Preventing Cavitation and Ensuring Pump Efficiency
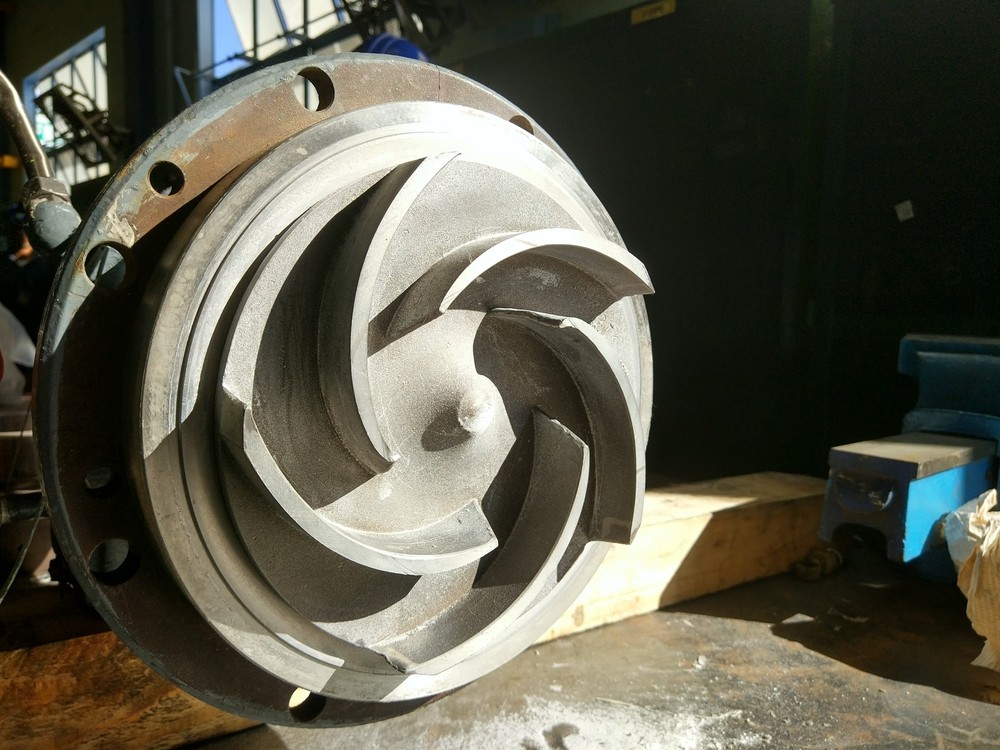
Pumps are the workhorses of industry, quietly but crucially keeping liquids flowing in everything from water treatment plants to industrial cooling systems. But a hidden issue can slow and weaken these workhorses: cavitation. This phenomenon can significantly reduce pump efficiency and lifespan if left unchecked.
Bubble trouble: What is cavitation?
Cavitation occurs when the pressure within a pump falls below the vapor pressure of the liquid it’s carrying. This creates tiny vapor bubbles that form and collapse rapidly. While these bubbles might seem insignificant, their implosion generates high-energy shockwaves, wreaking havoc on pumps.
Imagine throwing a pebble into a still pond — the ripples spread outward. Cavitation is similar, but with much more force. These repeated shockwaves can erode the pump’s impeller, leading to increased noise, vibration, and pump failure in some cases.
The consequences of cavitation
The consequences of cavitation are far-reaching. First and foremost, it hampers pump performance. A cavitating pump simply can’t move liquid as effectively as it should. This translates to higher energy consumption and potentially even insufficient flow rates.
The noise and vibration caused by cavitation are warning signs of damage. These symptoms arise when bubbles are sandblasting the inside of the pump and wearing down the impeller. Left unchecked, this erosion can lead to complete pump failure, resulting in costly repairs or replacements.
Solutions for cavitation
Any amount of cavitation is enough to cause problems for pumps and impellers. But cavitation is preventable. Here are some key strategies:
- Choose the right pump. Net positive suction head (NPSH) is a crucial concept here. NPSH refers to the minimum pressure a liquid needs to have at the pump inlet to avoid cavitation. There are two types of NPSH: NPSHa (available) and NPSHr (required). To prevent cavitation, NPSHa should always be greater than NPSHr. Selecting a pump with an NPSHr that matches your system’s NPSHa is essential.
- Optimize piping design and maintenance. Friction in the suction piping can significantly reduce NPSHa. Using larger-diameter pipes and smooth bends helps minimize friction losses. Maintaining a proper liquid level in the suction reservoir ensures the pump has enough liquid available to avoid cavitation. Regularly inspecting suction piping for leaks and air entrainment is also crucial.
- Use booster pumps when needed. In some cases, system conditions might make it difficult to achieve the required NPSHa. Here, auxiliary equipment like booster pumps can be employed to increase the pressure at the pump inlet, effectively preventing cavitation.
Keeping pumps healthy and functional
By understanding cavitation and taking preventive measures, manufacturers can ensure pumps operate efficiently and last for years to come. Remember, proper pump selection, system design, and regular maintenance are key. If you’re unsure about your specific application or facing cavitation issues, don’t hesitate to consult with a pump expert. We can help you diagnose the problem and recommend the best course of action to keep your equipment operating at peak performance.