A History of the American Manufacturing System
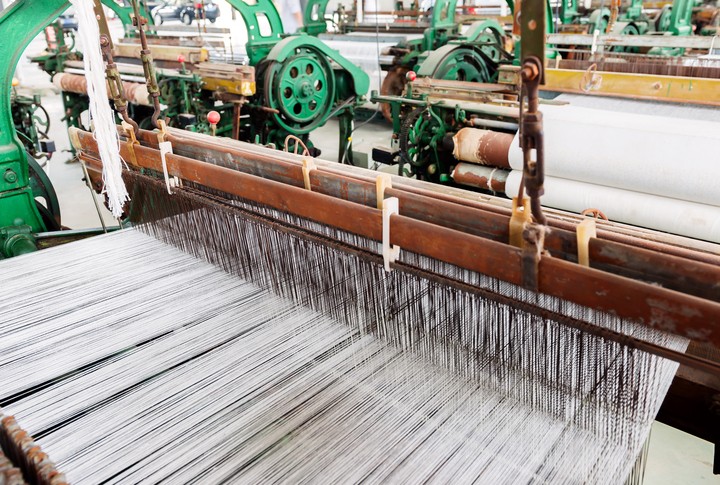
Manufacturing has evolved over the centuries with key strategic additions from various groups. Prefabrication has been a manufacturing technique for millennia. Guilds date back as far as the 11th century when tradesmen created rudimentary business networks to control the production and practice of their craft. The Ford Motor Company introduced the assembly line, fabricating cars piece by piece. Japan introduced just-in-time manufacturing, also known as short-cycle manufacturing, to reduce flow times and keep overhead low by only producing what was needed when it was needed. Manufacturing has been shaped and reshaped continuously, and the American system of manufacturing added to it in several ways.
For a bit of background, the American system was first adapted in U.S. armories so that weapons could be more easily repaired and more quickly built during wartime. Before then, skilled machinists were needed to produce parts and they were never quite identical. Some notable techniques from the introduction of the American system include:
Interchangeable Parts
The system focused on the use of machine jigs and tools to make identical, interchangeable parts. This was developed primarily for the textile industry, and its benefits were many:
- Manufacturing could be separated from actual assembly, leading to the semi-skilled laborers of the assembly line
- Fitting time was reduced since parts were manufactured to an exact, consistent tolerance
- Production time could be sped up due to specialized parts aiding the process – e.g. fixtures to hold textiles in place during weaving
Mechanization
The rise of specialized machines to create exact parts and tools for particular segments of the manufacturing process meant the need for skilled manual labor became less and less. This led to:
- Reduced production times
- Consistent output
- Reduction in labor costs
Division of Labor
The need to train and retain workers who were highly skilled in the entire manufacturing process was no longer there. Unskilled workers could be quickly trained to handle just one portion of the process, which allowed companies to hire from a broader worker base.
Manufacturing continues to evolve based on the processes introduced in past generations. Manufacturing systems are now lean, reconfigurable and adaptable. Specialized parts continue to be built for specific parts of the process. Prefabrication has grown to touch every part of the logistics network. 3D printing allows one-of-a-kind parts. The list goes on and on. Where do you think the next big innovation in manufacturing will be?
Please share your comments or questions with us below and be sure to visit gesrepair.com or call us at 1-877-249-1701 to learn more about our services. We’re proud to offer Surplus, Complete Repair and Maintenance on all types of Industrial Electronics, Servo Motors, AC and DC Motors, Hydraulics and Pneumatics. Please subscribe to our YouTube page and Like Us on Facebook! Thank you!