Scrum Benefits for an Agile Maintenance Team
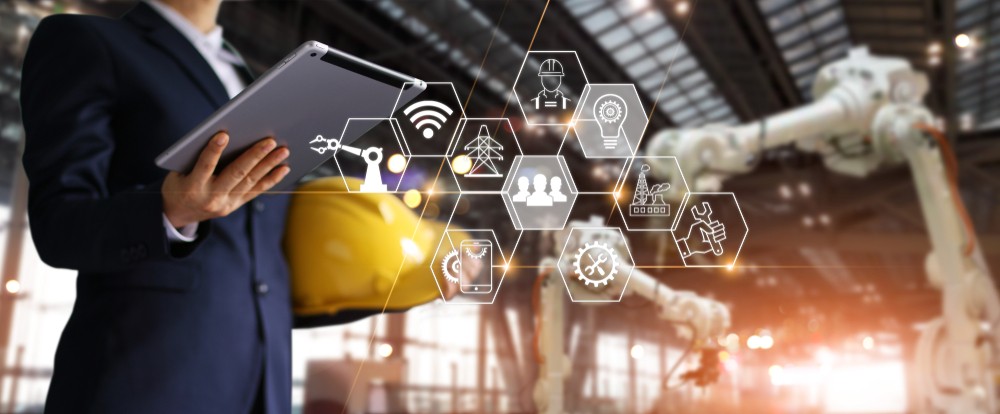
Many manufacturers struggle with the idea of proactive maintenance because it involves a lot of data and several unknown variables. Switching from a reactive to a proactive maintenance approach requires a massive shift in thinking and revision of current maintenance policies and procedures. This can be overwhelming without a framework for guidance.
In lean manufacturing environments, agile frameworks — particularly scrums — are one source for necessary guidance. Scrums allow maintenance teams to take things step by step to slowly transition to a new and evolving model. Instead of a massive, disruptive push for instant change, scrums finesse transformation and ensure it continues to yield results.
The benefits of scrum
Maintenance demands are always changing — especially for manufacturers seeking continuous improvement from their approach. Scrums embrace the changes of living, breathing processes within the factory environment. Here’s how it works:
- Maintenance teams start with a list of objectives and tasks (i.e., a product backlog).
- Teams select projects from the backlog to focus on in a sprint.
- During sprints, the teams engage in formal planning, check-ins, reviews, etc. (i.e., ceremonies).
- At daily scrums, the team quickly recaps its objectives and requests help if needed.
- At the end of a sprint, the team recaps the process and plans for the next step (i.e., the retrospective).
Scrums are cycles. After every sprint and retrospective, the team starts on another task from the project backlog. The result is a system continuously advancing toward a larger goal. In the case of maintenance teams, this might mean moving from reactive to proactive standards and then continuing to the next step for optimizing your approach to factory maintenance.
A closer look at the scrum framework and roles
To understand agile frameworks, first get a handle on their vernacular. There are a few key terms and roles to understand, including:
- Artifacts. Anything brought to the scrum that plays a role in the direction of a sprint.
- Sprints. Short, iterative, bite-sized tasks that translate into more meaningful change.
- Ceremonies. Phases of a sprint where the work is done and reviewed.
- Retrospectives. Final ceremonies that mark the end of a sprint and a recap of results.
- Milestones. Provide updates on progress within an evolving system to show growth.
- Product owners. The owners of a particular task charged with running the sprint.
- Scrum masters. Scrum experts who ensure all sprints are running smoothly.
- Scrum teams. Those doing the work within a particular sprint.
Scrums and agile frameworks are immersive, which means there’s a host of terms and processes to understand. Manufacturers considering the scrum approach should formalize training or hire project managers with strong scrum backgrounds.
The never-ending quest for improvement
Scrums are rooted in the world of software and product development, but they’re increasingly popular for manufacturing maintenance teams. Why? Because the framework supports continuous improvement, new variables, changing standards, and general growth. In the factory environment, maintenance is always in flux. Scrums support this uncertainty by rooting critical tasks in an adaptive framework.
Put simply, scrums acknowledge the unpredictability of factory maintenance without compromising the maintenance response.