Motor Shaft Voltage Damage: Why It Happens and How to Prevent It
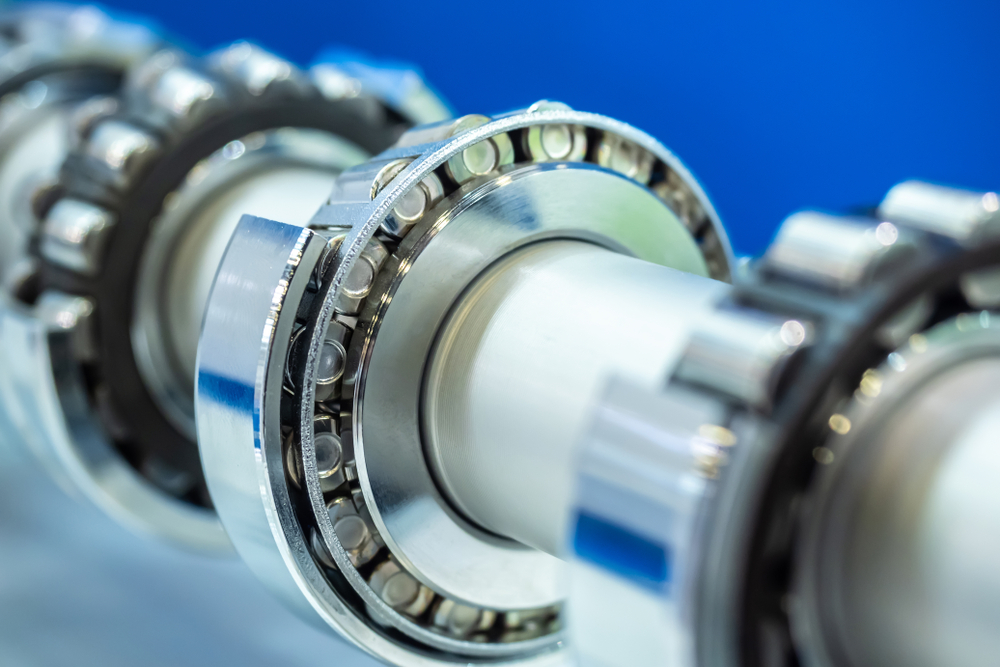
You don’t have to see sparks flying to know shaft voltage is a problem. The damage is subtle at first — minor pitting, strange noises, heat — but once bearings start to break down, failure moves fast. And when it does, downtime gets expensive. Most shaft voltage issues start with one root cause: high-frequency currents induced by variable frequency drives (VFDs). Here’s how to catch it early and what to do if the damage is already done.
What causes shaft voltage buildup?
VFDs are nearly universal in modern industrial environments. They improve efficiency, optimize control, and reduce energy waste, among other benefits. But they also create high-frequency switching pulses that can induce voltages onto nearby motor shafts. If those voltages don’t have a safe path to ground, they’ll find one — usually through the motor’s bearings.
As stray voltages travel along the motor shaft and discharge through the bearings, they carve microscopic pits that quickly snowball into fluting, noise, and, ultimately, motor failure. High switching frequencies and long motor cable runs make the problem worse. So do poorly grounded systems or motors with insulated bearings. Without proper mitigation, those voltage pulses can reach damaging levels quickly.
Common warning signs
- Bearing noise: A high-pitched whine or rumble often means the raceways are damaged.
- Excess vibration: Irregular torque from uneven bearing surfaces can shake the motor housing.
- Unusual heat: Friction from fluting increases operating temperatures, even under normal load.
- Failed bearing inspections: If a post-mortem reveals electric fluting, shaft voltage is almost always to blame.
Need electric motor service?
If you suspect shaft voltage buildup, contact GES. Now through the end of the month, we’re offering 10% OFF single repairs or 15% OFF 3+ repairs on ABB products, for an affordable way to keep your motors running!
How to stop shaft voltage discharge
Preventing damage starts with giving stray voltage a better path to ground. That can mean modifying your setup or installing hardware built specifically for this purpose. It’s often a combination of grounding, shielding, and hardware upgrades that gets the best results:
- Install shaft grounding rings: These conductive brushes redirect voltage from the shaft to ground.
- Use insulated bearings: Motors with insulated bearings on the non-drive end can stop current from circulating.
- Shorten motor leads: Long cables act like antennas, amplifying the voltage induced by high-frequency switching.
- Upgrade VFD filters: Some VFDs include common-mode filters that suppress shaft voltage buildup at the source.
If you suspect a voltage issue, don’t guess. Test! Using an oscilloscope with a shaft voltage probe, you can directly measure voltage levels on the shaft during operation. Readings that show repeated peaks over 40 volts — and especially those with regular discharge patterns — indicate an active problem.
Visual inspections are useful, too. If you’ve already pulled a failed motor, examine the bearings. Fluting patterns, frosting, and blackened lubricant are all signs that voltage has been discharging through the raceways.
Repairing (and resolving) shaft voltage damage
If shaft voltage has already damaged the motor bearings, you have a few paths forward. In motors where the windings and shaft are still in good condition, bearing replacement — plus the installation of a grounding ring — can extend the motor’s life. If damage spread beyond the bearings, a complete rewind may be necessary. This also gives you the chance to add insulation upgrades. For older or lower-horsepower units, full replacement might be more cost-effective than rebuilding.
Remember: The longer shaft voltage goes unchecked, the more damage it causes. Whether your motor needs a new grounding solution, a bearing replacement, or a full rewind, the team at GES is here to help. Count on us to stop the cycle of bearing failure — before it starts.