Retrofitting Trends: Upgrading Legacy Drive Systems for the Future
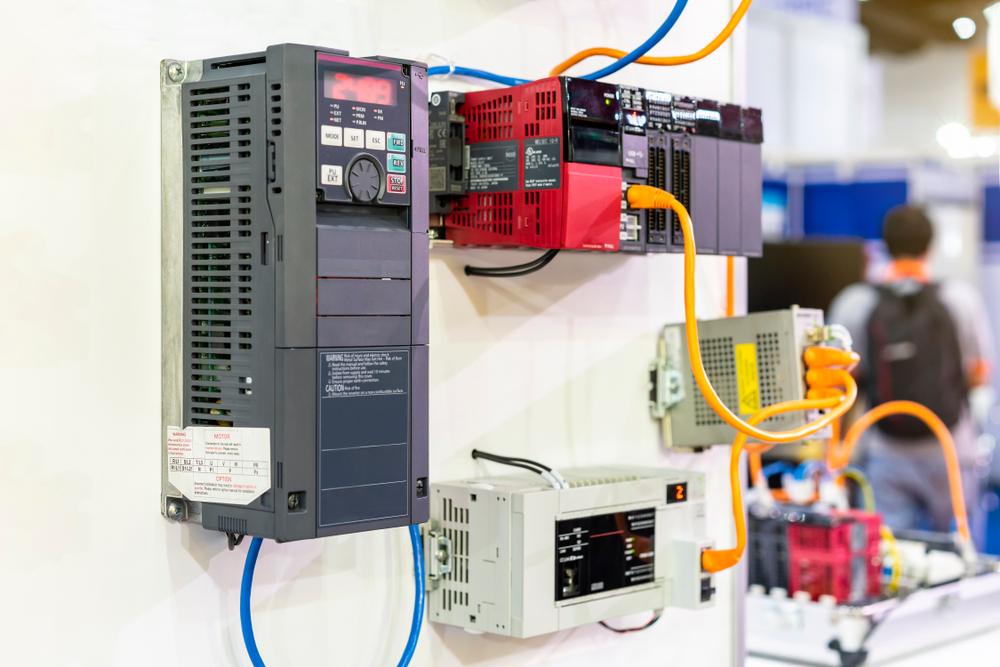
Legacy drive systems have reliably powered manufacturing for decades, but they’re beginning to show their age. Upgrading these systems isn’t just about keeping up with the times; it’s about staying competitive as the pace of production increases.
Retrofitting offers a smart alternative to wholesale replacement, letting manufacturers leverage existing infrastructure while embracing new-age technology. It’s a strategic move that pays dividends in both the short and long term, and several undeniable factors are pushing manufacturers toward retrofitting:
- Energy efficiency is no longer optional. With rising energy costs and stricter environmental regulations, upgrading to more efficient drive systems is a no-brainer. Modern drives can slash energy consumption by up to 50%, delivering significant savings.
- Performance demands are ever-increasing. Legacy systems often struggle to keep up with the precision and speed required by today’s manufacturing processes. Retrofitting with advanced drives can boost productivity, improve product quality, and reduce downtime.
- Integration is key. As factories become smarter, legacy drives can become isolated in a network of connected systems. Retrofitting these drives can enhance communication with modern control systems, to unlock benefits like data-driven decision-making and predictive maintenance.
- Cost considerations can’t be ignored. While a complete system overhaul might seem tempting, retrofitting offers a more budget-friendly approach. It allows manufacturers to upgrade incrementally, spreading capital costs over time.
Retrofitting strategies for success
In the same way every production environment is different, there’s no one-size-fits-all approach to a drive retrofit. Manufacturers can employ various strategies to bring their legacy systems into the future:
- Upgrading to VFDs: Variable frequency drives offer precise speed control, energy savings, and improved motor protection. Plus, they come with features like built-in PLC functionality and advanced diagnostic capabilities.
- Implementing advanced motion control: Precision is paramount in quality manufacturing. Retrofitting with advanced motion control systems allows for tighter tolerances, smoother operation, and increased throughput.
- Integrating IIoT and connectivity: Retrofitting legacy drives with IIoT-enabled components allows for real-time monitoring, predictive maintenance, and data-driven optimization. It’s about making old systems smarter.
- Enhancing safety features: Modern drive systems come with advanced safety features that can be retrofitted onto legacy equipment, including safe torque off and advanced emergency stop functions.
OCTOBER SPECIAL: DISCOUNT DRIVE REPAIRS
Not ready to retrofit yet? Through October, GES is offering a special on AC drive repair: All month long, you can get 10% off any single drive repair or 15% off three or more repairs!
Future-proofing through retrofitting
It’s important to remember that retrofitting isn’t just about solving today’s problems — it’s about preparing for tomorrow’s challenges. Retrofits should be made with future upgrades in mind, so they’re capable of supporting the integration of new technologies as they emerge. This means considering factors like:
- Data collection and analysis capabilities
- Cybersecurity and connectivity features
- Compatibility with control and communication systems
Regardless of how it’s done, retrofitting legacy drive systems is a smart move for manufacturers looking to stay competitive. It offers a cost-effective way to boost efficiency, enhance performance, and prepare for the future of Industry 4.0. Don’t let legacy systems hold you back. Assess your current infrastructure, identify opportunities for improvement, and start planning your retrofitting strategy today.