Corrosion Protection Tips
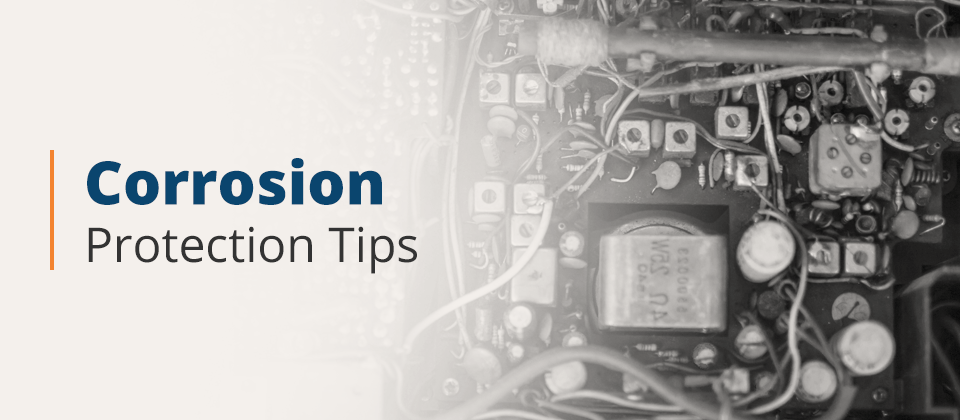
From flickering lights to stalling equipment, electronics that don’t work as they’re supposed to are a big problem. In the workplace, you depend on your equipment working exactly as intended. Any situation where this isn’t the case results in lost time and money for your bottom line. So what causes these types of glitches and errors, and how can you best react to them?
While there could be several potential answers to this question, it’s entirely possible that the problem is corrosion. If your wires and electrical components have corroded, this has the potential to wreak havoc on your electrical system and is certainly capable of ruining your productivity for a day or even longer.
Once the corrosion has set in, there’s little to be done but replace the damaged electrical components. There isn’t much choice there. Where you can take action and assert control over your electrical circuits, however, is in preventing corrosion in the future. Corrosion doesn’t have to cripple your electronics, and there are easy ways to avoid it. To help you do just this, let’s review our top ways to prevent the corrosion of your electronic components and metal surfaces, as well as why it’s so important to do so in the first place.
What Is the Cost of Corrosion?
We all know that corrosion can cause irreparable damage to electrical components. But what are some of the concrete ways this affects you, your employees and your business?
First, it’s helpful to get an understanding of what corrosion is and what it does to your equipment. In addition to the basic corrosion that corrupts exposed metal surfaces, there are two main types of corrosion that you’ll need to worry about with your company’s electronics:
1. Galvanic Corrosion
The natural electrolytes in any liquid work their way into the electronic components, creating unintentional electronic flows that pull the copper off the wire traces in your electronics. Once this copper is pulled off, the intended electrical connection cannot happen, resulting in the eventual failure of the device. In other words, the liquid has broken down the connection between two electrical points so that the electricity can’t flow between them anymore.
2. Denditric Corrosion
This type of corrosion starts the same way. The electrolytes in the liquid disrupt the existing flow of electricity, stripping away the copper oxide that coats the wire traces. Instead of stopping there and simply interrupting the existing connection, however, this problem goes one step further. It forms a new, unintended electrical connection, resulting in all kinds of unplanned activity within your device or machinery. Obviously, this type of corrosion is more complicated.
Just a few of the negative consequences that corrosion such as this may have on your business or production plant include:
- Damage or loss of electronics: As we mentioned earlier, corrosion can utterly devastate your electronics, causing them to weaken, work incorrectly or stop working altogether. Since electronics do not come cheaply, this can often present an enormous financial blow.
- Damage or loss of metal structures: While a significant part of corrosion prevention and control centers around its effect on electronics, it’s important to remember that corrosion can also devastate metal surfaces and structures. Corrosion is capable of entirely covering these surfaces, weakening them and even destroying them.
