The Checklist: A Maintenance Tech’s Best Friend
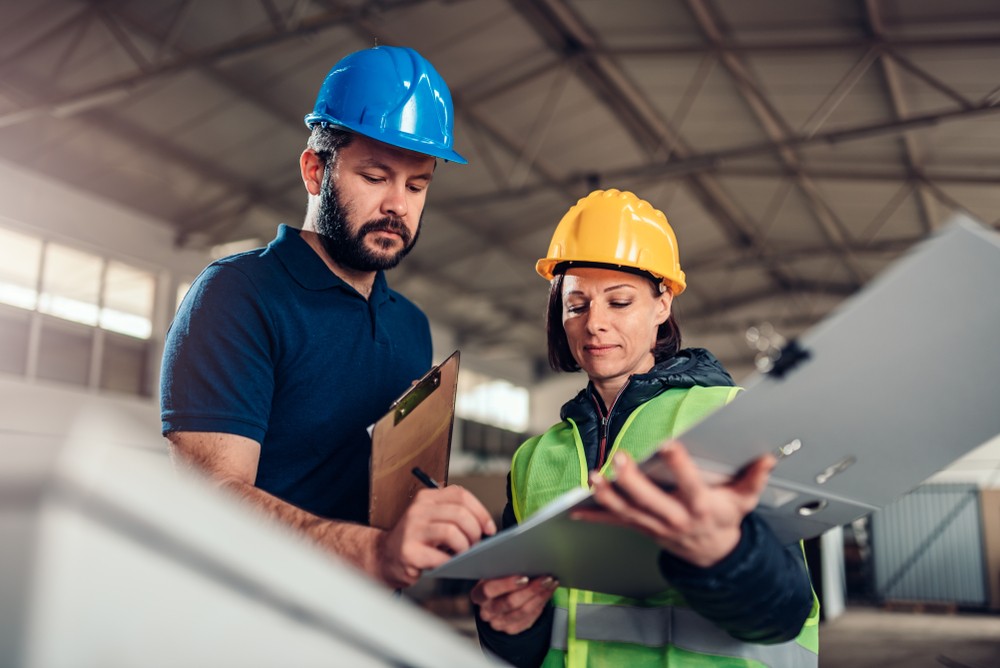
Maintenance technicians face the all-important task of ensuring equipment and machinery operate efficiently and reliably. From routine inspections to repairs and replacements, they’re responsible for keeping critical systems and components in good working order. But with so many tasks to perform and details to remember, even the most experienced technicians may overlook crucial steps or make mistakes.
This is where the checklist comes into play. A simple, step-by-step guide to maintenance procedures can go a long way in helping technicians stay organized and focused. And as a repeatable standard, a checklist is the key to reducing the risk of errors while improving the efficiency of maintenance efforts.
The benefits of a simple checklist
Today’s most successful manufacturers understand the importance of following a simple, detailed maintenance checklist. The simplicity is what makes a checklist so effective. Introducing a standardized approach to equipment maintenance yields a wide range of benefits, including:
- Increased efficiency and productivity, since checklists are prescriptive and incremental
- Improved consistency and reliability of maintenance tasks, as checklists create repeatability
- Reduced errors and mistakes, because checklists illustrate best practices in order
- Enhanced communication and collaboration among maintenance team members
Checklists put everyone on the same page. They create standards for who, what, where, when, and why to make it easy to achieve the desired results — or trace the root of a problem when something goes wrong. In short, a checklist creates consistency.
How to create an effective checklist
After assessing your manufacturing environment and establishing key maintenance goals, you can start drafting a checklist for your enterprise. Include all relevant actions and elements, and ensure each item is easily understood by anyone who needs to use the checklist, such as maintenance personnel, equipment operators, floor managers, etc.
The best way to create an effective checklist is to go through the motions of a particular task or action item and document each step sequentially. Keep in mind a good checklist will evolve as the process does, so creating a new checklist is simply about establishing guardrails to guide appropriate action.
Once you have all the steps (in order), pare them down for succinctness and clarity. All relevant details must be included, but each step should be as simple and straightforward as possible. This might mean breaking steps into subtasks or referring users to a diagram. Remember, the best checklist eliminates any room for misinterpretation.
Best practices for using a checklist
Once you have your checklist, train and standardize procedures against it. Walk the entire team through the checklist in real time. Train new personnel using the checklist. Tie KPIs and task criteria back to the checklist. Do whatever it takes to ensure a maintenance technician’s best resource is the checklist and it’s their first instinct to check and follow it.
Above all, get buy-in from your team. They won’t use a checklist they don’t trust. Take their questions, concerns, and suggestions under advisement. By encouraging open communication and the sharing of ideas, you’ll continually improve your checklists — and, by association, the caliber of your maintenance program.