Manufacturing Employment Prospects are in Dire Straits
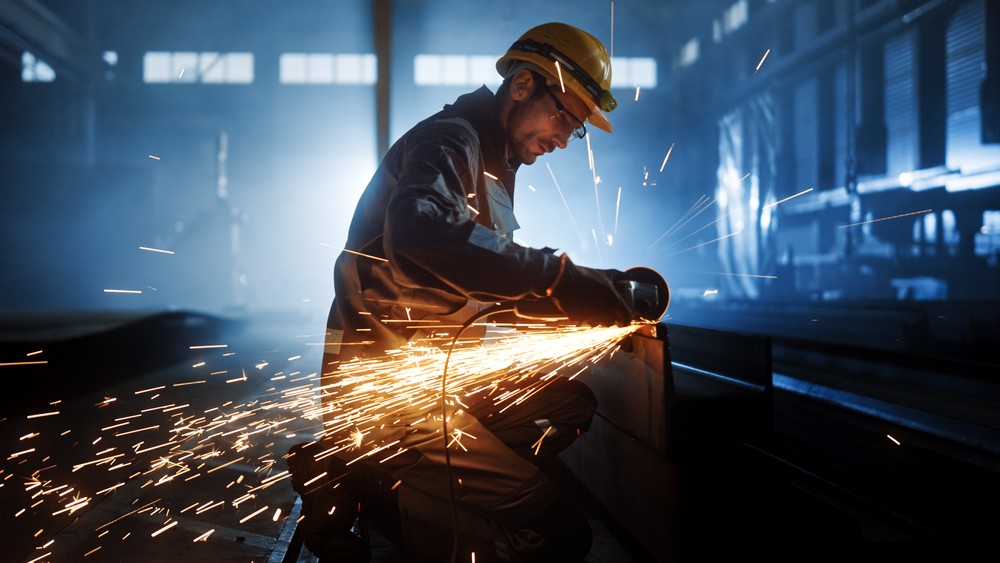
Employment struggles have long been the bane of the manufacturing industry. For decades, the gap between available positions and qualified workers has grown, and today, the labor shortage is reaching catastrophic levels. As manufacturing seeks to sustain itself, companies are ramping up their hiring efforts. Unfortunately, every other industry is doing the same, and there don’t seem to be enough workers to go around. The labor shortage is the single biggest barrier to what could otherwise be an impending domestic manufacturing boom.
Manufacturing job openings are at all-time highs
July of 2021 marked the second consecutive month of a record-breaking number of job openings in the United States. According to the U.S. Department of Labor, there were 10.2 million job openings in June and 10.9 million in July. And while there’s a small degree of turbulence in the August figures — mostly due to an increase in COVID-19 cases related to the Delta Variant — there’s reason to believe job openings will continue to set records.
From some perspectives, an increase in job openings is reason to celebrate, but it’s causing headaches for employers. Despite an unprecedented high number of job openings, hiring remained low — with only 6.8 million new employees hired in both June and July.
What’s driving the labor shortage?
Economists at Morgan Stanley recently offered three possible explanations for the current labor shortage, all related to the COVID-19 pandemic. Workforce relocation topped the list, followed by school closures and a lack of qualified candidates.
In the last year, many people relocated from urban centers to more rural areas. And while remote work opportunities mean there are many white-collar job openings available in rural areas, the availability of service jobs is sorely lacking. Urban areas have the opposite problem: too many open service positions. Currently, neither urban nor rural areas have enough of the workers they need.
Morgan Stanley also speculates that school closures contribute to the labor shortage. During the height of the pandemic, many parents were forced to take time off — or even leave their jobs — to provide proper childcare and supervise remote learning. There’s hope this issue will resolve itself with children returning to school, though the situation remains uncertain and is rapidly becoming a partisan issue.
Finally, companies across the board are struggling to find employees with the right qualifications and skills. As Contingent Macro Advisors commented, “Employers continue to struggle to find workers with the right skills, and those willing and able to work continue to be very selective.”
The pandemic sped up the Silver Tsunami
Though its arrival has been speculated for years, we could be seeing the earliest crest of the Silver Tsunami: the retiring of an aging workforce without sufficient suitable replacements.
During the pandemic, many workers of the Baby Boomer generation avoided the heightened risk of illness by simply retiring. This mass exodus of experienced workers quickly widened the employment gap in several sectors. There’s hope Generation Z will help reduce the effects of the Silver Tsunami, but the current employment squeeze has manufacturing executives nervous. That said, the 2019 L2L Manufacturing Index found 27% of Gen Z workers surveyed said they would consider a career in manufacturing.
Manufacturers are ready to get to work
With a pending multitrillion dollar infrastructure bill and increasing pressure to ramp up domestic production to support supply chains, manufacturers are entering a period of tremendous opportunity. To capitalize on it, they need access to a workforce that’s ready, eager, and able to drive growth. We don’t know how long the worker shortage will last, but we do know manufacturers face a steep uphill battle in their efforts to find, hire, and retain qualified talent.