- Maintenance, repair and replacement costs: Getting damaged equipment back in working order comes with a hefty price tag, as does purchasing new equipment to replace the damaged items. If corrosion is running rampant on your work floor and many items need to be replaced or repaired, these costs will very quickly start to pile up.
- Additional indirect losses: Corrosion opens the door for all kinds of risks. Fires might result from unstable electronics, leaks might spring from unsealed pipes and workers might be hurt as a result, leading to a loss of money through workers’ compensation and paid injury leave. There’s even a potential for lawsuits if injuries become involved. All these consequences could be the result of unchecked corrosion in your facilities.
Protect Your Facility’s Environment
If you’ve experienced repeated problems with corrosion in the past, it should be clear that the problem is not just an odd one-off event. There is likely an underlying problem that must be addressed, or else you’ll risk the corrosion returning again and again. One of the best ways you can practice this type of electronic corrosion prevention is by protecting your facility’s environment. Here are a few concrete ways you can do this:
1. Limit the Humidity
Humidity refers to the amount of water content in the air. If the humidity is high, this means that there is a great deal of water in the air, and vice versa. Since we know that excessive water is what leads to corrosion, it makes sense that high humidity levels would lead to increased counts of corrosion.
Because of this, one of the best things you can do to prevent corrosion is to lower the humidity levels of your facility. This will likely include investing in some high-quality climate control equipment, which can seem like a major expense. This investment, however, will protect your equipment for years to come and prevent you from having to repair or replace your metal and electronic components.
2. Control the Temperature
Climate control equipment is also a great way to ensure that the overall conditions your machinery and electronics need to endure is not overly harsh. Neither extreme heat nor extreme cold is good for your electronics, and while neither will cause corrosion all by themselves, they can aggravate pre-existing conditions.
3. Improve Air Flow
Hot, stifled and recycled air is also a recipe for disaster when it comes to corrosion. Electronics that are kept in a confined space with little breathability and no natural airflow are going to experience negative side effects. For an example on a smaller scale, imagine what might happen if you locked your phone in the car on a sweltering summer day with the sun beating in through the windows. With the high heat combined with the lack of air movement, the phone would likely suffer some severe consequences.
Reduce Exposure to Contaminants
While issues of condition and climate can certainly exacerbate underlying corrosion problems, they aren’t the primary cause of them. A hot environment would not be ideal for electronics, but it wouldn’t cause corrosion all by itself. The primary factor responsible for causing corrosion is foreign elements such as dust, chemicals and other contaminants.
Just a few of the likely culprits that may be latching onto your components and causing corrosion include:
- Ammonia
- Calcium
- Chlorides
- Magnesium
- Potassium
- Sodium
- Sulfate
Unfortunately, for the diligent worker attempting to protect their electronics, these are all elements and chemicals that are present in almost any environment in the world, no matter how much care you take. There’s no way to eliminate your exposure to them entirely.
What’s important to realize, however, is that while all of these elements have the power to corrupt your electronics, this will likely not be aggressive or even extremely problematic without the addition of high humidity. With added moisture, these chemicals will all become much more destructive and begin to eat away at your electronics.
While it’s impossible to eliminate these chemicals from your environment altogether, you can still take reasonable measures to minimize them. Here are just a few of the things you can do:
1. Clean Your Equipment Regularly
There’s no need to let dirt, rust or residue build up on your equipment. Working gently and carefully, clean your electronics thoroughly on a regular basis. Clean off any material that has built up on them and repeat this cleaning frequently.
2. Keep Your Equipment Away From Any Obvious Contaminants
Is there an open stream of fluids somewhere in your facility? Any loose materials that might fly up and attach themselves to nearby objects? A simple precaution you take is to keep your electronics away from these environments. While this doesn’t guarantee that your electronics say safe, it decreases the chances of them coming into careless contact with rogue chemicals.
