Closing the Middle-Skills Gap in the Manufacturing Industry
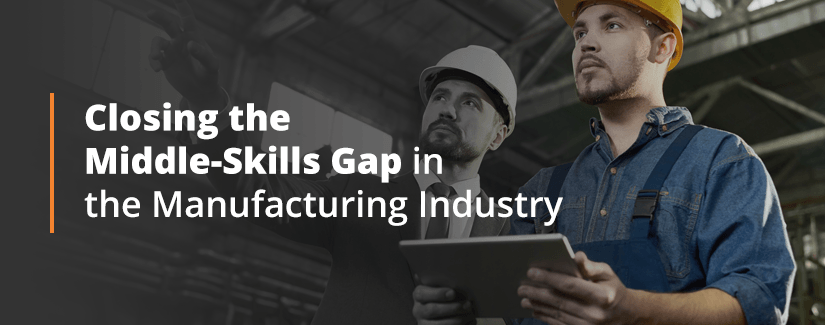
The manufacturing industry is undergoing exciting change as more companies adopt advanced technology. For example, according to a 2018 study conducted by Deloitte and The Manufacturing Institute, 50 percent of manufacturers said they adopted automation. Automation and robotics help companies produce more goods faster. Consider that manufacturing output increased by 2.9 percent in 2018, according to the Bureau of Labor Statistics.
However, the use of advanced machinery has presented a challenge to manufacturers – finding workers who have the skills needed to operate and fully use new technology. If manufacturers want to continue growing and producing at rates that meet consumer demands, they need to close the skills gap.
What can manufacturers do to find the workers they need, and why is it important to make an effort now? In this post, we’ll look at the steps companies can take to ensure they have a strong, highly skilled workforce now and in the future.
What Is the Skills Gap?
A skills gap is a term used to describe the gap between the skills needed to complete a task and the skills an employee actually has. Any employer who is having a hard time finding employees with the skills they need is experiencing a skills gap. Manufacturers, in particular, are struggling to find workers to fill middle-skills jobs. Middle-skills jobs refer to positions that require more than a high school education, but less than a four-year degree.
According to the Deloitte study, the skills gap may result in an estimated 2.4 million unfilled manufacturing jobs by 2028. This puts over $2 trillion in manufacturing gross domestic product (GDP) at risk. For manufacturers to succeed, they need skilled workers who can use the technology they have in their plant.
In the manufacturing industry, the skills gap is widening for several reasons, such as:
- New skills are needed to work with advanced technology such as programming skills and critical thinking skills.
- Americans are unaware of new manufacturing jobs, and there is a general misconception about the industry.
- Baby boomers are retiring and taking their expert technical skills and years of experience with them.
Manufacturers do not need all of their employees to have college degrees in math or science. They need workers with middle-skills who can work on the floor in collaboration with robotics and automation. For example, some production workers might need the ability to program a computer numerical control (CNC) machine on the floor. In general, manufacturers need workers who possess the following skills:
- Technology and computer skills
- Digital skills
- Programming skills for robotics and automation
- Critical thinking skills
- The ability to work with tools
Although the average worker may possess one of the above skills, many workers do not have the combination of skills needed to work with new technology. Likewise, many workers who have studied artificial intelligence or the Internet of Things in college often lack industry experience. Companies need well-rounded individuals who possess technical skills and manufacturing know-how.
Even though manufacturers face challenges regarding recruiting and retaining skilled workers, there are many ways to overcome obstacles and close the gap. Most importantly, manufacturers should prioritize finding the right employees so they can progress at full speed.
Why You Should Start Addressing the Skills Gap
The manufacturing sector is vital to the health of the U.S. economy. According to the National Association of Manufacturers (NAM), every dollar spent in manufacturing adds another $1.89 to the economy. Also, for every worker in manufacturing, another four workers are hired elsewhere. In other words, the manufacturing sector keeps the country strong, secure and thriving.
It’s critical manufacturers take steps to attract talented workers immediately because it affects the economy as a whole. Manufacturers also don’t want to risk slowing down production and being unable to meet the demands of a growing population. Lastly, companies don’t want to get left behind by technological advancements. If America wants to be a leader in manufacturing, companies must take action now.
