Early Warning Signs of a Faulty Temperature Controller
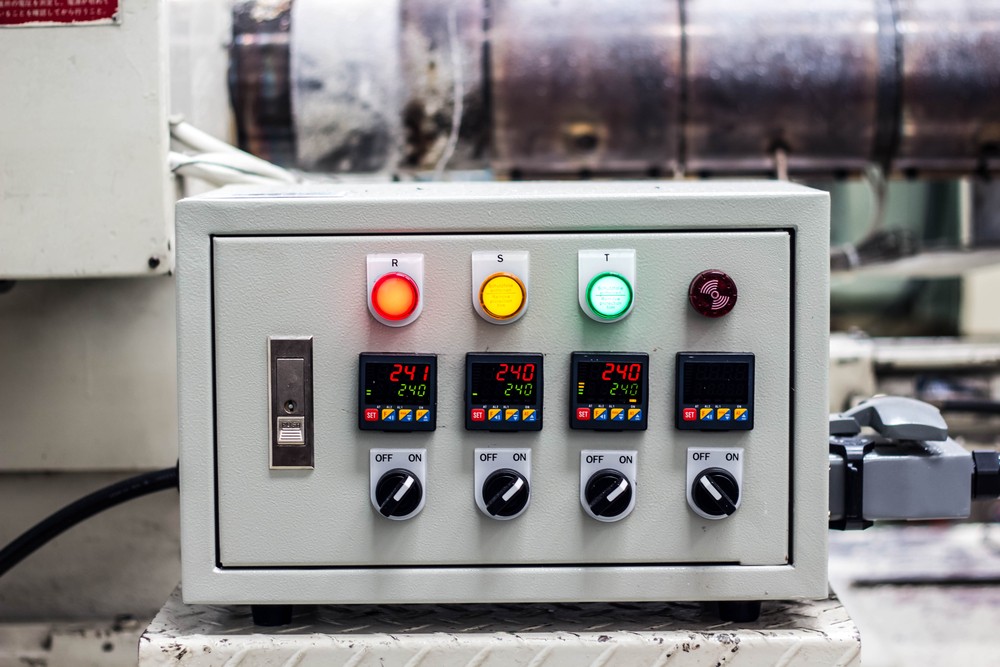
Of the many elements to control within a production environment, temperature is among the most important. Precise temperature control can be the difference between costly inefficiencies and smooth operations.
A faulty temperature controller can be the culprit behind a cascade of issues, leading to product defects, wasted materials, and costly downtime. The good news is that many warning signs can tip you off to a malfunctioning temperature controller before it throws your entire process into disarray.
Signs of trouble with a temperature controller
Is the temperature reading on your equipment moving out of tolerance? Have you noticed temperature spikes or swings? Issues like these are the earliest warning signs that your equipment is faulty or malfunctioning.
- Inaccurate temperature readings: If your controller’s reading consistently diverges from the actual temperature measured with a separate thermometer, or if the displayed temperature bounces around erratically, it’s a strong indication of a problem.
- Difficulty maintaining set point: Is your equipment struggling to reach or stay at the desired temperature? Does it seem to keep cycling on and off without ever achieving the set point? These behaviors suggest the controller might be malfunctioning.
- Unusual equipment behavior: Sometimes the warning signs come from the equipment the controller regulates. Listen for increased noise or vibrations and be wary of any unusual odors emanating from the equipment, which could signal overheating.
Troubleshooting a malfunctioning temperature controller
When you’re faced with temperature control issues in a production environment, it’s essential to have a systematic approach to troubleshooting. Here’s a step-by-step guide to diagnosing and resolving problems with your temperature controller:
- Check external factors: Examine environmental conditions like insulation, drafts, and other factors affecting temperature control.
- Verify sensor accuracy: Calibrate or replace inaccurate sensors and ensure they’re unobstructed and correctly positioned.
- Inspect wiring: Look for faulty wiring or loose connections that could disrupt communication with heating and cooling elements.
- Test control algorithm: Evaluate the controller’s algorithm for correct settings and adjust if needed to maintain set points.
- Monitor system response: Document any deviations from stable temperature levels within the specified range.
- Review error codes: Interpret error codes and alarms to address underlying issues according to the controller’s manual.
- Consider environmental factors: Mitigate ambient temperature fluctuations or humidity levels impacting system performance.
- Consult technical support: Seek assistance if troubleshooting efforts are unsuccessful or complex issues arise.
By following these troubleshooting steps systematically, you can identify the root cause of temperature control issues and implement effective solutions to restore optimal performance in your production environment.
Proactive measures for a healthy production line
Identifying a faulty temperature controller early gives you the opportunity to service it accordingly before issues have a chance to manifest or get worse. Keep these measures in mind as you service and maintain temperature controllers:
- Regular preventative maintenance: Schedule regular inspections and cleaning of your temperature controllers.
- Embrace monitoring systems: Many modern temperature controllers come equipped with data-logging features. Utilize these tools to track temperature trends over time. Consider setting up alerts for significant deviations from set points to catch problems as soon as they arise.
- Staff training: Empower your staff to be your extra set of eyes and ears. Educate them on the warning signs of a faulty controller and emphasize the importance of reporting any observed issues promptly.
If you’re experiencing multiple warning signs or your controller is an older unit with frequent repair needs, replacing it might be the most cost-effective solution. Carefully weigh repair costs against the potential benefits of a new, more reliable controller.
Get ahead of temperature controller issues
Early detection of a faulty temperature controller is an important part of maintaining a smooth, efficient production process. Through preventive maintenance routines, diligent monitoring, and technician awareness, it’s easier to catch problems early and avoid costly disruptions. A little vigilance can go a long way in ensuring temperature-controlled processes stay on track.