3. Spot Clean After Contact
Accidents happen sometimes. If there is any incident where your equipment has liquid spilled on it, or it accidentally comes into contact with any material it shouldn’t, clean up as soon as possible. Wipe down the electronic equipment, removing any traces of residue that you can find. You may want to repeat this the following day, to make doubly-sure that you cleaned all traces of the foreign material that remained.
Consider Adding Some Additional Protection
While it’s impossible to eliminate 100 percent of the elements that may attempt to damage your electronics, there is one additional step you can take, and that is to add an extra level of protection and security to your equipment. To best prevent corrosion in your facilities, think about investing in some of the following preventative measures:
1. Impressed Currents
This is an unexpected means of electronic corrosion control, but it’s been proven effective in many scenarios. What this entails is essentially generating a new electrical current of equal size and strength to the existing current, but flowing in the opposite direction. This is a very delicate solution, and should only be attempted by those with extensive electrical knowledge, as the incorrect implementation of this solution could actually end up leading to increased levels of corrosion.
2. Sacrificial Metals
If you place steel in contact with another metal, the secondary metal protects the steel from rust and corrosion. Steel on its own will almost always corrode, but the presence of another metal protects the steel. Instead of attacking the steel, the corrosion attacks the other metal instead. You can harness this tendency and use it to your advantage by lining your steel surfaces with other materials such as zinc or magnesium.
You can frequently see this principle at play on the hulls of ships. These hulls may appear rusted from the outside, but in most cases, it’s only the zinc or magnesium hull that’s being corroded. The steel underneath remains safe. Additionally, some engineers take advantage of this idea by painting steel surfaces in a zinc-based coat, which protects the steel.
3. Primers
Primers are a great way to protect any surface from the corrosion that would otherwise threaten to weaken and damage it. A primer creates a buffer layer between the surface and anything else that will go on top. In this case, that “anything else” is corrosion.
Primer acts as a barrier between your metal surfaces and corrosion. Instead of collecting directly on the metal, the corrosion is unable to get past the primer, and thus, your surfaces are protected. A primer does this specific work in three distinct ways:
- A primer coating helps to slow the rate at which oxygen and moisture from the surrounding environment latch onto the metal surface. Much of the moisture from the air is absorbed by the primer, preventing it from coming into contact with the metal at all. This doesn’t stop corrosion, but it does slow it down.
- The coating also helps slow the rate at which corrosive elements diffuse through the primer and encounter the metal surface. Again, this does not eliminate corrosion, but it helps to slow it.
- Many high-quality primers that are created for just this purpose also contain anti-corrosive properties that actually change the properties of the metal it’s protecting. In other words, the coating itself can cause the metal to develop a high level of electrical resistance, which makes it less susceptible to corrosion.
There are many different types of primers and coatings available, and you’ll need to choose for yourself which is best suited for your needs. A few of the things to keep in mind as you make this decision include:
- Aesthetic: How important is it to you what the final coating looks like? Some primers offer more aesthetic appeal than others.
- Price: What does your budget look like? There’s a primer for everyone at a variety of different price points.
- Environmental concerns: Check with your local and state regulations as to what is allowed in your location. You may find that some coatings are banned, or may only be applied with the use of certain additional precautions.
- Type: Protective primers aren’t a one size fits all solution. There are many different types, all with slightly different approaches to solving the corrosion problem. Powder paints and chromate conversion coatings, for example, are just two of the styles you may want to choose from.
Take Action Against Corrosion Today
While corrosion might seem like just an ugly stain that creeps onto your metal surfaces or into your electronics, it’s much more than that. It has the power to weaken or destroy structures and damage electronics so severely that they become unusable. If you allow corrosion to spread unchecked throughout your facilities, there’s no telling the amount of damage it could cause.
To learn more about corrosion protection, reach out to us today at Global Electronic Services. We’d be happy to answer any additional questions you may have, and brainstorm about ways you can give your electronics the protection they need to keep working for you.