Reconfigurable Manufacturing Systems: What They Are and Why They’re Important
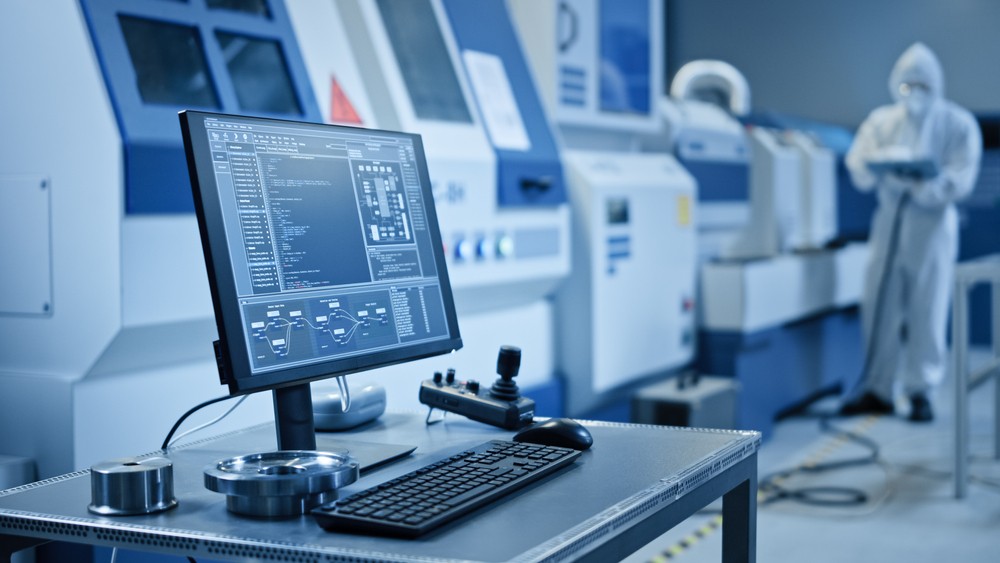
The manufacturing industry has undergone a digital revolution in recent years. While most people recognize the significance of the cloud, artificial intelligence, and machine learning, another concept deserves equal attention: reconfigurable manufacturing systems. These highly flexible, adaptive systems allow manufacturers to easily adjust their production capacity and functionality in response to changes in market demand.
Key features
A reconfigurable manufacturing system (RMS) is a purpose-designed framework that can quickly alter its structure, hardware, and software components. This adaptability allows the system to rapidly adjust its production capacity and functionalities, specifically within a defined part family. In simplest terms, it’s a production line that can produce many different components.
The driving force behind an RMS lies in its capacity to respond to sudden market shifts or intrinsic changes within the system. An RMS is characterized by six defining features:
- Modularity: An RMS is constructed from modular components that can be easily rearranged or replaced. This design facilitates swift reconfiguration for the production of diverse products or parts.
- Integrability: Components within an RMS are seamlessly integrated, both physically and electronically. This ensures cohesive system functionality even during the reconfiguration process.
- Customized flexibility: An RMS can be tailored to align with the specific requirements of a manufacturing application. This customization enhances production flexibility and minimizes the need for specialized equipment.
- Scalability: The scalability of an RMS allows for seamless adjustments to meet fluctuating production demands. This versatility is a valuable asset for manufacturers navigating variable market conditions.
- Convertibility: An RMS can be converted for the production of different products or parts with minimal effort. This adaptability empowers manufacturers to quickly respond to shifts in market demand.
- Diagnosability: Designed with the ease of diagnosis and repair in mind, an RMS minimizes downtime and maximizes overall productivity by promptly addressing potential issues.
Adopting an RMS
When manufacturers successfully embrace the concept of an RMS, they make their production processes more agile. Here’s how producers can incorporate an RMS:
- Invest in flexible manufacturing systems. A flexible manufacturing system (FMS) is an essential component of an RMS. By investing in an FMS, companies can automate their production processes and reduce errors. An FMS can also help manufacturers be cost-effective and better allocate their resources.
- Implement agile manufacturing processes. Agile manufacturing involves having a highly flexible and responsive production process. This concept allows manufacturers to be more responsive to market changes and customer demands. Agile manufacturing can also help companies reduce production time, increase product quality, and lower production costs.
- Use advanced analytics and machine learning. Through analytics and machine learning, manufacturers can optimize their production processes and achieve greater efficiency and productivity. These technologies enable producers to identify areas needing improvement and make informed decisions.
The ultimate results of an RMS are increased productivity and reduced costs. By adopting reconfigurable manufacturing systems, companies can better pinpoint issues so they can address them quickly and correctly. All told, these systems are the future of agile manufacturing.