Managing Spare Parts: A Strategy for Quick and Efficient Repairs
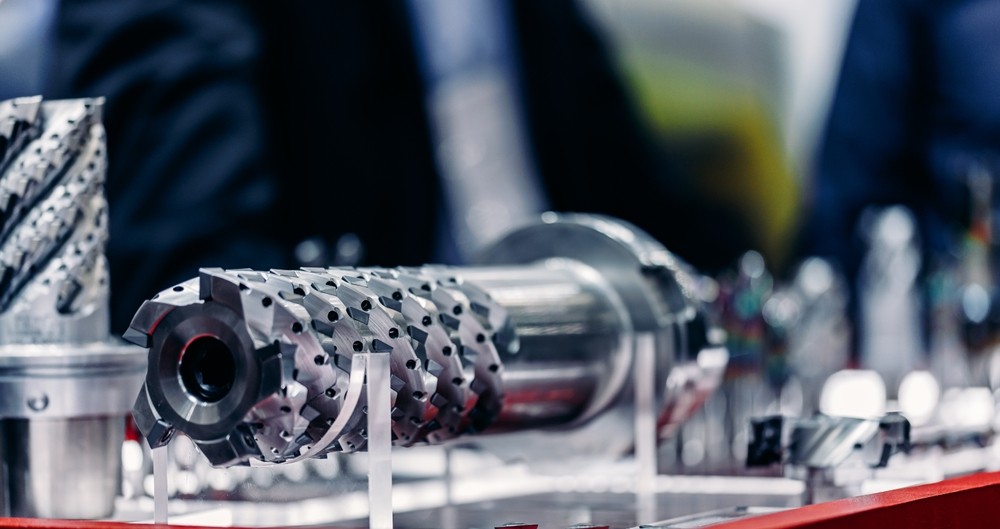
Imagine a key piece of equipment on your production line breaking down without warning. With the loss of one machine, your entire operation grinds to a halt. Every minute of downtime translates to lost production, unhappy customers, and a significant financial dent.
This scenario doesn’t have to be a production nightmare. By strategically managing your spare parts inventory, you can minimize downtime and keep your manufacturing targets in reach — even when critical equipment breaks down.
Building a strategic spare parts inventory
The first step to mitigating downtime is building a well-stocked inventory, prioritizing the parts crucial for keeping equipment running. Here’s where the ABC classification system comes in. This method categorizes spare parts based on their impact on production.
- A items: These are your critical parts. A single failure can bring your entire operation to a standstill. Think essential machine components or parts with long lead times.
- B items: These are important parts, but their failure might simply cause delays or require production adjustments. Examples include frequently replaced filters or specific fasteners.
- C items: These are less critical parts, often with lower costs and shorter lead times. Screws, nuts, and general maintenance supplies might fall under this category.
By classifying your spare parts using the ABC system, you can focus your resources on maintaining sufficient stock of A items, followed by B items. C items can be kept at lower levels with more frequent reordering. Don’t underestimate the power of forecasting — analyze historical usage data to predict future needs for frequently replaced parts.
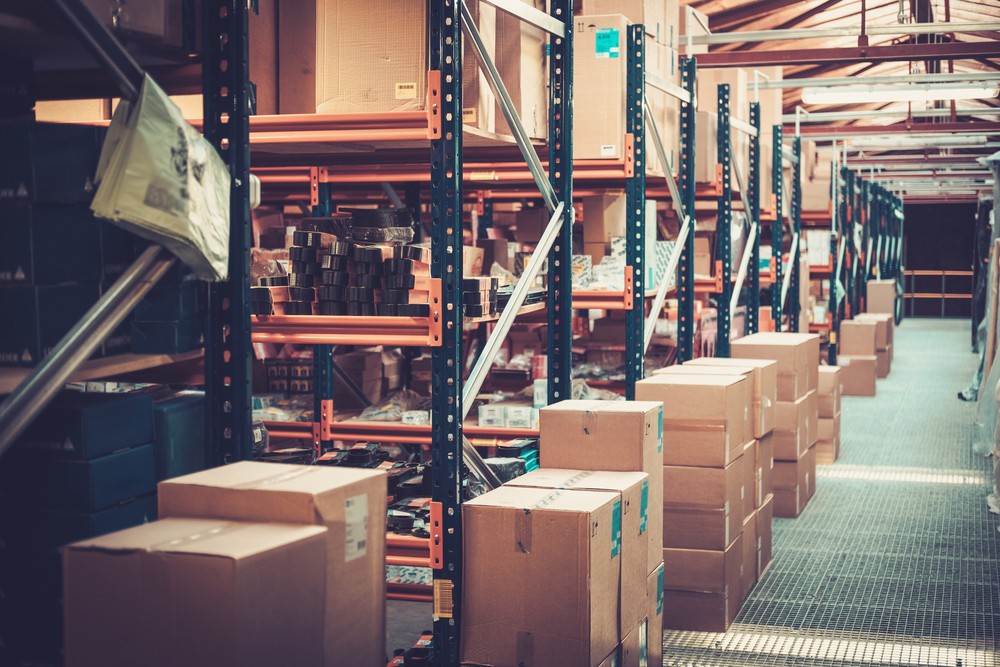
Managing spare parts
Keeping a well-stocked inventory is only half the battle. Here are some best practices for effective spare parts management:
- Minimize stock-outs. The key to preventing downtime is having the right part available when it’s needed. Set minimum reorder points, which represent the inventory level at which you need to place a new order. This ensures you don’t run out of critical parts before a new shipment arrives. Factor in lead times when setting reorder points.
- Leverage technology. Consider implementing a computerized maintenance management system (CMMS). These software solutions streamline inventory control by providing real-time data on stock levels, reorder points, and maintenance history. A CMMS can automate reordering processes and provide vital data for further optimizing your spare parts management.
- Implement cycle counting. Physical inventory checks are crucial for maintaining data accuracy. Regular cycle counting — which involves checking smaller portions of your inventory at regular intervals — helps identify discrepancies and ensures your CMMS reflects accurate stock levels.
Accessing spare parts
With your inventory optimized, your next priority should be to ensure spare parts are readily available when needed.
- Storage and retrieval: A well-organized storage system is key. Clearly defined storage locations with proper labeling make it easy for maintenance personnel to locate the parts they need quickly. Consider implementing shelving systems or bins to categorize and organize your spare parts efficiently.
- Clear labeling and identification: Ensure all spare parts are clearly labeled with part numbers, descriptions, and any relevant information for easy identification and retrieval.
- Personnel training: Train your maintenance personnel on spare parts identification, proper inventory procedures, and using your CMMS (if applicable). This empowers them to quickly locate parts, initiate reorders when necessary, and maintain accurate inventory data.
Make spare parts a priority
By managing spare parts strategically, you can significantly reduce downtime, improve overall production efficiency, and achieve substantial cost savings. The key lies in prioritizing critical parts, leveraging technology, and streamlining inventory accessibility.