Best Practices for Machine Lubrication
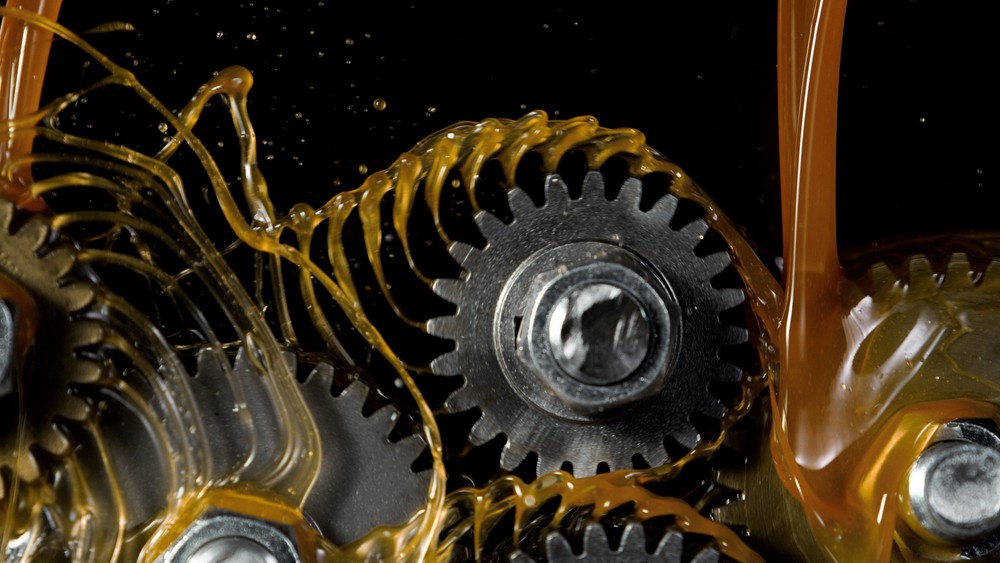
In manufacturing, lubrication is essential for reducing unwanted friction and the many problems associated with it. The smooth, uninterrupted operation of factory equipment is critical to manufacturing production efficiency and throughput. But there’s more to machine lubrication than simply greasing the gears. Lubrication science is an ever evolving, increasingly precise discipline.
To stay conscious of machine lubrication demands, and meet increasingly stringent standards, it’s critical to train technicians on best practices. Keeping up with lubrication and following core best practices will help manufacturers avoid downtime, manage unnecessary expense, and boost operational productivity.
Select the proper lubricant
The first and most essential part of keeping factory machinery running smoothly is selecting the right lubricant. There are three different classifications for lubricant: fluid (i.e., liquid), semisolid (i.e., grease), and solid (i.e., dry). There are several factors involved in choosing the right lubricant, including moisture, dust, vibration, and load size.
It’s best to observe the original equipment manufacturer’s (OEM) recommended lubrication standards whenever possible. In some cases, you may want to invest in lubrication analysis to increase technical understanding of the ideal solution for each application based on operating temperature, exposure, and other factors affecting the machine’s function. Ultimately, choosing the right lubricant for specific equipment helps to reduce machine downtime and prolong the life of factory machinery.
Have a maintenance plan in place
To avoid equipment issues and unplanned downtime, it’s important to have a good lubrication maintenance plan in place. This means knowing when and how to apply lubrication appropriately and having checks and balances in place to ensure equipment function between designated lubrication periods. Documentation is also critical, so techs can observe lubrication practices, note their effect on machinery, and make adjustments where necessary.
Avoid lubricant contamination
Lubricant contamination is a serious threat to equipment and results in component wear and eventual machine failure. The best way to avoid contamination is by properly storing and maintaining machine lubricants. Proper storage techniques for lubricants include:
- Keeping lubricants in sealed containers.
- Storing containers in a dry, clean room.
- Attaching air breathers to lubricant containers.
The best way to test oil contamination levels, for instance, is with a liquid particle counter. After the counter analyzes a sample, refer to ISO 4406 standards for information on contamination levels.
Streamline your processes
There are many ways to ensure efficiency in your factory’s lubrication approach. For example, training employees on proper lubrication techniques will prevent mistakes and streamline the process.
Designate a maintenance manager to oversee all lubrication procedures. The right manager can ensure everyone follows the lubrication maintenance plan and help technicians who have questions. They can also keep track of the nuances of a proper lubrication process, such as when it’s time to order more lubricant, when to adjust standard operating procedures, and when to update schedules.
Other techniques for streamlining the lubrication process include investing in computerized maintenance management system (CMMS) software and lubricating machines according to a comprehensive plan.
Work with an expert
Proper lubrication practices and procedures prolong machine life and ensure efficient factory operations. A lubrication maintenance expert can help manufacturers establish best practices, develop efficient processes, keep them updated on industry standards, and help choose the best lubrication approach for each situation. Lubrication is a critical facet of proper machine maintenance, and expert assistance can be an invaluable investment in your ongoing manufacturing success.