The Core Principles of Effective Maintenance
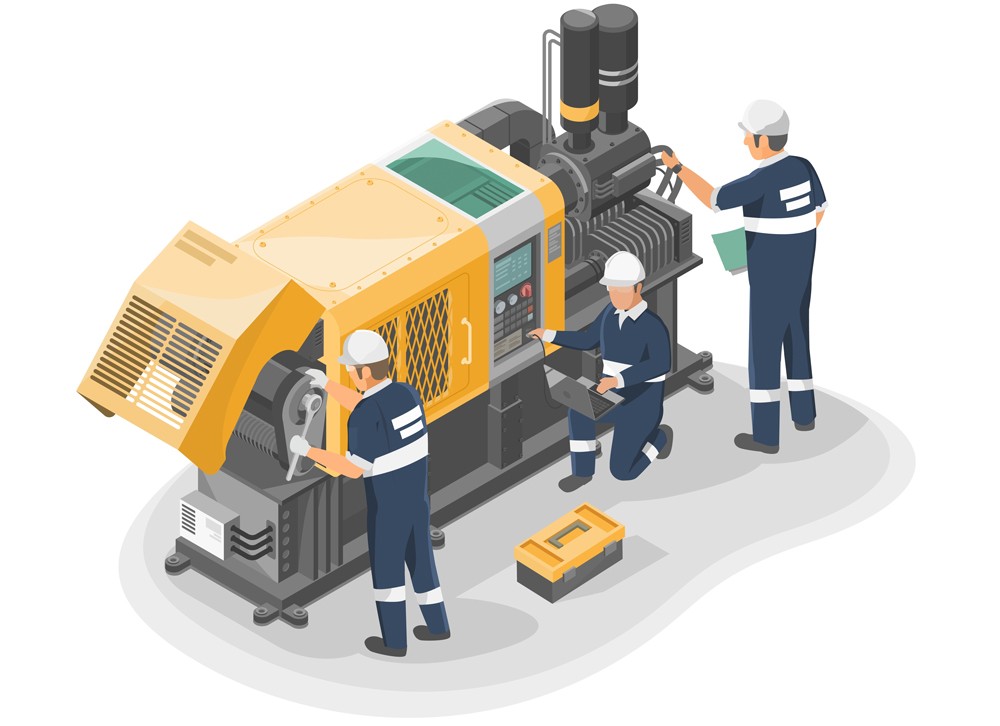
Behind every well-established process is a collection of concepts: a philosophy of why underlying the how. There’s no better illustration of this than manufacturing maintenance.
Before anyone flips a switch, turns a wrench, replaces a part, or logs service on a machine, there’s a level of understanding paramount to ensuring quality results. Manufacturing technicians need to know why they’re doing what they’re doing and how it contributes to a level of excellence beyond just a functional piece of machinery.
A machine only works as well as it’s serviced
A good maintenance program involves much more than fixing a machine when it’s broken. It entails promoting reliability by encouraging a preventative approach to service. The best maintenance plans focus resources on preventing downtime rather than reacting to it.
While some level of reactivity will always exist due to unaccountable variables, this shouldn’t stop maintenance teams from striving to be as proactive as possible. When failure happens, pinpoint the cause and work toward preventing it in the future.
Above all, as you make or refresh your maintenance plan, remember it won’t work if you don’t follow it. To ensure a maintenance approach produces efficacious results, it’s important to plan, do, study, and act (PDSA) to shape a response effective in creating reliability.
The core principles of effective maintenance
Your approach is everything. A well-considered maintenance approach stems from a clear understanding of the importance of maintenance and the results it creates. Thankfully, no matter what type of maintenance you or your team performs, the core principles remain the same:
- Be proactive rather than reactive. Reactive maintenance is an inefficient use of your assets. By creating a preventative or even a predictive maintenance plan, you can act on actual conditions rather than simply following a schedule. When you predict problems in advance, you can plan appropriately without sacrificing production.
- Be purposeful in approaching maintenance. In general, the purpose of maintenance is to promote the required capacity of a tool or machine used for production, at the lowest possible cost. All maintenance activities should revolve around this goal.
- Always look to solve the root cause. By focusing on the root cause of maintenance issues, maintenance teams can solve problems rather than treat symptoms. It also helps prevent the same problems from recurring.
- Have the proper training, equipment, and approach. Education and training are foundational elements in effective, proactive maintenance. Not only are the right equipment and training important for preserving the health of machines, but they are also critical for creating a culture of safety across the factory floor.
- Strive for continuous improvement. A culture of continuous improvement keeps production lines running and generates the maximum ROI from equipment. Seek feedback from operators and maintenance people, and use it to adjust your plan when necessary.
Embrace a better approach to maintenance
Following the core maintenance principles detailed above will result in a better approach to service. By creating a proactive maintenance plan centered on reliability — and implementing it across the factory floor — manufacturers can evolve to meet the challenges of today and tomorrow. No matter how maintenance needs change, these overarching philosophies will endure.