Breaking Down Maintenance: Preventive vs. Corrective Approaches
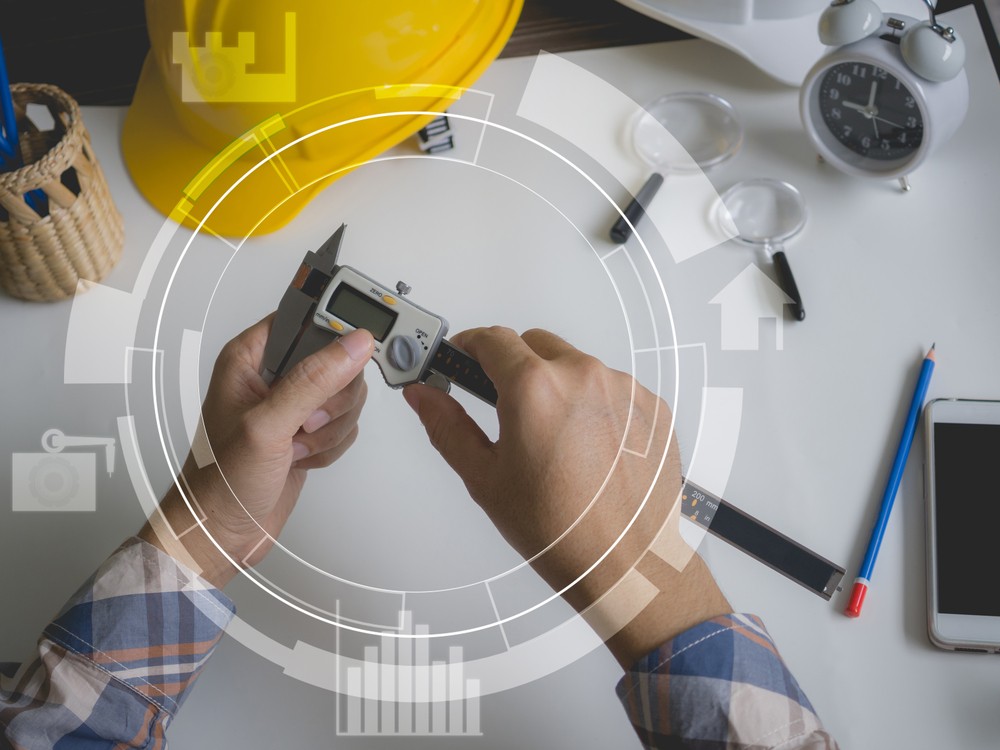
In the realm of maintenance, preventive and corrective approaches are two sides of the same coin. On one side, you administer maintenance at an upfront cost to (theoretically) prevent a larger problem from occurring later on. Corrective is the opposite: The cost is backloaded and proportionate to the solution. While preventive maintenance is unequivocally better, both have a place in factory operations.
Preventive approaches
By definition, preventive maintenance is service to a machine that’s performed to reduce the likelihood of failure. Depending on the nature of preventive maintenance, factors facilitating it could include time, condition of components, assessment of trends, and more.
- Time-based maintenance dictates service after a predetermined period of time; for example, delivering part replacements to a machine every three months, regardless of their condition.
- Failure-finding maintenance is actually a form of preventive maintenance that occurs during or after a corrective maintenance action. For example, during replacement of a failed component, the tech replaces peripheral components that haven’t yet failed.
- Condition-based maintenance is usually tied in with real-time condition monitoring technology. For example, if sensors indicate too much vibration in equipment, techs can act on repairs before failures occurs.
- Predictive maintenance is the pinnacle of preventive approaches. Using aggregate data about machine and part performance, as well as condition factors, techs make repairs to equipment ahead of failure catalysts. Historical data shows that bearings fail after 300,000 revolutions, allowing techs to replace them before that.
- Risk-based maintenance usually ties into inspections. If a component appears worn and needs servicing, a tech can choose to service it immediately or continue checking it at regular intervals in an attempt to deliver preventive maintenance closer to the point of failure.
Regardless of the type of preventive maintenance, it’s exclusively performed before issues arise. Skipping preventive maintenance is categorized as a “run-to-failure” situation, leading to demand for corrective maintenance.
Corrective approaches
A run-to-failure situation demands corrective maintenance. While not ideal, corrective maintenance is still technically a precursor to total machine failure. At this point in the process there are two types of corrective maintenance.
- Deferred maintenance is the act of delivering overdue maintenance to a machine in order to address a current breakdown, while preventing further failures. It’s a costly approach to maintenance that’s usually not purposeful but is the result of an erratic maintenance plan or understaffed maintenance team.
- Emergency maintenance is totally unplanned and unanticipated. Unlike deferred maintenance — which is usually known because it’s a deferred task — emergency maintenance requires a quick and organized response to prevent total machine failure or safety hazards.
While corrective maintenance is avoided through preventive approaches, it’s still integral to plan for these situations. Even the best maintenance plan isn’t all-encompassing. Emergency planning helps make uncertainty less erratic.
The best approach to crafting a well-rounded maintenance continuum is to consider all forms of maintenance and strategically factor them into your approach. For example, use preventive maintenance as the chief means of upkeep for your equipment, and build corrective actions into your emergency response plan. Identifying situations for all types of maintenance ensures that you’re putting every philosophy to work for the improvement of your plant’s operations.