Six Proven Tips for Reducing Changeover Times
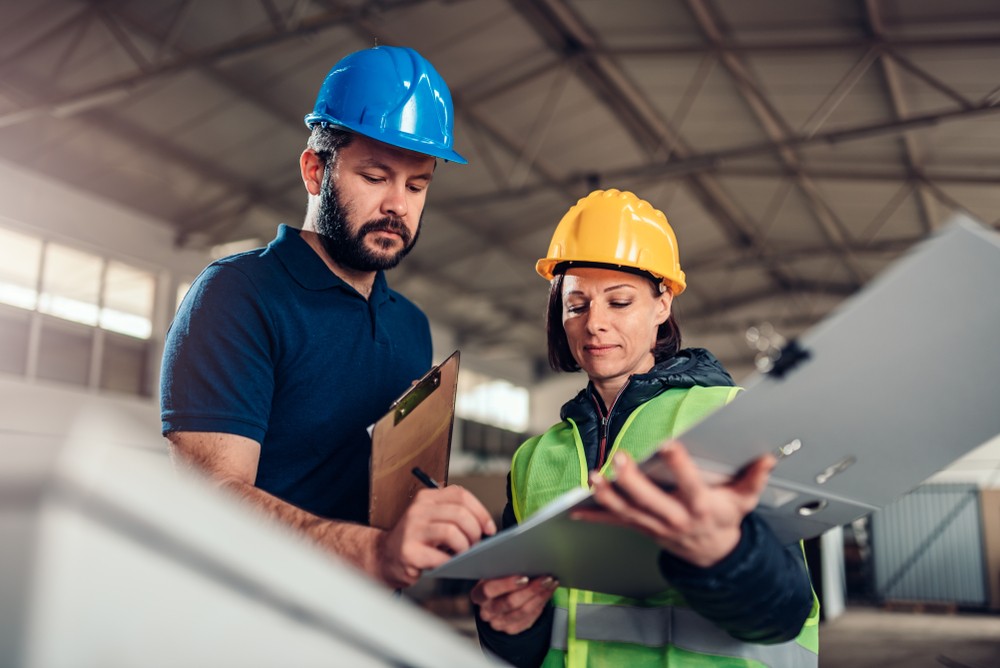
Changeovers may be planned downtime, but they are still downtime, and downtime is the bane of manufacturing. Too make matters worse, changeovers aren’t always as simple as they seem, so what promises to be a simple die swap suddenly gets complicated, raises unexpected challenges, and takes much longer than it should.
Many manufacturers are resigned to changeovers as the hassle they can be. Others go on a quest striving to adopt Single-Minute Exchange of Die (SMED) principles. For most manufacturers, the answer to quicker, more efficient changeovers lies somewhere in the gap between these two extremes.
For your next planned downtime, follow these simple, proven tips for reducing changeover times and improving processes and procedures.
- Use a checklist or standard operating procedure (SOP). A visual aid makes changeovers easier to coordinate. Use a simple checklist to keep track of all tasks leading up to a changeover, and use an SOP to facilitate the changeover itself according to proven, refined practices. Keep a record of the changeover process to help supervisors maintain and update the SOP as they find new, better, or more efficient methods for completing changeovers. Print relevant prep checklists and SOPs, and keep them near changeover areas for quick reference.
- Preparation. Proper preparation is the key to success. Gather and prepare all the necessary parts, including paperwork, tools, gauges, fixtures, and materials. Begin by placing tools and other essential items in one designated area, so they’re easier to find and access. Coordinating changeover prep reduces errors typically associated with component swaps. Maintenance techs can review each part to ensure it is correct and in good working condition.
- Make minor repairs. Don’t leave broken items for setup operators to handle. If something is broken, take the time to fix it. Setup operators can then focus on facilitating the changeover. Develop contingency plans for addressing problems that may arise during the changeover. Practice quick assessments to minimize extended downtime.
- Coordinate change tasks. While many companies have one designated setup person, changeover teams can prevent mistakes — particularly with more complicated machinery. Implementing setup teams also helps reduce total setup time. The machine’s operator should always be part of the changeover team. Familiarity with a particular machine makes operators uniquely qualified to identify problems or opportunities for improvement.
- Practice and training. Comprehensive training and hands-on practice are the best way to learn how to complete a successful changeover. Drill workers on proper preparation, processes, and procedures. Practice builds confidence and capability for quick, efficient changeovers with fewer errors in less time.
- Use changeover aids. From bridge clamps to pneumatic nips and idlers to attachments, changeover aids can reduce the time it takes to successfully complete the process. Whether a manufacturer invests in OEM recommended aids, or engineers and tests its own custom aids, incorporating specialized tools increases changeover efficiency.
Be thorough in your approach to changeovers. Preparation, performance, and precision are key elements in a quick and competent changeover routine. Follow these tips to turn troublesome changeovers into a swift and agile practice with less downtime and fewer unexpected issues.