How To Measure Overall Equipment Effectiveness (OEE)
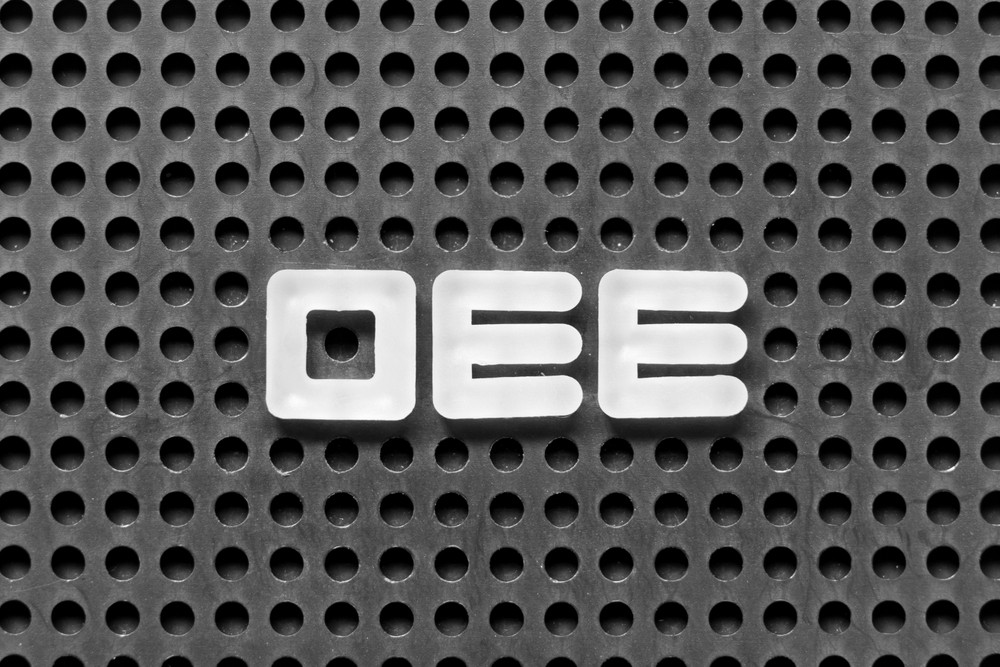
For manufacturers, every second of downtime and every imperfect product costs valuable resources. They rely on overall equipment effectiveness (OEE) to help mitigate unpredictable problems: a powerful metric for examining equipment performance to reveal opportunities for improvement. Measuring OEE empowers manufacturers to optimize operations, boost production, and gain a significant edge in the market.
Three pillars of OEE
OEE is a composite score reflecting three crucial aspects of equipment performance:
- Availability represents the percentage of time your equipment is running compared to its planned production time. Downtime due to breakdowns, setups, or other factors detracts from this score.
- Performance reflects how efficiently your equipment operates while running. Slow cycles, minor stoppages, and reduced speed contribute to performance losses.
- Quality measures the percentage of acceptable products compared to the total production output. Defects, rework, and scrap negatively impact this crucial pillar.
The measurable effectiveness of each pillar can be quantified with these formulas:
- Availability: Run Time / Planned Production Time
- Performance: (Ideal Cycle Time x Total Count) / Run Time
- Quality: Good Count / Total Count
Overall equipment effectiveness can be determined by multiplying the effectiveness of all three pillars: OEE = Availability x Performance x Quality. Most operations strive for scores between 60% and 85%, continuously seeking to improve.
Building an OEE measurement system
Accurately measuring OEE requires consistent, reliable data. Manual data entry, while feasible for small setups, can be prone to errors and inconsistencies. Consider these alternatives:
- Supervisory control and data acquisition (SCADA) systems: Many existing plantwide systems can capture relevant production data, offering a more automated approach.
- Dedicated OEE software: These specialized tools provide comprehensive data collection, analysis, and reporting, often integrated with existing systems.
Setting realistic targets for each OEE pillar is crucial. Start by benchmarking against industry standards or similar equipment within your plant. Gradually raise the bar as you identify and address improvement opportunities.
Transforming OEE into actionable insights
The true power of OEE lies in its ability to pinpoint areas for improvement. By analyzing data trends and identifying bottlenecks, manufacturers can:
- Analyze breakdown patterns and implement preventive maintenance strategies.
- Identify and address slow cycles or inefficiencies in the production process.
- Implement quality control measures and improve process consistency.
Many of the world’s largest producers use OEE data to routinely streamline and improve operations. OEE is closely tied to Lean Six Sigma initiatives, as well as individual aspects of manufacturing excellence such as total productive maintenance (TPM).
Ultimately, OEE data serves as a marker for incremental improvements across the manufacturing floor. Working backwards from OEE to its variable components, and the factors influencing those variables, manufacturers can improve availability, performance, and quality and dramatically improve OEE for manufacturing excellence.
Make OEE a central standard
Measuring OEE means unlocking the true potential of equipment. The goal of leveraging OEE data is to optimize efficiency, elevate productivity, and gain a competitive advantage in the market. Achieving these benefits requires more than just collecting data; it requires a steadfast commitment to data-driven decision-making and continuous improvement efforts across the organization. By embracing OEE as a core component of their operations, manufacturers can drive sustainable improvements and position themselves for long-term success.