How To Conduct an Equipment Criticality Assessment
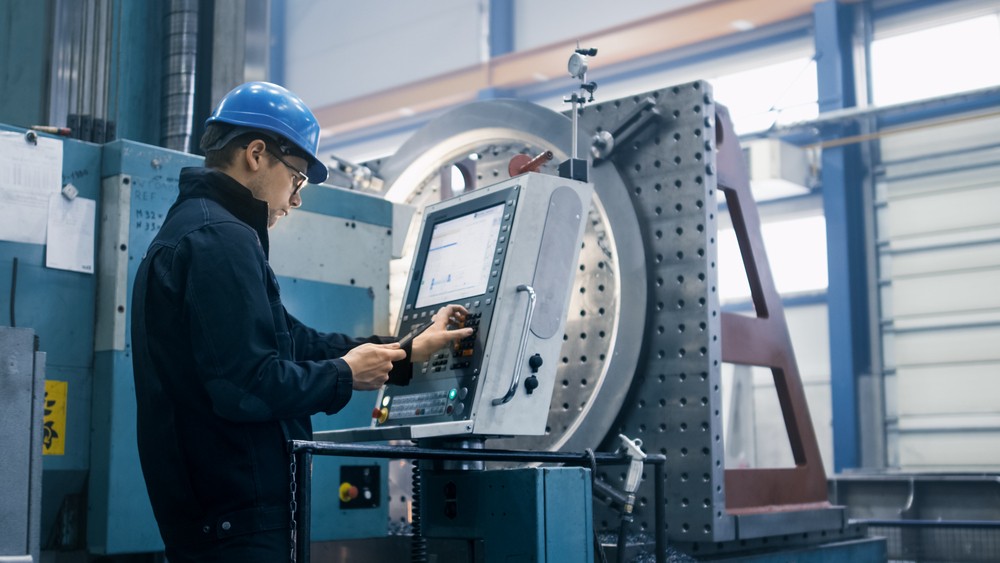
Maintaining optimal equipment performance is crucial for any manufacturer, and a key tool in achieving this is an equipment criticality assessment. This process helps prioritize maintenance efforts and resources by systematically evaluating the potential impact of equipment failures.
By understanding the criticality of assets, producers can make informed decisions about maintenance strategies, spare parts inventory, and resource allocation — ultimately leading to improved efficiency, reduced costs, and enhanced safety.
Here’s a step-by-step guide for how to conduct an equipment criticality assessment and what to keep in mind as you assess the service needs of different production assets.
1. Define objectives and assemble a team
Clearly define the goals of your assessment, such as prioritizing maintenance tasks or optimizing your spare parts inventory. Form a cross-functional team with representatives from operations, maintenance, engineering, and other relevant departments. Each member brings valuable insights and perspectives to the process.
2. Identify equipment and establish context
Create a comprehensive list of all equipment within the scope of the assessment. Define the operational context for each equipment unit, including its function, role in the process, and potential consequences of failure. Understanding the bigger picture helps assess the true impact of potential issues.
3. Develop a criticality assessment matrix
Choose a suitable matrix format, such as a three-by-three or five-by-five grid. Each axis represents a criticality factor, typically:
- Severity: Impact of equipment failure on various outcomes like safety, production, environment, and cost
- Frequency: Likelihood of equipment failure based on historical data, reliability analysis, and expert judgment
Assign scoring or weighting systems for each factor in the matrix. This helps quantify the relative importance of each factor in determining overall criticality.
4. Gather and analyze data
Collect relevant data for each asset, including maintenance records, failure history, manufacturer specifications, operational logs, and input from subject matter experts. Analyze the data to assess the severity and frequency of potential failures for each equipment unit. This forms the basis for assigning scores within the matrix.
5. Rank and categorize equipment
Use the assessment matrix and assigned scores to rank each equipment unit based on its overall criticality. Categorize equipment into different levels (e.g., critical, high, medium, low) based on their ranking. This helps prioritize resources and develop targeted maintenance strategies.
6. Develop and implement maintenance strategies
Based on the criticality ranking, develop tailored maintenance strategies for each equipment category. This might involve:
- Increasing the frequency of preventive maintenance for critical equipment to prevent failures
- Implementing condition-based monitoring for high-risk assets to identify issues early on
- Optimizing spare parts inventory by focusing on critical equipment and components
7. Document, review, and update
Document the entire assessment process, including methodology, data sources, and results. This ensures transparency and facilitates future reviews. Regularly review and update the assessment as operational conditions, equipment performance, and organizational priorities evolve. The assessment should be a living document, reflecting the current state of your equipment and operations.
Ready to perform your next criticality assessment?
Conducting an equipment criticality assessment is a proactive approach to optimizing maintenance efforts — and improving overall reliability metrics. By following these steps and continuously refining the process, maintenance teams will gain valuable insights into equipment for a more exceptional maintenance standard.