Is Your Compressed Air System Ready for Summer?
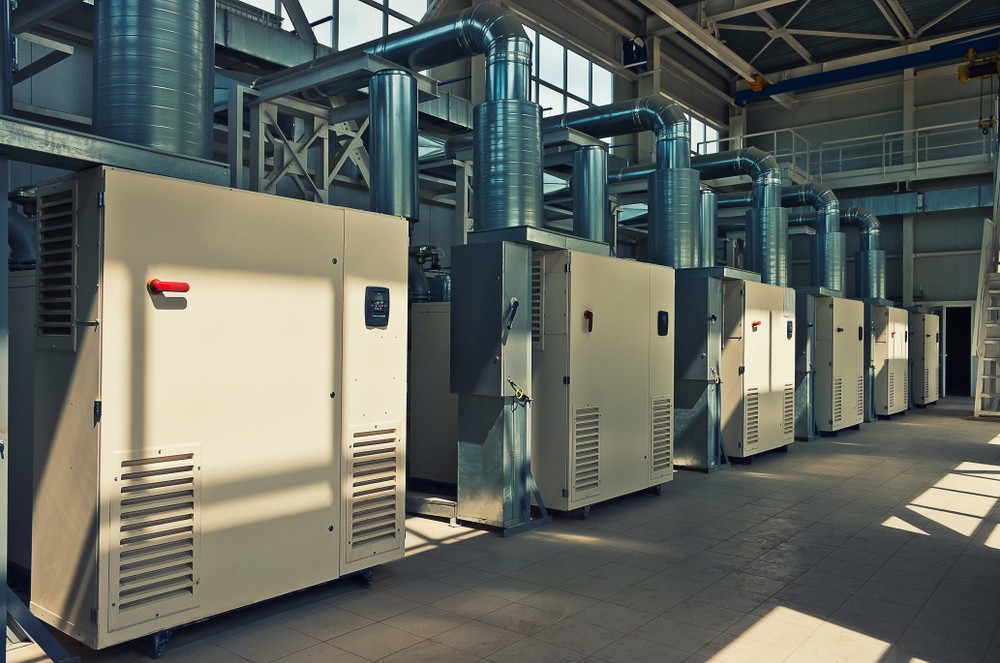
With summer just around the corner, it’s time to start getting your compressed air system prepared to handle the heat and humidity. Doing so helps ensure your system functions at its best and allows you to avoid delays and downtime from industrial equipment breakdowns and unscheduled maintenance or repair.
Keep up with routine maintenance throughout the year, and take the extra time this spring to thoroughly inspect, clean, and make necessary repairs to your compressed air systems.
Basic cleaning practices for compressed air systems
Using general cleaning practices will help keep your compressed air systems working efficiently all summer. Start cleaning the systems themselves by routinely dusting surfaces, removing debris buildup from air intakes, and cleaning connectors and condensation drain traps. It’s also essential to regularly change filters and check lubrication levels.
Keep the room housing your compressed air systems dust- and debris-free with routine vacuuming and dusting. To help prevent overheating, remove anything impeding the compressor’s airflow. Check for oil leaks underneath the compressor, and keep a close eye on ventilation filters.
Monitor fluid levels
During the summer, manufacturers should monitor compressor fluid levels daily. Add fluids whenever necessary and routinely check for leaks. To prevent overfilling, never add fluid to a cold sump tank, and because it’s extremely dangerous to open a vessel under pressure, always follow proper safety procedures when performing maintenance.
Issues with fluid viscosity and pH levels could also cause major problems for heavy machinery. If you suspect a problem, invest in a fluid testing program. Testing small samples of fluid will determine if there are any issues, including the presence of contaminants.
Monitor temperature levels
Because air compressors produce a lot of heat, it’s important to watch for overheating. Overheating will quickly cause malfunctions and eventually, the failure of critical components.
Temperature stabilization is critical for preventing overheating. To stabilize the temperature of a water-cooled air compressor, technicians must check fluid levels and clean all strainer screens. Air-cooled compressors require routine cleaning for temperature stabilization. With both types, it’s essential to routinely check for fluid leaks and system obstructions.
Learn from your technician
Following best practices can help prolong the life of your compressed air system, but it’s also essential to build a good relationship with your compressed air system technician. A good technician will often offer pointers on proper maintenance and cleaning techniques.
Keep your technician informed about any issues you encounter with your compressed air systems, so they can take care of small problems before they get out of control. Observe closely and ask questions to understand your compressed air system, keep it well maintained, and ensure it’s ready to handle the rigors of summertime operation.