The Pros and Cons of Factory Automated Guided Vehicles
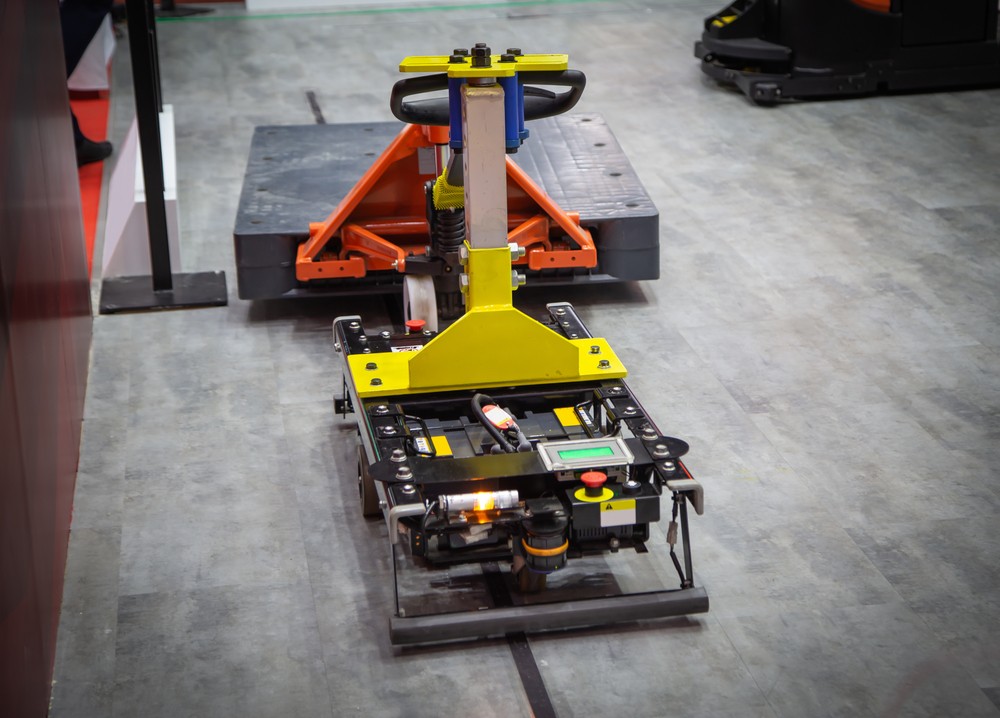
As industry is increasingly automated and digitized, manufacturers are welcoming new and robust technologies to the factory floor. Automated guided vehicles (AGVs) have risen to prominence in recent years. These autonomous robots are useful for ferrying supplies to and from production areas, and they’ve revolutionized warehousing for many companies. Effective AGV use requires an understanding of their role in the modern factory and some of the pros and cons that accompany their deployment.
What are AGVs?
AGVs are computer-controlled load carriers that complete factory tasks without a driver or onboard operator. Instead of relying on a driver, these vehicles operate on sensor-based guidance systems that use magnetic tape lasers and/or optical sensors to define their routes. AGVs move with controlled speed and feature automatic obstacle detection bumpers, which allow them to move safely along their specified path.
Most manufacturers use these vehicles to transport raw materials and finished goods, deliver pallets, and tow trailers. Examples of AGVs include automated carts, unit load AGVs, tugger AGVs, and automated forklift AGVs.
AGV pros
More manufacturers are investing in AGVs because of their many advantages, including improved safety and increased productivity. AGVs provide more efficiency and room for growth. The main advantages of AGVs include:
- Reduced labor costs. While AGVs may have high initial costs, they reduce labor expenses. After purchasing the equipment, a company need only pay for routine maintenance, which is much less expensive than hiring manual labor and certified forklift operators.
- Increased productivity. Even one AGV can improve a company’s productivity. AGVs don’t require downtime and could work 24 hours a day, seven days a week if necessary. In round-the-clock factories and warehouses, this automation drives line productivity.
- Improved scalability. Since they don’t require installation or much space, it’s easy to add more AGVs as a business grows. Manufacturers can implement additional AGVs without physical labor, so long as they have the tracks and routes established to accommodate them.
AGV cons
As with any new technology, there are certain drawbacks to AGVs manufacturers should consider before making an investment. Some common examples of AGV disadvantages include:
- Upfront investment. As with most advanced technology, the initial costs are high for AGVs. Manufacturers will see the savings from their investment over time, but it could take years to recoup the cost of an AGV investment at scale.
- Maintenance expenses. Routine maintenance is essential for keeping AGVs running. Maintenance costs money and requires downtime, which can have ramifications for value streams reliant on AGV operation.
- Connectivity demands. Since AGVs require connectivity to regulate their functions, it can take a long time to fix or replace them should something go wrong. Software and connectivity issues can be more difficult to repair than mechanical problems.
Are AGVs a good investment for you?
As the factory environment becomes more connected and advanced, manufacturers must identify technologies to enable higher efficiency, lower costs, improved safety, and increased output from their value streams. For many, AGVs are a solid investment. Consider all the pros and cons before deciding if they’re right for your factory environment.