Hyperautomation Is Bringing Scale to Industry 4.0
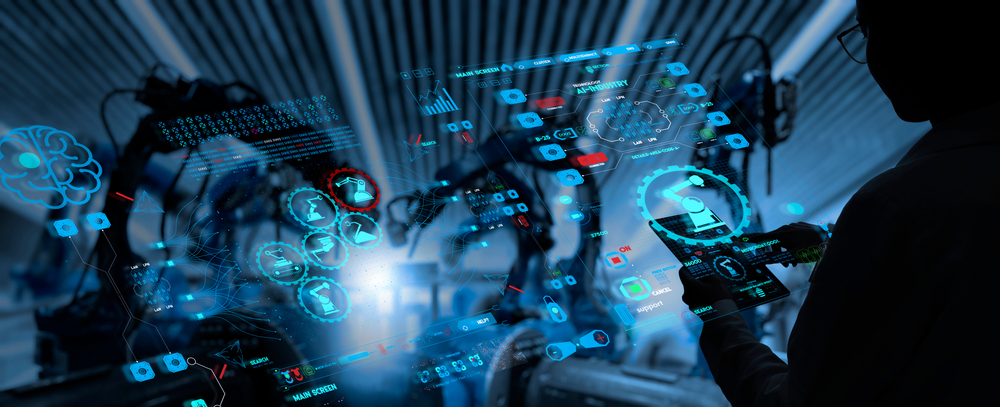
Automation is a key driver of progress in the new era of manufacturing. Reliance on technologies like computer numerical control (CNC) machining and programmable robotics has paved the way to more opportunities for efficiency and productivity. That said, automation has its limits. Now, through a concept called hyperautomation, manufacturing is pushing those limits to expand the possibilities for synergy across the factory. It’s a philosophy that’s quickly bringing scale to Industry 4.0 environments.
What is hyperautomation?
In the realm of manufacturing technology, hyperautomation is a step beyond what we think of as traditional automation. That is, hyperautomation doesn’t just focus on the automation of a single task or process: It encompasses automations that span the entire organization. It’s not just about automating production lines or inventorying processes; it’s about connecting them to automate as much of the factory as possible.
Hyperautomation within the factory
Hyperautomation is closely tied to the concept of a dark factory — a fully automated factory that requires no physical human presence. Although we’re not quite there yet, technologies like 5G, artificial intelligence (AI), and machine learning are inching us closer. The more a factory can do by itself, the less reliant it is on manual inputs.
Many manufacturers are already dabbling in hyperautomation, in preparation for Industry 4.0 at scale. Schneider Electric, for instance, automates the process of creating, labeling, documenting, and organizing switchboards across residential, commercial, and industrial business lines. As a result, human interaction is eliminated from the process, save for data input and the physical installation of the finished product.
There’s promise for hyperautomation when it comes to maintenance and reliability. For example, Industrial Internet of Things (IIoT) sensors can trigger maintenance ticketing, inventory querying, parts ordering, documentation, and more, eliminating manual labor from maintenance, repair, and operations (MRO), aside from the physical administration of service to equipment.
Scaling into Industry 4.0
Hyperautomation encourages manufacturers to think at scale, which is proving to be a significant driver in adoption of Industry 4.0 technologies. Complex automations are only possible among digitally interconnected systems. Thus, factory operators have plenty of reason to invest in the IIoT, enterprise asset management (EAM) software, digital twins, and more. In fact, industry analysts expect the market for hyperautomation technologies to reach $596 billion in 2022 — up nearly 24% from $482 billion in 2020.
As manufacturers build out their digital infrastructures and create automation at scale, the process is paving the way for exciting new opportunities. From the ability to fully automate material ordering based on production line output in a dynamic environment, to end-to-end MRO automations that enable proactive and preventive strategies, it all comes back to hyperautomation.