How Often Should Employees Undergo Training?
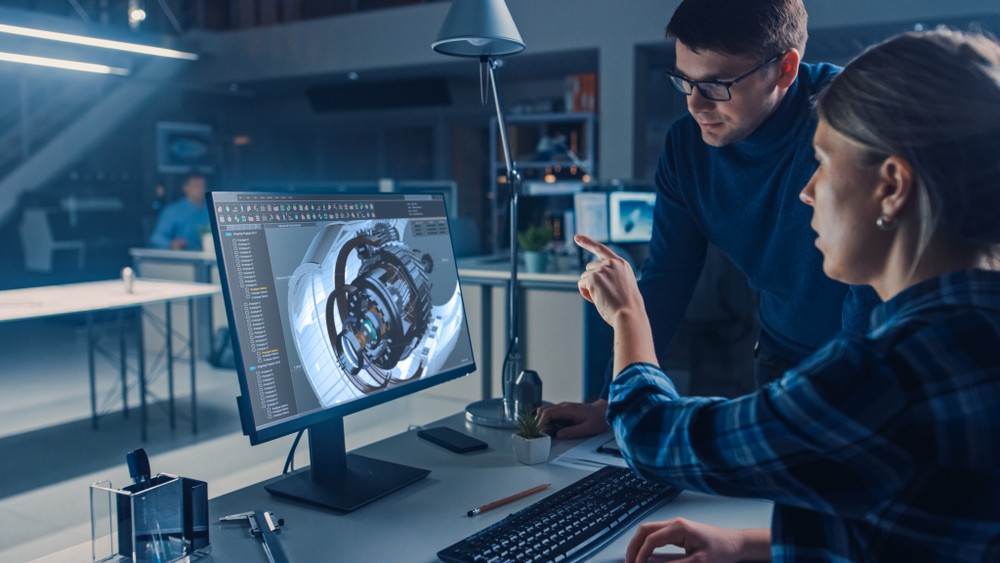
Most factory employees go through a period of on-the-job training to get them acclimated with the standards and expectations of the work they’ll be doing. After that, training opportunities can be a toss-up, depending on the industry or specific factory they work in. Some manufacturers have annual training tracks, as a reinvestment in their workforce. Others offer training opportunities passively and to select employees. It begs the question: how often should manufacturing employees undergo training?
Training intervals, understood
How often you train depends on the subject of that training. There’s no need to train and re-train an employee on their core job duties weekly; however, you might have weekly safety briefs as a form of ongoing training. As a general rule, training should take place when it’s needed based on the nature of the training. Common intervals include:
- Daily: General skills upkeep and improvement. Jake sees Tom struggling on the job and offers a quick lesson in how to approach a certain task.
- Weekly: Briefs and updates for routine and generalized topics. Mallory gives a seminar every Friday on different, applicable OSHA (Occupational Safety and Health Administration) standards.
- Monthly: Certain skills and topics that require ongoing refinement. Yousef re-trains on standard operating procedures and lockout/tagout protocols each month.
- Quarterly: Job-specific skills and standards. Leon completes quarterly modules from a SaaS (Software-as-a-Service) provider to understand the IIoT (Industrial Internet of Things) system he manages.
- Annually: Specialized training and recertification. Helen goes to an OEM (Original Equipment Manufacturer) for machine-specific equipment repair training each year.
Again, these specific intervals are mere guidelines for when training may occur in a manufacturing environment. Training can and should take place when it’s needed. More important, training and re-training should take place in a proactive capacity, not a reactive one. Train to prepare your workforce, not to remediate issues that have begun to creep into operations.
The value of making training a priority
Knowledge is power. The more your employees know about the concept and execution of the tasks they’re expected to perform, the better they’ll be able to perform those duties. More important, they’ll be better equipped to perform above and beyond minimum expectations, paving the way for a higher caliber of work and a more diverse scope of capabilities.
Ongoing training also empowers employees. Given opportunities, employees will distinguish themselves by acquiring new skills and pursuing a wider range of opportunities within the company. Your floor worker could position themselves for a role in management, given the right education. Likewise, your mechanical technician may choose to become OEM-certified for repairs given the ability to achieve that certification.
These benefits feed back into the company in many ways. They foster a culture of continued education and innovation. Employee loyalty and satisfaction rise. The quality of value streams improves alongside the quality of products. Education is the lynchpin for uplifting a factory.
- 60% of employees who receive on-the-job training retain their position past one year.
- 70% of employees cite ongoing training as a decision to retain their position.
- 87% of employees cite education opportunities as vital to their careers.
- Companies engaging employees with education outperform competitors by 202%.
- Manufacturing skills average two years before they become antiquated.
Create an employee training program
The answer to the question, “how often should you train employees” is a simple one: continuously. Make training a cornerstone of your factory operations and seize every opportunity to provide training and educational opportunities to employees. Start with an employee training program and grow that program into an essential part of your operations. The benefits will quickly become apparent.