Manufacturers Increasingly Adopt Wearable Tech
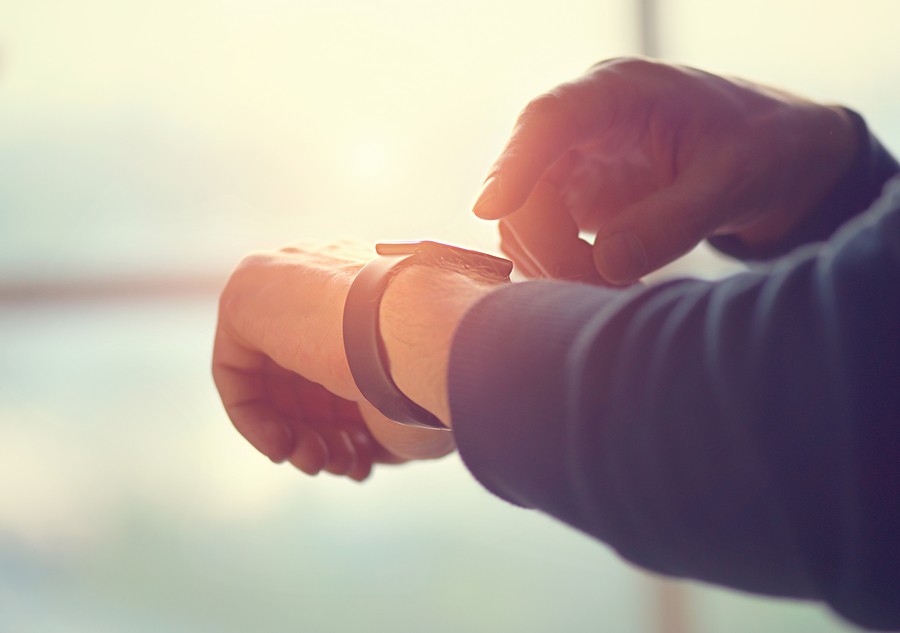
Whether it’s a Fitbit, Apple Watch, or other wearable device, modern tech is everywhere — and the manufacturing floor is no exception. But wearables in plants serve as much more than just clocks and health monitors: They also help increase safety, reducing hazards for manufacturing professionals on the floor; transparency, as employees gain greater visibility into machine functionality; and quality, as standards become more universal across the global industry. And with more manufacturers investing in wearables for employees, it’s important for industry insiders to understand what kinds of manufacturing wearables are available today and how they could change their industry.
Implementing new tech
From Google Glass to smart helmets, manufacturing leaders are quickly embracing new technologies. In fact, half of global manufacturers who took part in Zebra’s 2017 Manufacturing Vision Study said they “plan to adopt wearable technologies by 2022. And 55 percent of current wearable users expect to expand their level of usage in the next five years.”
These devices connect to machines via the Industrial Internet of Things (IIoT), for which, according to the Zebra study, use is also growing rapidly among manufacturers. In an age in which 62% of manufacturers still use pen and paper, the industry is ripe for change as analysts expect that amount to drop to 20% five years from now with 64% of manufacturing plants being fully connected by 2022. This level of connectivity means more than IIoT-enabled machines and humans, though. With radio frequency identification growing in the supply chain, manufacturers can track and verify their products’ authenticity, giving end users peace of mind and ensuring manufacturers’ reputability.
Google Glass Enterprise
The wearable formerly known simply as Google Glass is now Google Glass Enterprise with Google’s manufacturing- and warehousing-focused rebranding. In addition to its new look, Google Glass Enterprise is also lighter and made for long-term wear, allowing those on the manufacturing floor to stay connected and comfortable throughout the workday. These smart specs use augmented reality (AR) to direct workers and can even connect them to experts who can see what the employee sees to assist in work that’s out of scope for an individual.
Smart helmets
This example of wearable technology serves dual purposes: Smart helmets not only protect individuals physically in the event of an accident but they can also warn employees of unsafe areas and imminent dangers. Configured with sensors, they can warn manufacturing professionals of unsafe zones for personnel and even the unseen, such as gas leaks. Plus, smart helmets can track the number of hours a worker has been on the floor and warn against excessive hours worked in a day, which can lead to fatigue and increase risk for others in the plant.
In addition to making plants safer, wearable tech can also increase productivity, which, in turn, helps boost the bottom line. When manufacturing professionals can avoid dangers more easily, see their next steps through AR displays, and connect with one another more easily, everyone wins.