Production Line Down – Repair Or Replace…What Do You Do?
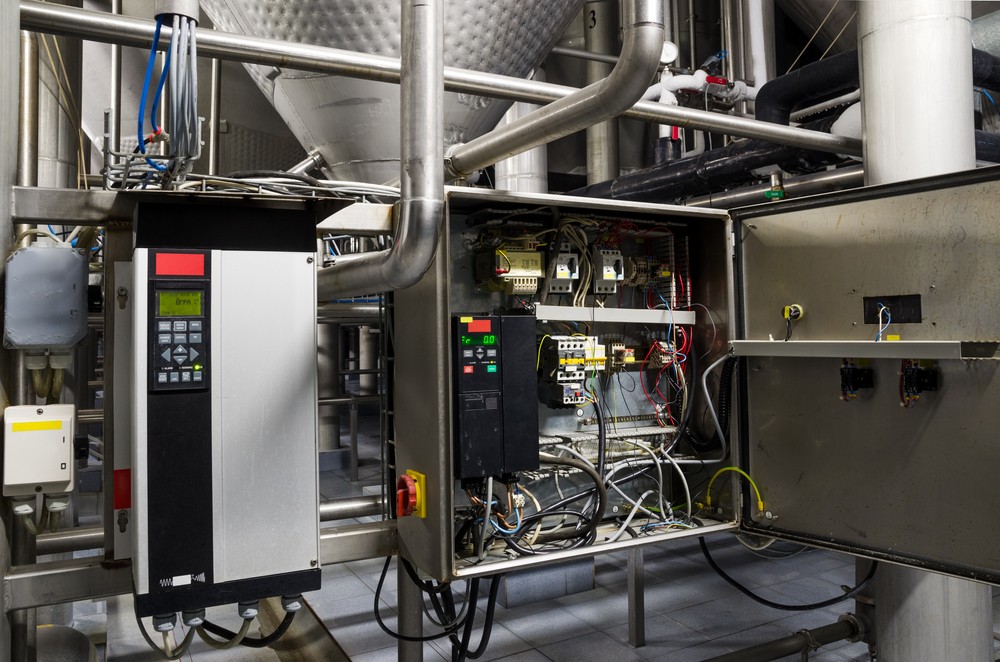
It’s 2am on Saturday night and your production line has been running flawlessly and you are just ahead of schedule. Just as you are making your rounds you get a call on the radio that a variable speed drive faulted out, and the main line is down and can’t run without it. Thinking to yourself sounds like no big deal; you make you way down to the parts crib to find out that you do not have a spare one on the shelf. You are left with one BIG decision. Repair or replace….what do you do?
There are a few things that most teams will consider when making this decision, but there are many advantages that have customers choosing the repair every time.
Less down time!
Whenever a drive, plc, circuit board, motor, valve, etc. fails on a production line, the primary goal is to get the line back up and running as fast as humanly possible. Often times the first thing one might think is where can I get a new one of these to get up and running. If you are dealing with a unit from a machine that was made 10 years ago or more that might be easier said than done. You might be looking for a unit that is obsolete, on back order or even has to be custom made from the OEM. Choosing to repair can get you back up and running in a matter of days or even in hours in some cases keeping downtime to a minimum.
Cost savings!
Repairing industrial electronics, motors, and hydraulics can provide a huge cost saving that can be allocated towards new projects. Repairing this equipment can provide a cost saving of at least 50% off of the price of a new unit which includes fully refurbishing your repair and giving it a warranty that is better than when it was new. Another way of looking at it is you can get two units repaired for the price of one new unit. One can be in production, the other on the shelf as a spare.
Your software, your parameters!
When choosing repair you get your same unit back with all your stored parameters and software in it. If a new unit is decided on often times you will have to send your old unit in as a core and you will get back a unit that requires some retrofitting. Customers have indicated they spend many hours reinstalling the software or parameters on a new unit after they receive it. Sending the unit in for repair means you get your unit fully refurbished and you get to keep your existing software and stored parameters.
No matter what industry you might be in from wood processing, plastic manufacturing, chemical, to food processing; repairing your unit that has failed is always be a great way to save money and most importantly minimize your downtime.
Please share your comments or questions with us below and be sure to visit gesrepair.com or call us at 1-877-249-1701 to learn more about our services. We’re proud to offer Surplus, Complete Repair and Maintenance on all types of Industrial Electronics, Servo Motors, AC and DC Motors, Hydraulics and Pneumatics. Please subscribe to our YouTube page and Like Us on Facebook! Thank you!