The Role of a Reliability Engineer
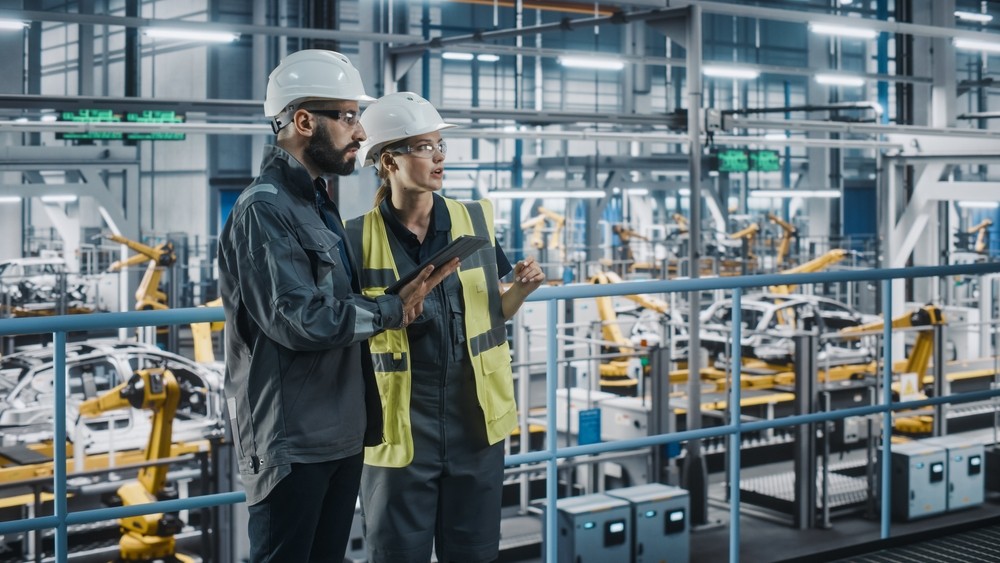
Nothing hurts a manufacturer like unexpected downtime. Production is the lifeblood of the factory, and unexpected downtime is a direct drain on throughput and profits. Proactive maintenance is required to keep equipment up and running efficiently. And while maintenance teams can pivot to preempt downtime, it takes a reliability engineer to establish a higher standard of maintenance.
Reliability engineers aren’t just another problem-solving force within the factory environment. They’re a critical component for keeping factories running efficiently under any circumstances.
What is a reliability engineer?
Traditionally, the duties of a reliability engineer break down into three disciplines: loss elimination, risk management, and life cycle asset management. These duties apply specifically to equipment used in factories, and the primary goal of a reliability engineer is implementing solutions to prevent unplanned downtime.
Manufacturers tend to lean on reliability engineers to mitigate production problems. Recurring bottlenecks, aging equipment, and line restructuring need the oversight of a reliability engineer to ensure optimal efficiency.
Benefits beyond problem-solving
It’s easy to think about reliability engineers in the context of the problems they solve. For instance, they can identify and resolve bottlenecks caused by inefficient equipment function, but the benefits of hiring a reliability engineer go far beyond a singular cause-and-effect use case.
Reliability engineers are typically at the center of factory initiatives designed to drive change. Their input is invaluable on projects ranging from lean-focused optimizations to new equipment integrations, training, upskilling, and beyond. Everything in the factory comes back to reliability. Reliability engineers ensure decision-making will benefit operational processes without negatively affecting their standard of reliability.
Used appropriately within the factory environment, reliability engineers do a lot more than keep equipment up and running. They also facilitate cost savings, enhanced efficiency, higher asset ROI, and improved safety.
An integral part of the team
Reliability engineers don’t operate in a vacuum. They’re frequently part of collaborative groups formed to solve specific problems or assess the potential impact of significant changes.
For example, a reliability engineer might collaborate with your chief maintenance manager to work through a failure modes and effects analysis, or they might partner with your asset manager to assess the total cost of ownership or life cycle cost of factory equipment. They might even work with digital transformation specialists to implement Industry 4.0 innovations with precision.
Reliability is intrinsically tied to core factory functions. From equipment maintenance to operational structure and process development, reliability should be a primary focus, which makes a reliability engineer essential.
Increasingly essential to factory operations
Reliability has always been a core focus of manufacturing. Now, as manufacturing anticipates a turbulent future, it’s more crucial than ever to hire and retain reliability engineers.