Edge Computing Has Manufacturers Buzzing
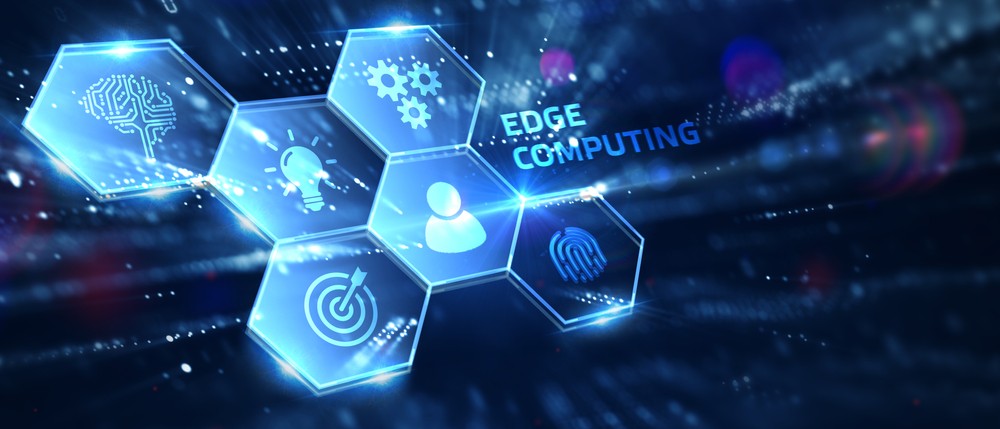
Edge computing is getting a lot of buzz in the industrial sector, but it’s not just another buzzword. For manufacturers, it has the potential to make meaningful change. Much like the cloud revolutionized the business world’s perspective on data, edge computing will enhance the industrial internet of things (IIoT) in inventive and unexpected ways. By keeping data closer to the point of generation — and the point of use — edge computing promises to make next-gen factories smarter, faster, and better equipped for leveraging digital infrastructure.
What is edge computing?
Data is prolific and growing every second. Despite modern technologies, computing power based on centralized data centers can’t keep up. The constant transmission and reception of data to off-site servers and storage causes latency issues and network disruptions. These problems are especially disruptive for manufactures relying on IIoT data for equipment condition monitoring, alerts, and diagnostics. But edge computing is the solution.
Instead of processing data in a data processing warehouse, edge computing captures, processes, stores, and analyzes data near the source — and on the edge of the network. Edge computing provides instant communication between devices and nodes with low latency to make data sharing quicker and more efficient, which is a priority as the IIoT continues to grow.
Edge computing in the manufacturing environment
There’s a great need for edge computing in the manufacturing environment. It’s the solution to increasingly antiquated data handling systems that push data offsite for processing, and it also offers more flexibility for sharing and accessing data onsite — near the IIoT devices relaying it and relying on it. Edge computing facilitates manufacturing data processing in several specific ways, including:
- Condition-based monitoring. Machine failure happens in real time which necessitates a timely, automated response. Sending data offsite for computing isn’t fast enough to support real-time adaptation to condition-based situations. Onsite edge computing offers low latency to assess and respond to condition triggers quickly.
- Predictive maintenance. Manufacturers require data to develop effective predictive maintenance programs. Edge computing allows for quick access to necessary data, data aggregation, and integration into dashboards and systems designed to facilitate smarter predictive maintenance solutions.
- AR/VR and augmentation. Augmented technology requires access to broad swaths of critical data. Retrieving data from offsite storage can create functional delays in augmented reality (AR) and virtual reality (VR) tech. Edge computing helps prevent latency issues to ensure workers can use headsets and other wearables without losing functionality.
- Precision monitoring and control. Safety and fault safeguards are increasingly intelligent systems. Like condition-based monitoring solutions, they need real-time access to data to facilitate triggers and activate features. Without node-level data, these systems can’t monitor precision conditions and execute controls at specific safety thresholds.
Utilizing edge computing allows manufacturers more flexibility in their processes and helps them fully leverage IIoT technology investments.
The power to transform the IIoT
Manufacturers are already seeing impressive results from their implementation of edge computing. According to Lumen, “69% of manufacturers surveyed using edge computing solutions believe they help to better acquire, analyze, and act on critical data.” It’s a clear call to action in favor of bringing critical data processing to the edge of the onsite network — where it’s most useful.
In the same way cloud computing made data more accessible, edge computing can mobilize data like never before. From dynamic automations to enhanced workflows and a vast new digital infrastructure for factories, the future of manufacturing is on the edge. As more manufacturers move to implement edge computing, Industry 4.0 is coming into focus for more producers.