The Squeaky Wheel Gets Too Much Grease, When Good Intentions Lead To Repair
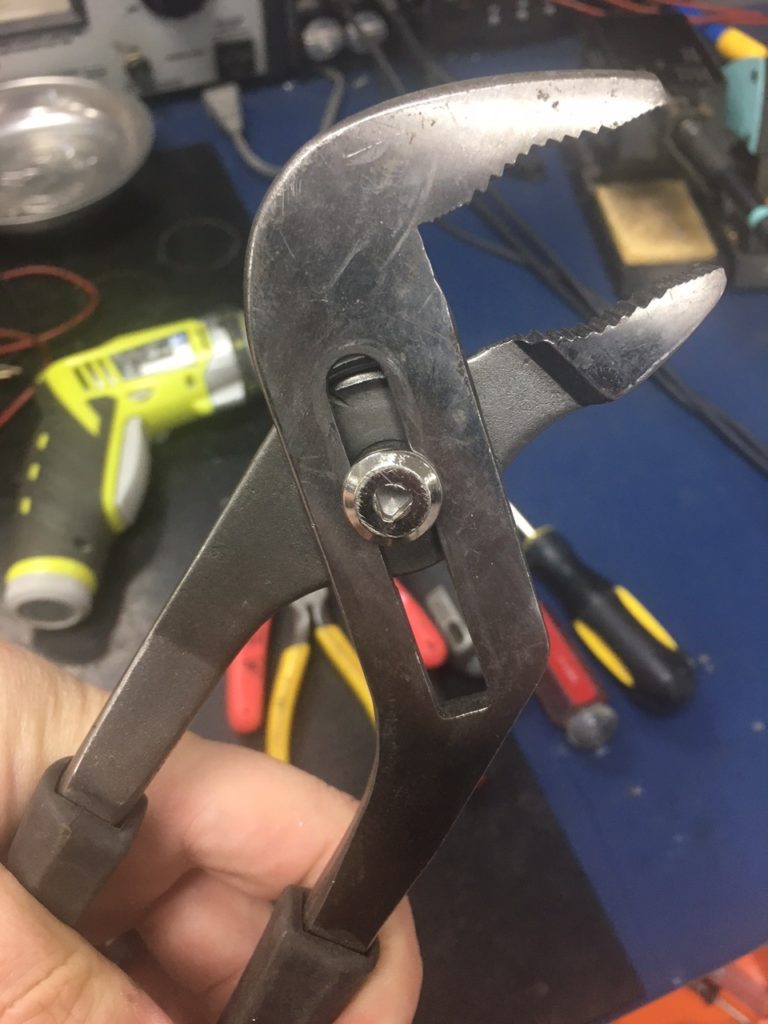
So the question that I posed to the technicians was this: are there any specific industrial electronics, motors, servo motors, hydraulics or pneumatics you see that are a direct result of the maintenance crew trying to do good, but end up intensifying or creating the problem? Needless to say there was quite a bit of spirited debate around the shop on whether I should cover this topic. While interviewing I heard, “what are you trying to do with this article Chris, put us out of work”, as a response! But in the interest of sharing knowledge, here are a few of the best answers I received on how some of these problems and failures on the units could have been prevented.
From Bill in the Hydraulics shop:
“Channel locks. Throw them out. I mean it. Collect them from every maintenance guy’s toolbox and throw them in the scrap bin. They strip bolts, gouge metal and otherwise tear up every piece of metal they touch. One of the most common things we see is a crewman tugging on a locked down cylinder with a pair of channel locks trying to free it up, and turning what would have been a simple job replacing some bad packing into now having to machine up a new shaft.”
From Terrance in the Controls Department:
“How you unplug things is important. We see so many connector repairs that could be avoided. On PLC racks those little swinging plastic locks are there for a reason! Don’t just yank the card out. If something doesn’t immediately slide out, it wasn’t meant to move! You are doing something incorrectly. One of the best examples I can think of is on the analog Eagle timers we repair. A maintenance man will have one that fails and instead of releasing the lock and slowly pulling straight out, they will uninstall using a twist of the arm, which will shatter the retaining ring on the rear connector making the repair much more difficult and time-consuming.”
From Javier in the Motor Shop:
“Too much grease. A lot of times a motor will fail in a plant and lead to some panic. Especially if the machine is down. So a supervisor will come down and order PM’s on every motor in the place. Good intent, but bad idea. What happens is that the maintenance crew will over grease everything and that grease is going to push right past the bearing and into the motor windings. We see a lot of motors that need rewinds as a result.”
From Lyle in Drives Repair:
“Label your wires. Take PICTURES! Take more pictures than to think you need. So many times we will fix a drive, only to have maintenance try to reinstall it from memory. You cannot accurately keep track of many wires purely from your memory. As stupid as it sounds the most common one I see is folks putting motor leads where input leads should go and vise-versa. Quickest way to blow up a drive and it happens more than you think.”
From Randy in the Motor Shop:
“Over torque. When reinstalling some of these motors we see a lot where someone wanted to just crank down on everything as hard as it will go. If you are tightening bolts to the point where they chew down into the metal you are over doing it. Also, tighten things evenly, if you have one side offset, then vibration will occur, and in motors that eventually leads to needing to be repaired.”
There you have it. A little advice from the guys at the ground floor. While we appreciate the repair business, we also want our customers to have as much uptime as possible. But as we all know, stuff happens, and if it does, we are always here to fix it!
Cheers as always!
Please share your comments or questions with us below and be sure to visit gesrepair.com or call us at 1-877-249-1701 to learn more about our repair services. We’re proud to offer Complete Repair and Maintenance on all types of Industrial Electronics, Servo Motors, AC and DC Motors, Hydraulics and Pneumatics. Please subscribe to our YouTube page, Like Us on Facebook! Thank you!