Archiving and Updating Maintenance Documentation
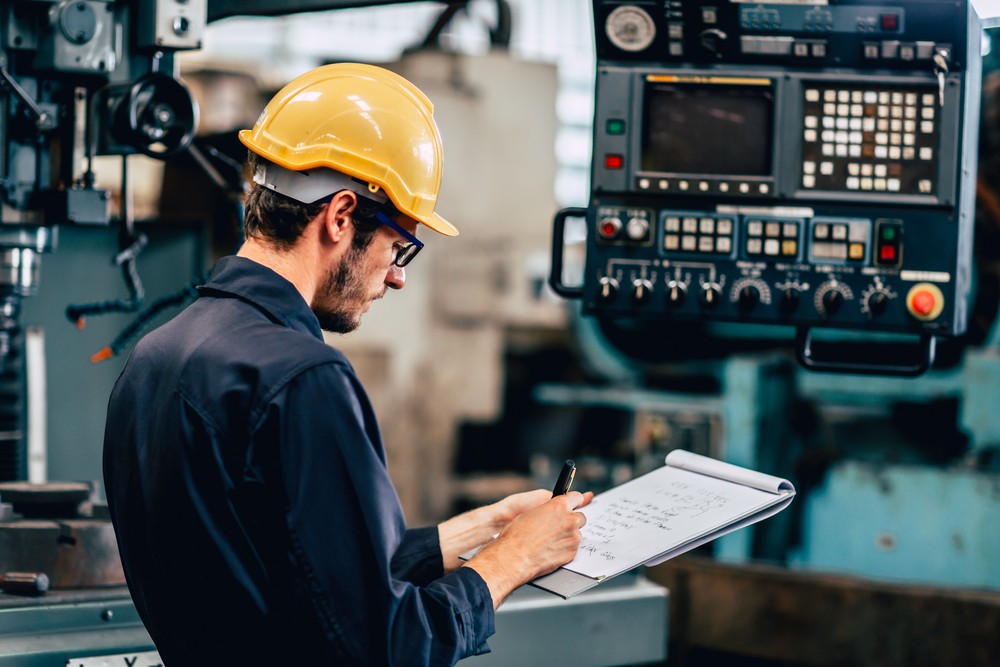
Outdated or lost maintenance documentation can be a recipe for disaster. Imagine a critical piece of equipment failing, but the maintenance crew lacks clear instructions on how they should troubleshoot or replace the faulty components — or what previous repairs were administered. Valuable time might be wasted searching for information as the risk of further damage increases.
Maintenance documentation should always be at your fingertips. Let’s delve into how you can build a robust archiving system for maintenance documentation, along with strategies for keeping it up to date.
Standardize data documentation
Before looking at sorting and archiving maintenance records and service logs, it’s important to develop systems for standardizing data capture and documentation. That way, records aren’t just easy to find; they’re also easy to understand.
Take the opportunity to delineate the different types of documentation. While you’ll likely keep system records together while archiving, recognize the different types of documentation you have:
- Procedures: Detailed instructions for all routine and preventive maintenance tasks
- Schedules: Clear schedules for maintenance, including recommended frequencies
- Parts inventory: Lists of spare parts and their corresponding part numbers for each system
- Troubleshooting guides: Step-by-step guides for resolving common system issues
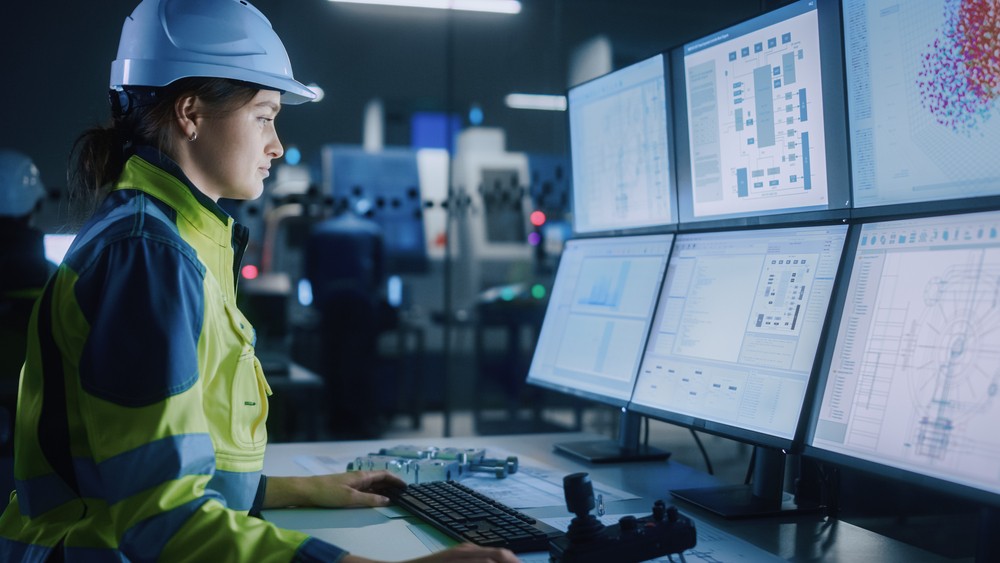
Maintain current documentation
Just as important as archiving is keeping documentation current. After any maintenance activity, changes to the system, or identification of a new troubleshooting step, these updates need to be documented. Quality management systems like ISO 9001 can help implement systems for ongoing documentation updates.
The responsibility for updating documentation can be assigned to the maintenance crew or engineers, depending on the organization’s structure. This might involve recording details such as:
- Parts replaced (including part numbers and reasons for replacement)
- Procedures modified (with clear explanations for the changes)
- New troubleshooting steps discovered
Most digital platforms offer revision history features, allowing you to track changes made over time.
Use archived documentation
Effectively archiving and updating maintenance documentation is an investment that pays off in the long run. Some of the benefits of readily accessible and up-to-date maintenance documentation include:
- Faster completion and fewer errors for maintenance tasks
- Reduced training time and improved training best practices
- Streamlined troubleshooting and more efficient resolutions
- Better knowledge retention within the team
Remember, readily available, up-to-date knowledge empowers your team to keep your systems running smoothly and efficiently, contributing to a productive and successful manufacturing environment.
Save on Fanuc repairs
As you’re archiving and updating maintenance documentation for Fanuc equipment, keep in mind our May special on Fanuc repairs. Get 15% off repairs on any order of three or more items, or get 10% off a single Fanuc repair. Use code MAYFANUC at checkout to claim your discount.