An Audit Could Help Uncover Gaps in Your Maintenance Plan
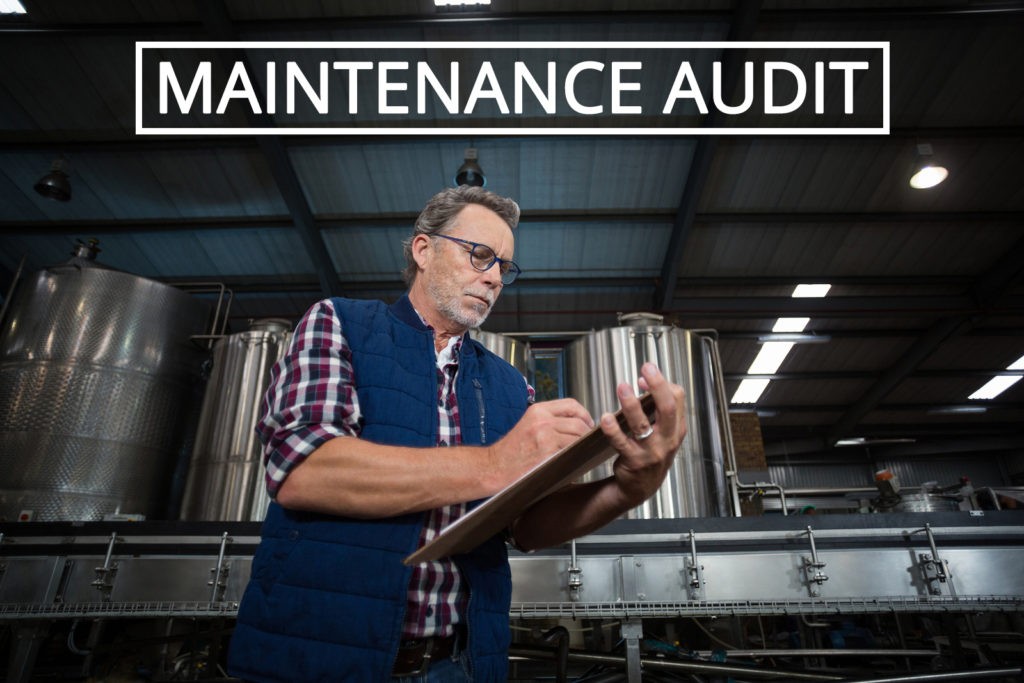
Audit is one of the most dreaded words in the manufacturing realm. Most managers instantly associate it with a time-consuming process that frivolously breaks down their operations and points out every little detail that they could improve. Well, in fact, that’s what an audit is all about: improvement.
Maintenance audits are no exception to the rule. Rather than shudder and shy away from a maintenance audit, managers would be wise to embrace and encourage them. The information gleaned from a robust audit could dramatically improve maintenance operations, making life simpler and more predictable for techs.
What’s the maintenance audit’s goal?
Like any audit, a maintenance audit’s goal is to ultimately facilitate process improvements. This audit type in particular has 5 distinct goals:
- Review maintenance processes and practices
- Benchmark maintenance best practices
- Identify opportunities to improve maintenance processes
- Identify efficiency improvements within current maintenance practices
- Better utilize maintenance resources and manpower
Each goal facilitates an overall improvement to the way your facility handles maintenance — whether it’s establishing a better way of accomplishing a specific task or implementing a system for lowering man hours.
How to execute a maintenance audit
Audits are by nature an invasive process, but that doesn’t mean they have to be disruptive to your operations. The best way to approach an audit is in stages. For a maintenance audit, this starts with the people performing maintenance tasks.
Interview maintenance personnel first, including managers, reliability engineers, training department members, health and safety supervisors, and anyone else directly involved in routine maintenance processes. Get a clear, concise understanding of what they do, when they do it, how they do it and what obstacles they face. This provides context for all other aspects of your audit.
After personnel interviews, begin to look closely at established processes and routine tasks. Determine how your personnel fit — or don’t fit — into these tasks and, more important, what the outcomes of these processes are. Leverage any data you collect to pinpoint trends in your maintenance procedure. Some examples include:
- What types of unanticipated maintenance arise most? How long do they take to fix and how are you addressing them?
- What is each maintenance staff member’s workload? Is there correlation to maintenance efficiency at this workload?
- Do you have a way of delineating unanticipated maintenance versus scheduled, routine maintenance?
Another important variable to examine during an audit is the nature of maintenance tasks: when they arise, if and how they’re anticipated, how they’re addressed, and what you’re doing to address them.
Finally, look at the equipment and resources you possess to handle maintenance demands. This could be as simple as inventorying tools and space parts or as complex as correlating scheduled man hours against maintenance log records.
A maintenance audit is worth it
The scope and intricacy of a maintenance audit may be enough to deter many managers from undertaking one, but those that stay the course could unearth insight that pays dividends. Having a clear, top-down view of how your business handles maintenance gives you license to make informed improvements that may result in everything from reduced costs to fewer down-time interruptions to a better standard of work for your employees.
Audit may strike fear into the heart of most manufacturers, but for maintenance managers, it’s a chance to shore up any practices or processes that just aren’t working.