6 Signs of Voltage Imbalance in Three-Phase Motors
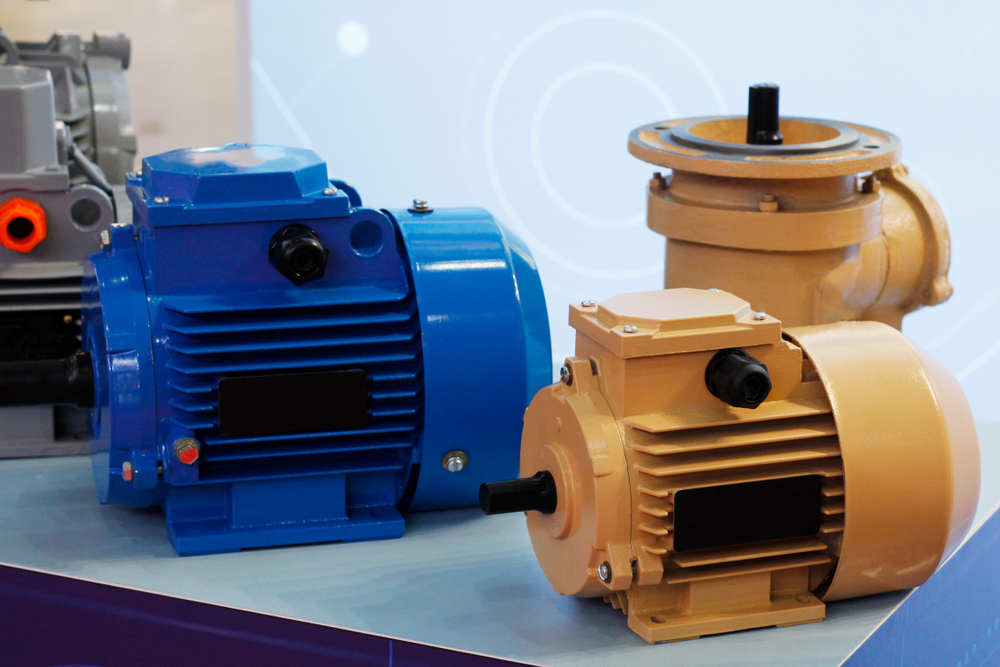
Voltage imbalance is one of those silent problems that doesn’t always show itself right away. One phase lags behind the others and the motor keeps running… until it doesn’t. By the time the damage becomes obvious, you could be dealing with overheated windings and premature motor failure.
Small voltage variations may not seem like a big deal, but they create uneven current loads, stressing some windings more than others. The sooner you catch the signs, the better your chances of preventing major damage. Here are six indicators to watch out for.
1. The motor is running hotter than usual
Excess heat is one of the earliest red flags. A voltage imbalance forces certain windings to work harder than others, creating localized overheating. Insulation degrades faster, bearings wear down, and the risk of failure skyrockets. Use an infrared thermometer to check for unexpected hot spots and compare winding temperatures — if one phase consistently runs hotter, imbalance is a likely cause. If a motor is overheating without an obvious reason, check phase-to-phase voltage readings.
2. Trips and shutdowns keep happening
A motor that shuts down randomly (or worse, repeatedly) may not have a mechanical issue at all. Drives and overload relays detect voltage imbalances and will trip to protect the motor. Compare shutdown logs with voltage data to see if there’s a pattern. Remember, voltage issues can change throughout the day, so be sure to take readings at different times to track fluctuations. If trips occur even when the motor isn’t under heavy load, imbalance is a strong suspect.
3. The motor doesn’t sound right
A healthy three-phase motor should produce a smooth, steady hum. If the motor starts sounding rough, labored, or inconsistent, voltage imbalance could be disrupting its normal operation. Buzzing or grinding under load often points to electrical stress. Excess vibration may also develop as the motor struggles to maintain even torque. If belts, bearings, or couplings wear out faster than expected, imbalance could be the reason.
4. Current readings are uneven
A three-phase motor should draw relatively balanced current across all three phases. When voltage levels vary, current draw becomes uneven, putting extra stress on some windings while leaving others underutilized. Take current measurements across all three phases — a difference of more than 10% suggests a problem. Check for overcurrent warnings on motor controllers or drives, too. And, if power factor correction capacitors are in place, ensure they’re properly sized and tuned.
5. Power consumption is rising
If energy costs are climbing without an obvious increase in production, an imbalance could be forcing the motor to work harder than it should. A sudden rise in power consumption with no operational changes is a major red flag. Motors in similar applications should have comparable energy usage — if one is drawing significantly more, check the voltage supply. A slow decline in efficiency ratings over time could also indicate worsening imbalance.
6. Windings show signs of premature wear
If voltage imbalance goes unchecked, it accelerates insulation breakdown, causes internal arcing, and eventually leads to winding failure. Regular insulation resistance tests can reveal early degradation. Discoloration or burn marks on winding connections also tend to point to electrical stress. If windings in one phase consistently fail first, voltage imbalance is a likely culprit.
Voltage imbalance that won’t quit? It’s time for a deeper fix.
If voltage imbalance keeps showing up despite adjustments, deeper electrical faults — like failing transformers, unstable supply lines, or internal motor damage — could be the real issue. The experts at GES diagnose and repair voltage-related failures, restoring your motors to peak performance before bigger problems arise. And, now through the end of the month, we’re offering 10% OFF single repairs or 15% OFF 3+ repairs on ABB products, including single and three phase TEFC motors.