Consider the 2016 Global Manufacturing Competitiveness Index. According to this study, China is the most competitive manufacturing nation. The U.S. is expected to take the top position by 2020. However, one of the keys to making it to the top, according to CEOs, is using advanced technology. Manufacturers rank talent as an essential driver of global manufacturing competitiveness. Competition is the force that propels innovation, growth and productivity – critical components of a booming economy.
How We Can Close the Skills Gap in Manufacturing
There are many strategies manufacturers can implement to draw and retain skilled workers. They must understand there is no instant solution to the skills gap problem, but it requires immediate attention nonetheless. In this next section, we’ll look at ways a company can build the workforce they need.
1. Identify the Skills Gap
The first step to solving any problem is identifying what the problem is. Manufacturers can perform a skills gap analysis to determine where they have talent and where they need talent in the short term and long term. Once a company knows where they need workers and specific skill sets, they can devise a plan of action.
To perform a skills gap analysis, company leaders can take these steps:
- Identify goals: Determine the skills needed in current and future employees as well as the company’s objectives.
- Gather data: List the skills and knowledge needed to fulfill specific roles, and rank them by priority. Use employee surveys, questionnaires and interviews to make assessments. Categorize employees’ skills as entry-level or master-level.
- Analyze data: List the skills current employees lack to determine the training needed.
- Construct a plan: Devise training plans to help current employees develop.
The skills gap analysis should answer questions such as:
- What skills are required for each role within the company?
- What skills do employees already possess?
- What skills are needed for future roles?
- Are employees participating in current training opportunities, and if not, why?
- What skills does the company value?
To help manufacturers envision what jobs might look like a decade from now, Deloitte created a few examples. One of these includes the job of a robot teaming coordinator (RTC). An RTC trains robots and humans to work together collaboratively. An RTC needs to possess skills in the following areas:
- Robot management
- Technical training
- Behavior analysis
- Customer service
- Administration
As you can see, a professional like an RTC needs a mix of digital and social skills to fulfill their role successfully.
2. Form Manufacturing Training Partnerships
Most parents who send their children to college believe in the “college premium.” This is the notion that four-year degrees automatically lead students to higher-than-average incomes. In reality, however, many of today’s college graduates do not earn incomes higher than their peers with less formal education. If they do, their student loan debts often keep them from experiencing the higher-than-average-income lifestyle.
Experts agree there are too many students being pushed into four-year college degrees. In fact, more affordable vocational training would likely provide better opportunities for lower-income workers and reduce overall income inequality in the United States. Vocational training programs build bridges into the manufacturing sector at each level of education. Programs also tend to be very affordable with opportunities reaching as many potential workers as possible.
Many vocational schools and manufacturing employers have adopted partnerships, using their specific training methods in these programs to grow their workforces. Some manufacturers have joined forces with other manufacturing companies to create an alliance and discuss common needs. By working together, manufacturers, both large and small, can advocate for greater support from their community and government. For example, manufacturers can work with the government to fund apprenticeship programs. This will help companies gain access to employees who were trained to fill roles involving new technologies.
3. Intend to Train New Employees
If a company waits around to hire the perfect employee, they might get left in the dust. They might also overlook employees who have potential and values that match the company. Instead of striving to find ideal workers, companies should hire employees with the intent to train them. They should look for individuals who are eager to learn and adaptable, and be ready to teach them specific skills. Training programs are an investment, but they are worthwhile. By training new employees company-specific skills, employers can build a workforce of dedicated experts. Workers who are trained within a company are also more likely to stick around.
Companies should also not overlook groups that are often underrepresented in the manufacturing industry like women, minorities, individuals with disabilities and veterans. By doing so, an employer may miss the opportunity to work with highly educated, ready-to-learn individuals.
