Make Materials Handling a Focus of Your Factory’s Best Practices
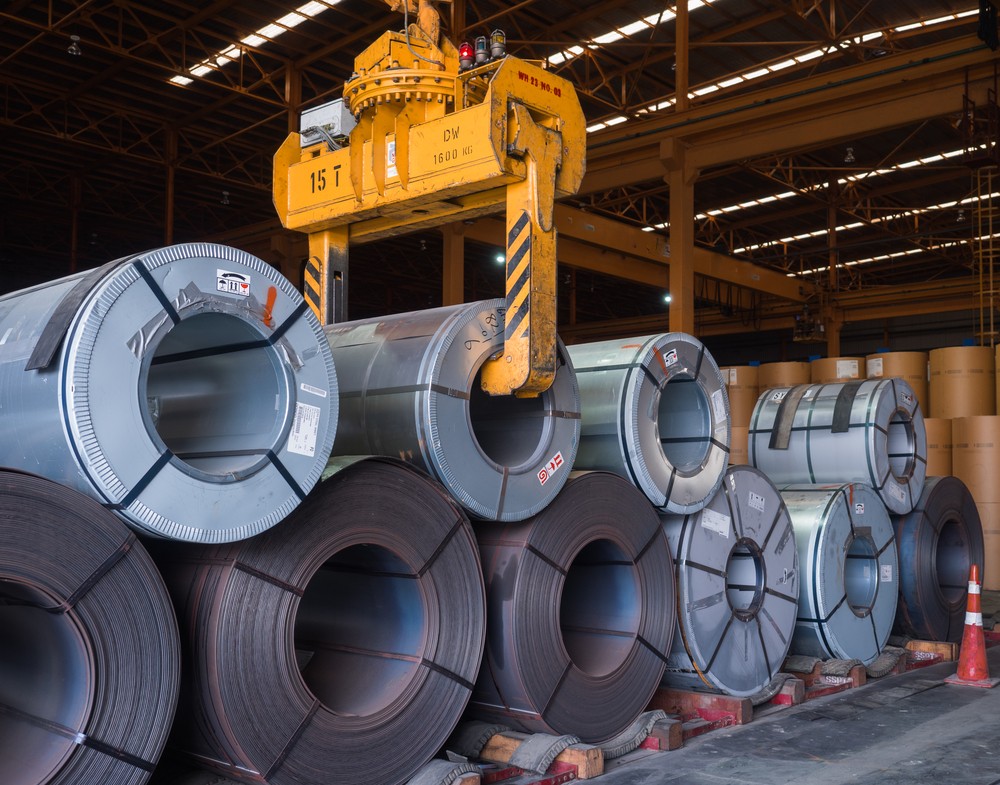
The term “materials handling” is broadly defined in factories. It’s as simple as moving a pallet of product from one place to another, and as complex as interacting with environmentally controlled substances using extreme caution. In any case, materials handling demands one thing above all else — care. Having a rigid training program and emphasis on best practices for materials handling is the key to avoiding the many problems arising from accidents and material mishaps.
Instill a culture of safety
There’s no margin of error when it comes to materials handling. Any accident, no matter how minor, results in a loss. Loss of product and revenue. Loss of employee wellbeing. In the worst case, loss of life. Materials handling demands excellence, and manufacturers need to set the tone by developing best practices.
Outline the risks and explain the dangers of materials handling throughout your factory. Then, provide employees with everything they need to avoid these problems. Back it with standards for accountability and the tone for a safety-conscious culture is set.
Developing best practices
In developing best practices, consider standards in your workplace. Driving a forklift is a lot different from moving controlled substances by hand, but the standards shouldn’t vary all that much. What will vary are the stipulations for each job. A forklift license versus hazardous materials handling certification, for example. The easiest way to develop best practices for materials handling is to consider it in three stages:
- Prequalification — dictates who handles materials and what the expectations are
- Handling standards — determine the process for how specific materials are handled
- Emergency standards — account for accidents and problems
Within the context of how your employees handle materials, consider what’s necessary to keep them safe and to protect factory operations at large.
Factors to consider
Every job is different. How employees handle materials and what they’re handling changes, which means providing them with the necessary resources to do the job right. When developing best practice frameworks, consider the following:
- What kinds of equipment do employees need to safely handle materials?
- Are there any ergonomic risk factors to consider?
- What kind of training do employees need? Do you provide that training?
- Is there documentation available, such as SOPs or a handbook?
- Is there a process for making materials handling safer?
Best practices are the standards your employees will ultimately be held against when doing their jobs. Accounting for all the above variables and more ensures they’re able to meet those expectations.
Stay safe, keep it simple
Too many people see best practices as the lowest benchmark for standards ― the minimum requirement. Materials handling demands the highest standards for safety. Keep your best practices simple, but don’t compromise on their rigidity. These are the standards that’ll help prevent injury, loss of revenue, and other negatives. They’re deserving of a high standard.
Evaluate your materials handling processes today. If there are accidents and loss, address them. If the processes are sound, consider how they could be distinguished or made better. Keep safety at the forefront of these conversations and make materials handling the top priority for your process improvements.