermal imaging reveals a 20-degree temperature difference between bearing housings, you know exactly where to focus your attention. When vibration analysis shows increasing 1X running speed amplitudes, you can address the root cause before it progresses to bearing failure. Each measurement provides actionable intelligence that eliminates guesswork and prevents over-maintenance.
Load paths unlock predictive maintenance potential
Functional load path analysis takes the guesswork out of foundational equipment maintenance and opens the door to more data-driven decision making. Systems that track load path changes catch problems early, reduce stress and failures, and optimize maintenance based on actual equipment condition.
The investment in measurement tools and analysis techniques pays off through improved reliability and reduced maintenance costs. Itโs a cost many manufacturers are glad to bear โ especially considering the alternative.