Repair Considerations in Harsh Environments – A Look at Two Industries
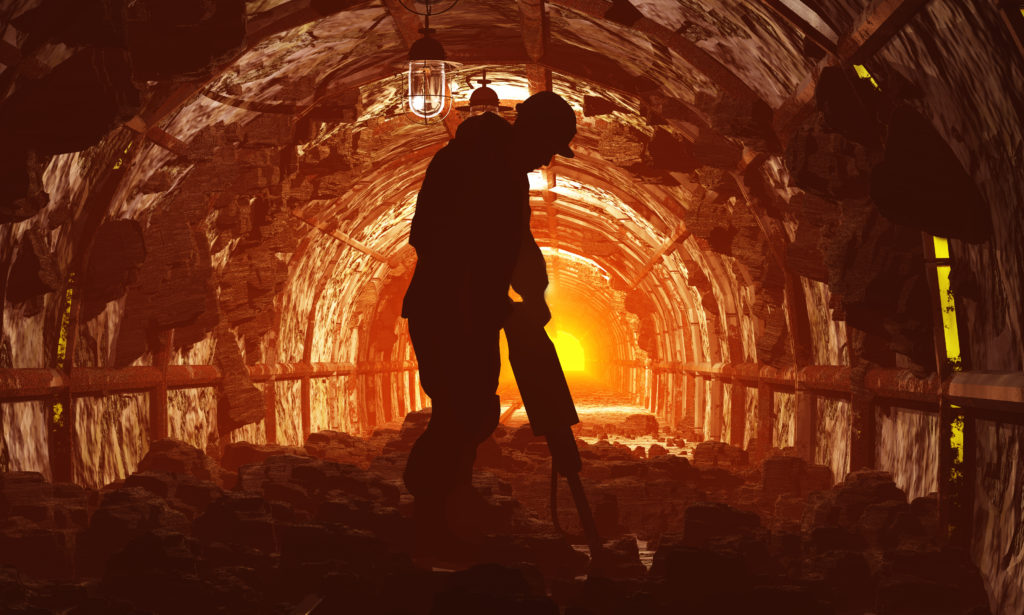
Because we service such an extensive range of products we see repairs coming from a very wide breadth of industries. While repairs coming from most manufacturers are fairly straightforward, some industries more than others have very specific challenges they must overcome to properly maintenance their equipment as well as needing to make sure their repair program is a success. Below are two industries that could not be more different but have particularly challenging repair concerns due to harsh environments.
Mining
In 2015 The National Institute for Occupational Safety and Health (NIOSH), reported that there were currently 13,294 active mining operations in the US alone. Modern mines contain many machine devices both mechanical and electrical that are prone to failure and often need repair. Some of this is due to the environment that they are in. Debris and dust become an insulator on electronic components and will cause overheat failures. These are caused by either the cooling failure (fan failure, clogged vents and heat sinks) or by components being covered with contamination.
One of the more challenging aspects of mine maintenance is time. Within a mine it is imperative that maintenance crews spend their time as efficiently as possible working out a problem because extended time spent underground is inherently dangerous. The quarters are often cramped and dust buildup can create a dangerous environment that would require the mine to be emptied of personnel at a moment’s notice. In addition, time spent pulling a failed device in and out of a mine can be tricky in and of itself, as it takes time to transport the item in and out of the shaft.
The most important aspects of overcoming these concerns are planning and diagnoses.
- Planning consists of making sure that you are ready for a failure. This can take many forms but the basics are understanding what can cause your devices to fail, performing preventative maintenance whenever possible and keeping on hand spares that are critical to your process.
- Diagnoses means spending the time to perform root cause failure analysis to prevent future failures.
Food and Drug
The food and drug industry is one that faces many repair challenges as well. Within a food or drug processing plant cleanliness is given top priority and as such, machinery is cleaned often during a process called wash-down. What makes this such a harsh environment is that water and electronics simply don’t mix.
Wash-down procedures vary greatly from plant to plant. In some, maintenance personnel are exacting in their methods, putting plastic covers on sensitive electronics, checking water seals on enclosures, or otherwise taking great care in preventing a water or corrosion related failure. But some crews either skip steps if they are in a hurry or make a mistake that causes equipment to get wet and thus damage the equipment.
What makes a water related contamination failure so difficult is that it is hard to pinpoint when the failure will occur. If the device is completely submerged, then the failure will present itself immediately as the water will reroute electronic current to paths of least resistance and will cause a short within the device. The trickier failure is corrosion brought on by relatively small amounts of moisture. In this type of failure, the damage happens at a rate relative to the amount of moisture, temperature and air conditions the device was exposed to making it hard to predict.
The advice we offer these facilities is to make sure you are covering two basic preventative measures. Following proper wash-down procedures and inspecting equipment often.
- The basics of properly washing down equipment consists of making sure the equipment is powered off, bagging the appropriate devices that are not wash-down rated, and making sure the area is well clear of water and steam when the equipment is turned back on.
- Inspections in a wash-down facility need to be focused on looking for water related failures. There are two major things to look for: broken seals and corrosion. A piece of wash-down rated equipment is only as good as its sealing components, and if they are compromised the unit must be sent in for repair. In addition, if you find rust on an electrical or mechanical item the item must be serviced to prevent further damage.
So there you have it, repair concerns from two very challenging industries. Is your maintenance work in a challenging environment? Let us know! We would love to read your comments below! Also be sure to visit us online at gesrepair.com or call us at 1-877-249-1701 to learn more about our services. We’re proud to offer Surplus, Complete Repair and Maintenance on all types of Industrial Electronics, Servo Motors, AC and DC Motors, Hydraulics and Pneumatics. Please subscribe to our YouTube page and Like Us on Facebook! Thank you!