An Innovative Approach to Manufacturing: Plastic Gears

Changes in polymers and innovations in gear shape and design have allowed plastic gears to catch up to their metallic counterparts in many arenas, according to Gear Solutions magazine. Specifically, engineers have developed acetal and nylon to the point where stresses and torque on these injection-molded parts do not exceed the plastics’ abilities. Manufacturers are also increasingly employing plastic gears reinforced with small amounts of carbon fiber. Given their small amounts of strategically placed carbon fiber, total costs for these gears are lower.
Benefits of plastic gears in manufacturing
These new plastics solve many problems in gear creation and use. According to Machine Design, plastic gears function with less noise, require less lubricant or are self-lubricating, and create less inertia due to being less heavy and dense. In manufacturing processes involving wet environments and food preparation, plastic gears are safer and work better. Many of these plastic gears are shock- and vibration-absorbent given how much more elastic the materials are than metal.
Plastic gear limitations
That being said, there are still important factors to consider when choosing a plastic gear over other material choices. All other things being equal, plastic gears have less load-bearing capacity than metal gears, so it’s important manufacturers make sure they use the right size plastic gear. And, if a small gear must bear a large amount of weight, metal may still be the best option. At times, plastic gears can be difficult to attach to metal parts, and some specialty plastics are actually more expensive than base metals used in gear making. It’s important to find the right mix of smart economic choices and properties to benefit your manufacturing operations according to your company’s needs.
In many cases, plastic gears are becoming more and more useful in the processes that create manufactured goods. Even with their benefits, however, it may not be necessary to replace metal gears if metal-geared systems serve immediate needs. On the other hand, it’s important to evaluate the possibilities of plastics when designing new processes or improving manufacturing system designs. When repairing or replacing manufacturing process elements, it is important to weigh the pros and cons of plastic gears — and potentially arrive at a hybrid solution that incorporates the best of all available materials.
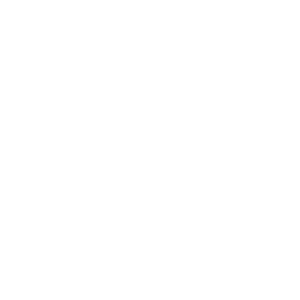