Automation and the Manufacturing Job Market Part 1: Reasons Behind the Skills Shortage
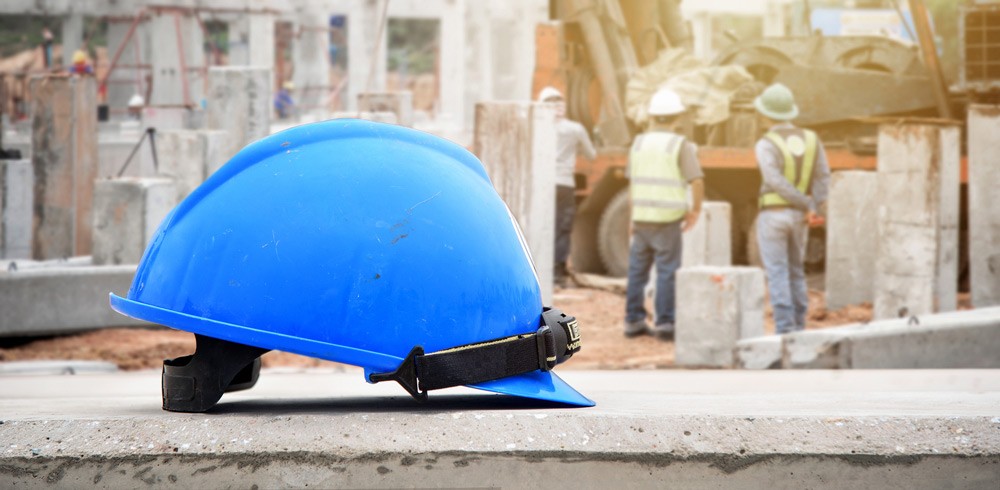
American manufacturing has declined in the past 30 years, but a resurgence is occurring. Industry insiders partly attribute the increase in manufacturing output to the introduction of more industrial robots and automation. Automation mitigates problems like worker shortages, allows for easier shifts in production levels, and offers numerous other benefits that increase productivity and profitability.
In a December 2017 series, we explored three steps manufacturers should take when transitioning to smart manufacturing. In this new three-part series, we take a closer look at how taking those steps toward automation can help manufacturers bridge the skills gap today and in the future. But to understand the direction in which the smart manufacturing industry is headed, it’s important to know how it arrived at its current state.
Manufacturing employment has fallen from approximately 17.5 million members of the U.S. workforce in 1987 to around 12.4 million in 2017. However, manufacturers are still having trouble filling the reduced number of positions available. Several factors are contributing to this nationwide shortage.
- The workforce is aging — and retiring. In 2016, over 50% of the manufacturing workforce was older than 45, and over half of those members were 55-plus. These workers are getting close to retirement, and not enough younger workers are interested in filling the vacated positions.
- Drug use has increased. The opioid epidemic has also affected the eligible employees’ availability to fill open jobs. Regina Mitchell, co-owner of an Ohio manufacturing company, says at least four out of 10 applicants can’t pass a drug test. Drug use continues to rise across the U.S. and, according to a Quest Diagnostics study, 4.2% of American workers tested positive for illegal drug use in 2016.
- Skills are in demand. The face of manufacturing today requires workers who have adaptive skills, such as critical thinking, advanced problem-solving abilities, reading and writing proficiency, as well as the competence to make good decisions quickly. Modern trade school systems and manufacturing training programs are typically lacking in adaptive skill education, and, in turn, this skills shortage hampers manufacturers’ abilities to fill available positions.
However, automation could help reduce the number of unfilled openings. In part two of this series, we’ll look further into how automation could mitigate the worker shortage.