The 3 Keys of TPM: Detection, Restoration, and Prevention
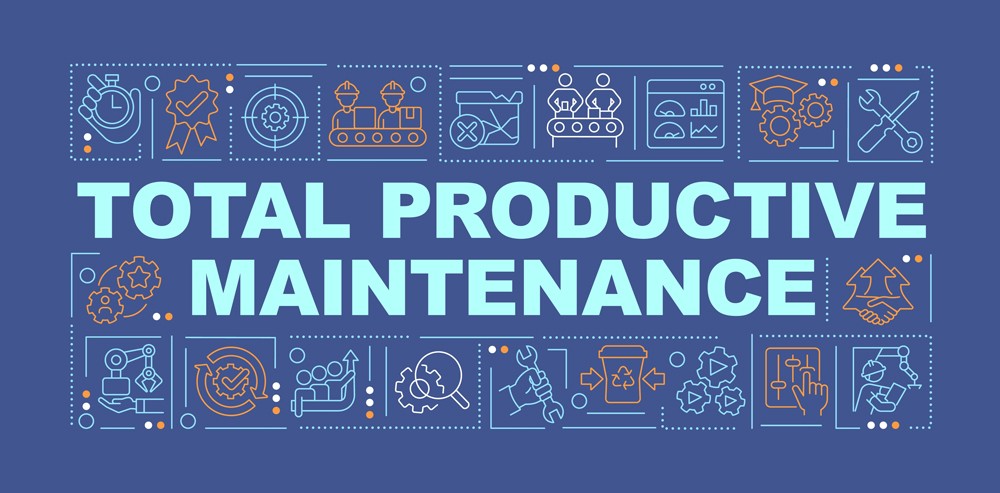
Total productive maintenance (TPM) is a powerful approach to improving the efficiency and effectiveness of manufacturing operations. At its core, TPM focuses on maximizing equipment availability and reliability through a combination of proactive maintenance and continuous improvement.
As manufacturers seek to create reliability across the value stream, TPM becomes a critical concept to consider. It starts by drilling down into detection, restoration, and prevention practices.
Understanding TPM
In simplest terms, TPM is a systematic way of preventing equipment breakdowns or deterioration through regular maintenance checks and continuous improvement efforts. The goal of monitoring TPM is to achieve maximum equipment effectiveness, lower overall maintenance costs, and improved product quality. This comes down to keeping equipment running efficiently while minimizing unexpected downtime. By properly maintaining equipment, manufacturers can decrease total losses due to downtime, reduce defects, and increase production output.
TPM is closely connected to other facets of lean manufacturing and Six Sigma practices. It emphasizes teamwork, continuous improvement, and waste reduction. Proper TPM implementation can help manufacturers attain their goals of high-quality products, increased efficiency, and profitable operation.
The keys to TPM excellence
TPM goes far beyond servicing equipment correctly or according to best practices. For an approach rooted in TPM, manufacturers must shift their mindset from reactive thinking to proactive standards.
The focus of TPM is to keep equipment running reliably through a set of key principles. These principles include detection, restoration, and prevention:
- Detection. Proactive companies identify issues before they escalate into more significant problems resulting in downtime or equipment failure. How are you becoming aware of problems before they reach the point of downtime?
- Restoration. Properly maintaining equipment helps manufacturers respond promptly, efficiently, and effectively whenever equipment issues arise. What are you doing to quickly service equipment and maintain production quality?
- Prevention. By following a proactive approach to maintenance, manufacturers can avoid potential problems with machines in the first place. The result is less downtime and a longer lifespan for assets. Are you servicing equipment before it fails?
Take a proactive approach to TPM
Manufacturers aiming to promote reliability in their operations must prioritize TPM. This approach maximizes machine uptime, reduces downtime, and improves overall equipment effectiveness (OEE). TPM isn’t just about fixing machines when they break down; it requires a commitment to continuous process improvement.
When companies commit to being proactive, they avoid costly downtime and decrease the need for reactive maintenance, making operations more dependable and efficient. In short, embracing TPM is a smart and strategic move for any organization seeking to increase reliability and achieve manufacturing excellence.