Boeing’s Major Problems Have Roots in Poor Training Standards
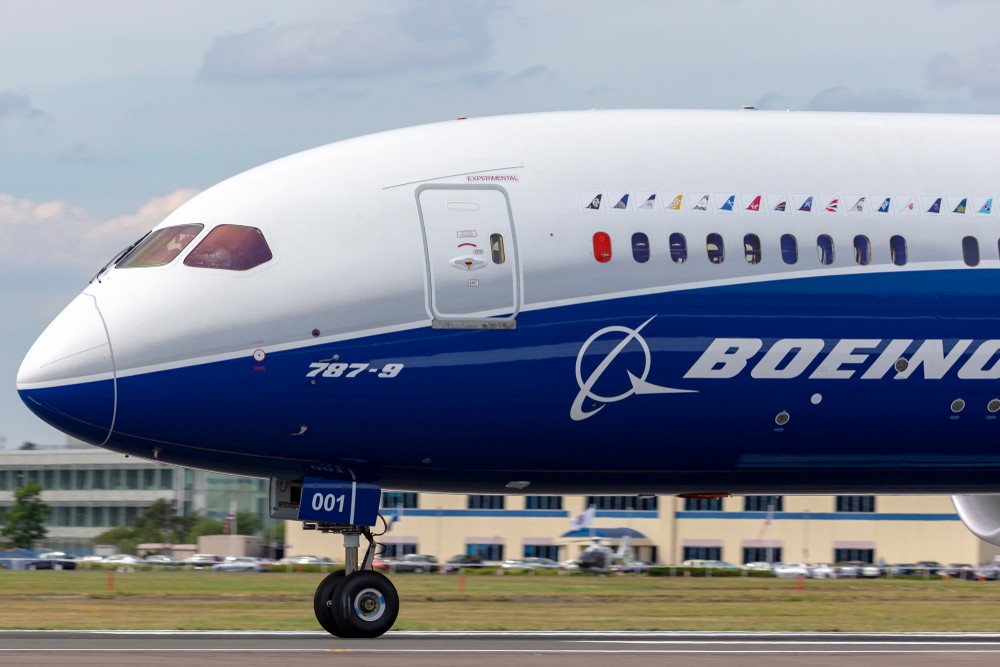
More than 350 dead and a worldwide fleet grounded. That’s the current story revolving around Boeing’s 747 Max 8 planes. Those following the story know the various factors behind the situation: hastily modified aircraft, optional and costly safety features, and collusion with the Federal Aviation Administration (FAA). But there’s one chief component that any manufacturer can and should take away from the story: Training is paramount.
A lack of training is to blame
Investigative journalism has uncovered that while poorly designed software was the catalyst for at least two of the recent fatal crashes of 747 Max 8 planes, equally to blame is the lack of training pilots received regarding this software.
Reports show that instead of formalized, simulated training, most pilots took a breezy refresher course through an iPad in less than an hour. Moreover, these modules explained little about the plane’s new software, which was designed to adjust the nose of the aircraft at higher altitudes to accommodate increased engine size.
The result? The software did what it was programmed to do, pilots reacted the way their original training dictated, and the two controlling factors ended up working against each other.
An incredible fact
Boeing’s decision — with the FAA’s blessing — was to bill the 747 Max 8 as “the same airframe with newer engines,” instead of a brand-new model. This led to lack of regulatory oversight regarding training for new features, which led to a plane that has contributed to more fatalities than any other in history over its first two years of service. It’s a record no manufacturer wants to hold.
What manufacturers should take away from this
Boeing is one of the largest manufacturers in the world. But this situation shows that no company is immune to the ramifications of cutting corners — especially when it comes to training and education.
In this situation, the problem was Boeing’s failure to properly provide training materials for pilots. On the factory floor, failing to train your employees on proper repairs and maintenance can have proportionately serious consequences. To avoid injury, bodily harm, disability, or even worse — death — factory workers need thorough training and education.
In a 2009 study titled “Does Safety Training Reduce Work Injury in the United States?” researchers Geetha M. Waehrer and Ted R. Miller undertook an impressive inspection of factory training protocols and their effect on worker safety. The study concluded that “safety training appears to be more effective in preventing severe injuries in large firms” and “formal safety training is associated with a significantly increased probability of shorter duration injuries.”
Safety first is more than a slogan
The tragedy surrounding Boeing’s 747 Max 8 planes is undeniable. And while investigations are still ongoing, all signs point to several key factors causing these fatal crashes. What we do know is that lack of training is one of the catalysts — one that could’ve helped avoid disaster if pilots had received the necessary information and training.
In an industry dominated by complex machinery and rigid safety protocols, every manufacturer needs to take heed of Boeing’s situation and understand that there’s no substitute for safety. When it comes to service and maintenance for your factory’s machinery, the best way to protect your workers is to educate them.