Diagnosing and Repairing PLC Module Failures
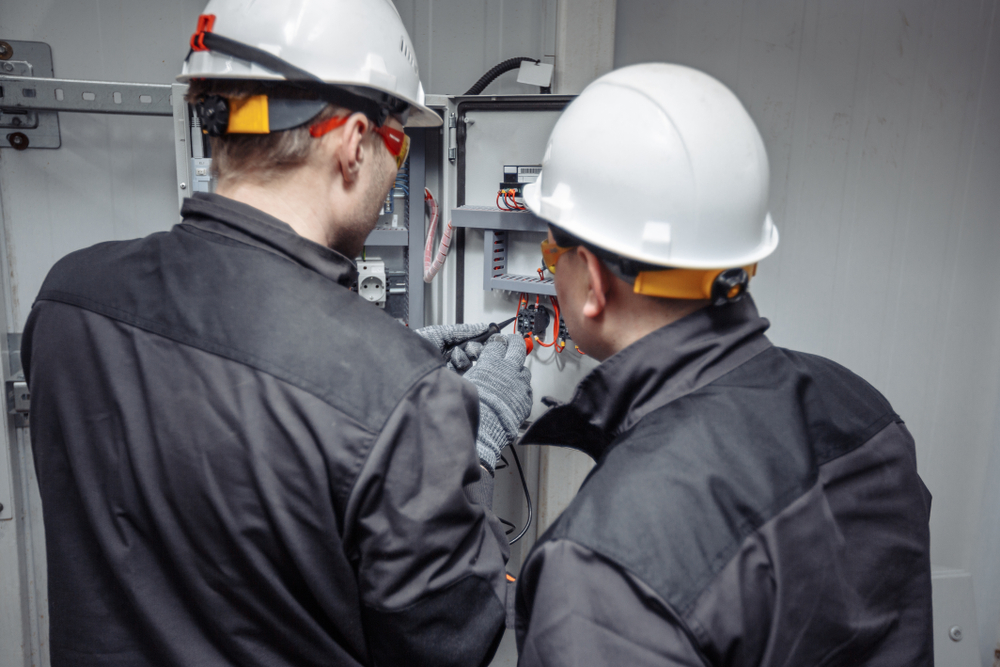
Programmable logic controllers (PLCs) are the brains behind modern manufacturing systems, driving automation to make sure processes run seamlessly. But like any technology, PLC modules are prone to failure over time. When a PLC module starts to fail, it rarely happens without warning. Some of the most common indicators include:
- Unexpected system shutdowns or resets
- Error codes or fault indicators on the PLC display
- Intermittent communication issues between modules
- Unresponsive input/output (I/O) signals
- Fluctuating or inconsistent performance in automation
- Overheating or unusual heat patterns on the module
These symptoms can stem from a range of underlying causes, including hardware degradation, power supply problems, or software glitches. Environmental factors — including excessive dust, humidity, or temperature variations — can also accelerate hardware deterioration. In some cases, failures may manifest intermittently, making them difficult to diagnose without continuous monitoring. The question is: how do you get to the root of the issue?
Pinpointing the root cause of PLC failure
Effective troubleshooting begins with a structured approach. Methodical root cause analysis saves time and reduces the risk of overlooking obvious issues. Start with the basics:
- Power supply checks: Verify that the PLC is receiving consistent voltage within the specified range.
- Inspect physical connections: Loose wires, corroded terminals, or damaged cables are frequent culprits.
- Review error logs: Most modern PLCs maintain diagnostic logs that can reveal where the failure originated.
- Module swapping: If you suspect a faulty module, swap it with a known good one to confirm its function.
- Environmental assessment: Check for environmental factors that might impact module performance.
- Software diagnostics: Run diagnostic tools to detect configuration errors or firmware mismatches.
Should you repair or replace a damaged PLC?
Once the fault is identified, the next step is deciding whether to repair or replace the PLC module. Minor issues, such as a blown fuse or loose connector, can often be fixed quickly. However, more severe damage — like burned-out circuits or repeated faults — usually calls for replacement. It’s also important to verify that replacement modules are compatible with the existing PLC system. Firmware mismatches or outdated configurations can create new problems during installation.
Give your equipment the attention it deserves
Have servo motor issues stemming from poor PLC performance? Contact GES today to schedule service and take advantage of our January special: 10% OFF a single repair or 15% OFF 3+ repairs on servo motor units!
Preventing future failures
Preventive maintenance is the best defense against PLC failures. Regular inspections, firmware updates, and environmental controls (like reducing dust and heat exposure) can extend the lifespan of PLC modules. Training personnel to recognize early warning signs and respond appropriately also plays a significant role in avoiding prolonged downtime.
Investing in predictive maintenance technologies — such as thermal imaging or real-time performance monitoring systems — can provide early insights into potential failures. These tools enable teams to schedule maintenance proactively rather than waiting for visible symptoms to emerge.
Keep PLC integrity top-of-mind
Diagnosing and repairing PLC module failures requires a mix of technical know-how, attention to detail, and a structured troubleshooting approach. With the right practices in place, manufacturers can address issues swiftly and keep operations running efficiently.
Beyond repairs, investing in long-term strategies — like preventive maintenance, ongoing training, and predictive technologies — ensures a resilient automation system. The ability to anticipate problems before they escalate can save you the trouble of defective PLCs and the rippling headaches that can stem from one.