4. Support STEM Education
The new manufacturing workforce needs skilled workers with education in science, technology, engineering and mathematics (STEM). This includes a need for data scientists, software developers and engineers. The first step to making sure there are enough STEM workers in the future is to support and encourage STEM education. Some of the ways manufacturers can support STEM include:
- Provide students with tools to design and build robots as part of a competition
- Support after-school programs that focus on STEM education
- Provide development opportunities for STEM teachers
- Support STEM opportunities for underrepresented groups like women and minorities
- Fund campaigns to bring awareness and generate interest about STEM career options
It’s important for companies and educators to encourage STEM early in school. According to the U.S. Chamber of Commerce Foundation, preschool children who develop math skills have better math skills in elementary school. Teaching children STEM skills through activities and programs will result in an increase in STEM degrees and applicants who are prepared for STEM jobs. It’s also important to reach out to students while they are young because they are still curious and have not likely developed doubts about their math or science skills.
5. Change Misconceptions
Manufacturers believe that negative views of manufacturing jobs have also led to a skills gap. The truth is, modern manufacturing is not what it used to be. Today, many manufacturers are at the forefront of innovation, using the most advanced technology in their production methods. Nevertheless, many parents and STEM students do not think of manufacturing when it’s time to choose a career path.
For example, according to a survey conducted by Deloitte and The Manufacturing Institute in 2017, fewer than five in 10 Americans believe manufacturing jobs are rewarding, clean and safe. Also, fewer than three in 10 Americans would encourage their children to pursue a manufacturing career. The majority of parents who wouldn’t encourage their children to work in manufacturing worry about job security and stability. Sixty-four percent say the jobs don’t pay enough.
What can manufacturers do to change their image? Here are some tips:
- Invest in internships, apprenticeships and certification programs, because skill-building programs appeal to Americans the most.
- Raise awareness about the benefits of working in the manufacturing industry such as high pay, strong job benefits and challenging work.
- Aim to recruit workers from pro-manufacturing demographic groups like women, Gen X Americans and individuals who are familiar with the industry.
- Offer tours of the manufacturing facility to students and the public so they can see how interesting and rewarding a manufacturing career is, and feel motivated to pursue a job in the industry.
The top three elements Americans want in a job are good benefits, better pay and rewarding work. Companies need to show Americans that manufacturing offers all of those things.
6. Focus on Retention
It’s taking longer to fill positions where there is a skills gap. For example, in 2015 it took 70 days to fill a skilled production worker position, whereas in 2018 it took 93 days. Jobs that require college degrees take an average of 118 days to fill. Hiring new workers slows a company’s ability to deliver orders and satisfy customer needs. Employers should focus on helping current employees grow and learn new skills when possible because current employees are already familiar with company values and have likely developed company-specific skills.
Here are ways manufacturers can keep employees engaged and help them grow into more advanced roles:
- Teach skills needed in the future by offering in-house training, education, cross-training and retraining where necessary.
- Pay for employees to attend conferences, workshops or pursue certificates or degrees.
- To retain highly skilled workers, offer competitive pay and benefits, such as flexible hours and paid vacation.
- Support employees’ career goals by addressing an employee’s desire to cross-train or fulfill roles in the company.
- Encourage workers to spread the word about the benefits of manufacturing jobs.
- Launch programs to retain older workers so they can contribute their skills and knowledge in some capacity after retirement.
It’s worth putting effort into training current employees. They’ll be more likely to stay if they feel engaged and challenged, and companies save time and money when they don’t have to hire new workers.
7. Try Unique Recruitment Strategies
Manufacturers can extend their reach to talented workers by thinking outside of the box when it comes to advertising job openings. Although employers should still use traditional ways of recruiting workers, such as posting job openings online or participating in job fairs, they should also try unique methods. Employers might reach potential employees through social media, or they might recruit freelance workers. Some manufacturers might consider meeting with universities to ask about qualified recent graduates. There are dozens of ways to locate and contact potential employees who have the desired skills.
Subscribe to Our Blog for the Latest Manufacturing Industry Updates
Despite the challenges manufacturers face when it comes to finding and retaining skilled workers, the future looks bright if they take immediate steps to close the gap. Consider that 83 percent of Americans believe U.S. manufacturing is vital to the country’s economic prosperity. Manufacturers are optimistic as well. Almost 90 percent have a positive outlook for their company’s future.
At Global Electronic Services, we are eager to help companies stay positive and keep growing by offering expert repair services and advice. To stay on top of the latest industry news and research, subscribe to our blog today!