How Are You Addressing Operational Risks in Your Manufacturing Facilities?
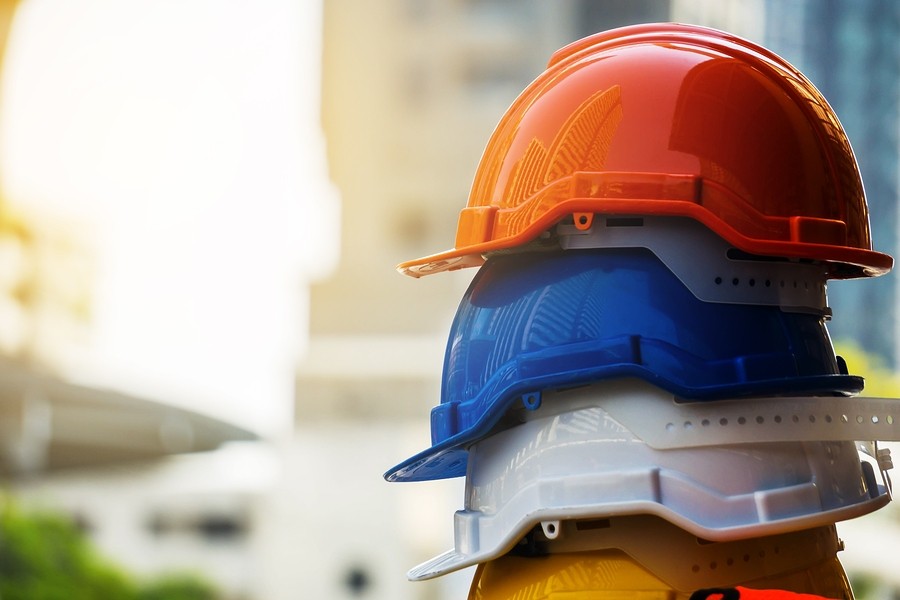
Worker safety has always been a clearly defined focal point of factory operations. But as industry evolves, is the concept of risk mitigation and worker safety evolving with it? As we enter a new phase of industry, there are new concerns about how factories are identifying and mitigating risk. Manufacturers need to take a close look at how they’re addressing safety risks before getting too involved in changing their operative practices.
A look at what “risk” really means
Every factory has safety procedures and protocols in place, designed to reduce risk. But risk itself tends to be ambiguous. For some, it’s a matter of frequency. The time between incidents is an indicator of risk tolerance. For others, it’s about severity. The nature of an incident has a direct bearing on the amount of risk involved.
One thing is for certain: How risk is perceived is different than how it’s managed. A recent study by DuPont Sustainable Solutions (DSS) shows some startling data regarding how manufacturers approach and manage risk:
- As many as 78% of survey participants say that low incident rates do not correlate to reduced risk. But as many as two-thirds of those respondents focus on lowering incident frequency as opposed to understanding the other catalysts involved in mitigating risk.
- Roughly 25% of survey participants felt like front-line personnel were not equipped to properly cut risk. Fifty-five percent of those surveyed felt like upper management were not cognizant of operational risks facing the company.
Survey respondents identified everything from utilizing data to developing processes as ways to minimize risk. Despite these probable solutions, it’s clear that identifying operational risks remains a priority for manufacturers.
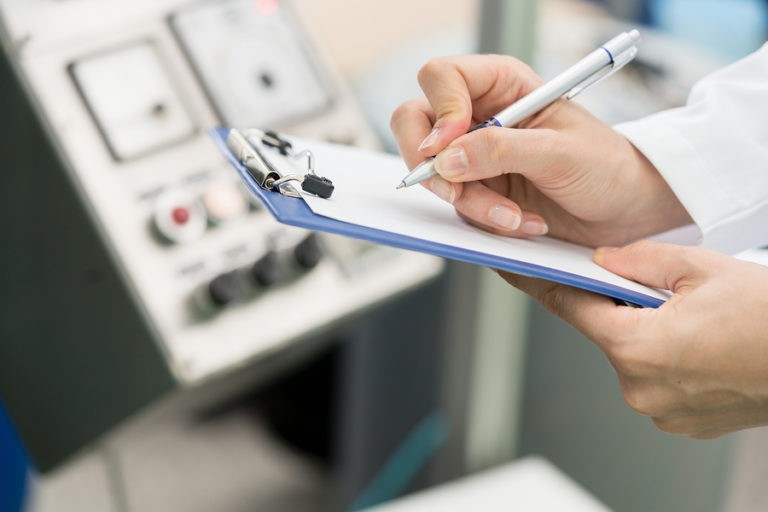
Side view close-up of the hands of a female engineer or inspector, ready for writing a technical report about the manufacturing process in a contemporary factory
Addressing risk at your facilities
There are many ways to approach identifying risk. Evaluating safety and performance data, having frequent safety meetings, and even taking a Gemba walk through your facilities can easily shine a light on unnecessary operational risks.
Once identified, reducing or eliminating risk becomes a case-by-case situation. Evaluate the nature of risk and the variables involved to create a possible solution that mitigates both frequency and intensity of incidents. Some options include:
- Improving processes, specifically targeting unmitigated risk.
- Training informed personnel, capable of identifying risk and acting to mitigate it.
- Rewriting Standard Operating Procedures (SOPs) and best practices to reduce risk.
- Scheduling audits and setting expectations focused on risk minimization.
Even beyond these individual steps for reducing risk, creating a culture of safety will serve to engrain a safety-first, low-risk approach to operations within your facilities.
A new type of risk
The already-muddled definition of risk is changing with Industry 4.0. In the era of worker safety, risk still exists in the form of a sloppy workstation or dangerous repair procedure. Now, it’s also becoming clear in how we’re protecting the industrial internet of things (IIoT).
Cybersecurity is the next big question mark in operational risk. Unsecured, network-enabled devices are already a target for hacking attempts. A compromised piece of technology represents a major threat to worker safety — and without proper understanding of the IIoT, there’s no way to identify this risk, much less mitigate it.
Manufacturers need to educate themselves on cybersecurity risks, as well as other risks becoming apparent in the new age of industry. Like traditional problems, they’re best solved with the right understanding and approach.
Are there gaps in your operations leading to safety concerns? Don’t put your workers in harm’s way to do a job that might be better left to someone more knowledgeable. You can always count on the professionals at Global Electronic Services. Contact us for all your industrial electronic, servo motor, AC and DC motor, hydraulic, and pneumatic needs — and don’t forget to like and follow us on Facebook!