AC Motor Bearing Failures: Causes and Prevention
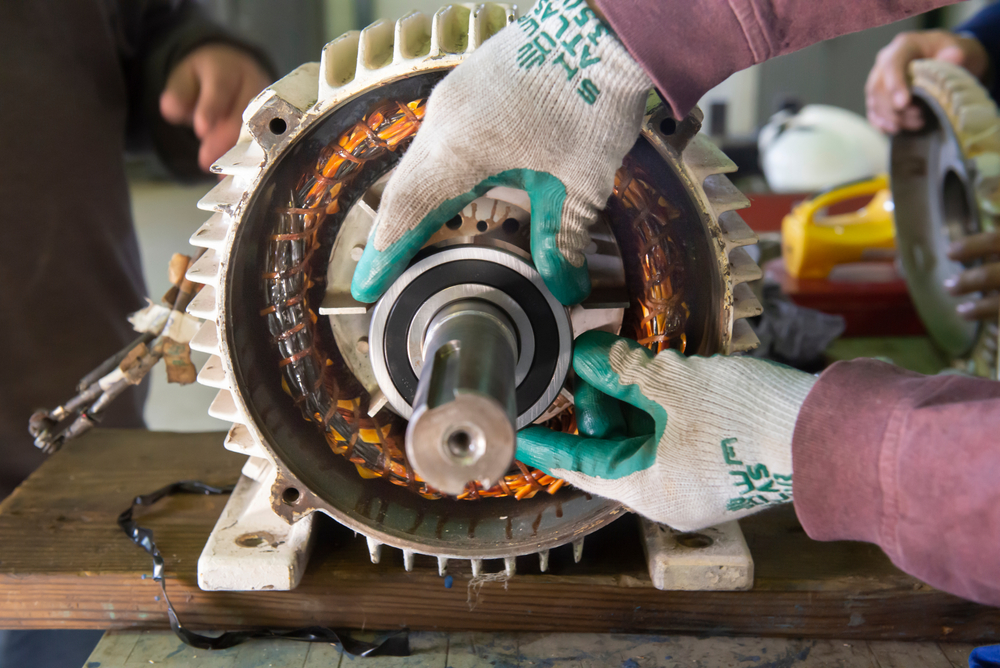
While AC motors power countless industrial processes, their reliability hinges on one often-overlooked component: bearings. A single failing bearing can halt an entire production line. Understanding why bearings fail — and how to prevent these failures — can save you substantial time and money. It starts by understanding the common culprits behind bearing degradation.
Common culprits behind bearing damage
Improper lubrication is often the primary cause of premature bearing wear. Too much grease creates excess heat and pressure, while too little results in metal-on-metal contact. Both scenarios accelerate bearing deterioration and can reduce bearing life by up to 50%.
Misalignment issues are another common issue that creates uneven stress distribution across bearing components. Even slight shaft misalignment forces bearings to handle loads they weren’t designed for, reducing their lifespan dramatically. Studies show that a misalignment of just 0.002 inches can cut bearing life by a third! This is exacerbated by contamination, as airborne particles from production processes can infiltrate even well-protected bearings. Once they breach bearing seals, they create microscopic damage that compounds over time.
Electrical discharge also poses a unique threat to AC motor bearings. Stray currents can arc through the bearing, creating tiny pits in the metal surfaces. These pits multiply rapidly, leading to premature failure. Variable frequency drives often amplify this problem, making proper grounding an important step.
Problems with motor bearings?
In addition to AC motor bearings, now through the end of January, GES is offering 10% OFF single repairs and 15% OFF 3+ repairs on all servo motors. We’re here to keep your industrial equipment operational and reliable!
Smart prevention strategies that work
With so many simple threats to bearing integrity, it might come as no surprise that equally simple preventive measures can dramatically extend bearing life and prevent costly failures. Here’s what works:
- Regular vibration analysis catches problems early. Modern vibration monitoring systems can detect subtle changes in bearing performance long before catastrophic failure occurs.
- Proper lubrication schedules matter. Each bearing type needs specific amounts of the right lubricant at the right intervals. Documentation and strict adherence to these schedules prevent many common failures.
- Quality seals and proper installation make a difference. Installing high-grade seals and following manufacturer specifications for bearing installation creates a strong foundation for long-term reliability.
- Shaft alignment requires precision. Using laser alignment tools during installation and maintenance ensures bearings operate within their design parameters. Regular alignment checks should be standard procedure.
- Temperature monitoring adds protection. Bearing temperature trends can reveal developing problems. Infrared cameras and permanent temperature sensors provide valuable early warning signs of bearing stress.
Taking action saves money
A proactive maintenance strategy focused on bearing health pays for itself many times over. By implementing proper monitoring, maintenance, and installation practices, manufacturers can significantly extend motor life and reduce unexpected downtime. Studies show that predictive maintenance programs can reduce bearing-related failures by up to 70%.
Building a comprehensive bearing maintenance program requires investment in tools, training, and time. Still, compared to the cost of emergency repairs and lost production, prevention offers clear financial advantages. Remember: bearings might be small, but their impact on manufacturing efficiency is enormous. Protecting them protects the bottom line.